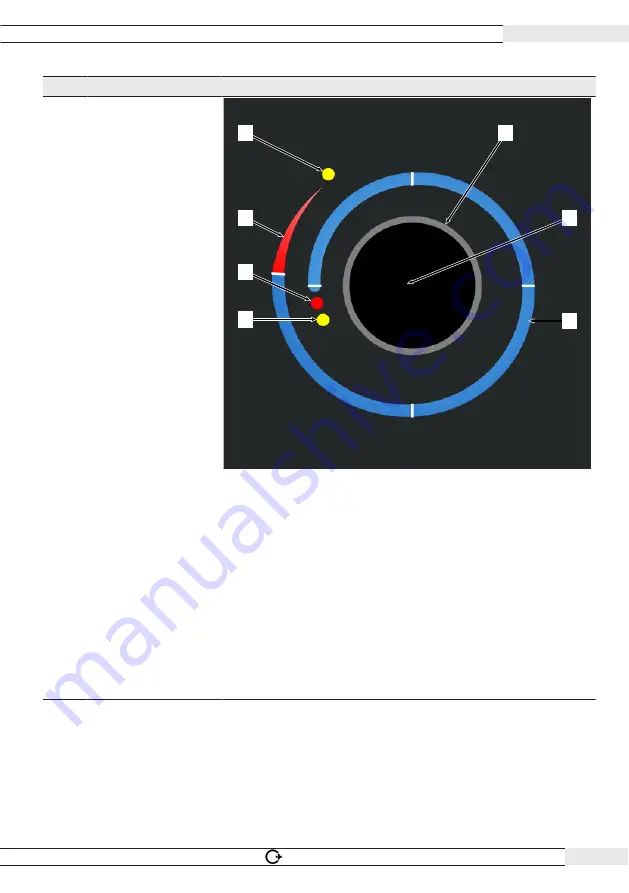
MOBILE WELDER OC PLUS
ENGLISH
ORBITALUM TOOLS GmbH
, D-78224 Singen www.orbitalum.com
69
NO.
DESIGNATION
FUNCTION
20
Welding procedure
process graphic
1
2
3
4
5
6
7
In the main menu, the process graphic shows the structure of the cur-
rently loaded welding procedure and its progress in a clockwise direc-
tion.
It adapts dynamically depending on the number of segments and
segment length, as well as on the welding parameters of the respec-
tive active welding procedure.
During the welding process, it is used to determine the position of the
electrode and to display the current welding process.
In the main menu, the process graphic is also a touch-actuated action
field that can be used to access the welding parameter levels of the
different segments in order to change their parameters. To do this,
touch the respective area on the monitor.
Содержание MOBILE WELDER OC PLUS
Страница 8: ...ENGLISH MOBILE WELDER OC PLUS 8 ORBITALUM TOOLS GmbH D 78224 Singen www orbitalum com ...
Страница 20: ...ENGLISH MOBILE WELDER OC PLUS 20 ORBITALUM TOOLS GmbH D 78224 Singen www orbitalum com ...
Страница 177: ...MOBILE WELDER OC PLUS ENGLISH ORBITALUM TOOLS GmbH D 78224 Singen www orbitalum com 177 ...
Страница 200: ...SPARE PARTS MOBILE WELDER OC PLUS 200 ORBITALUM TOOLS GmbH D 78224 Singen www orbitalum com ...
Страница 204: ......