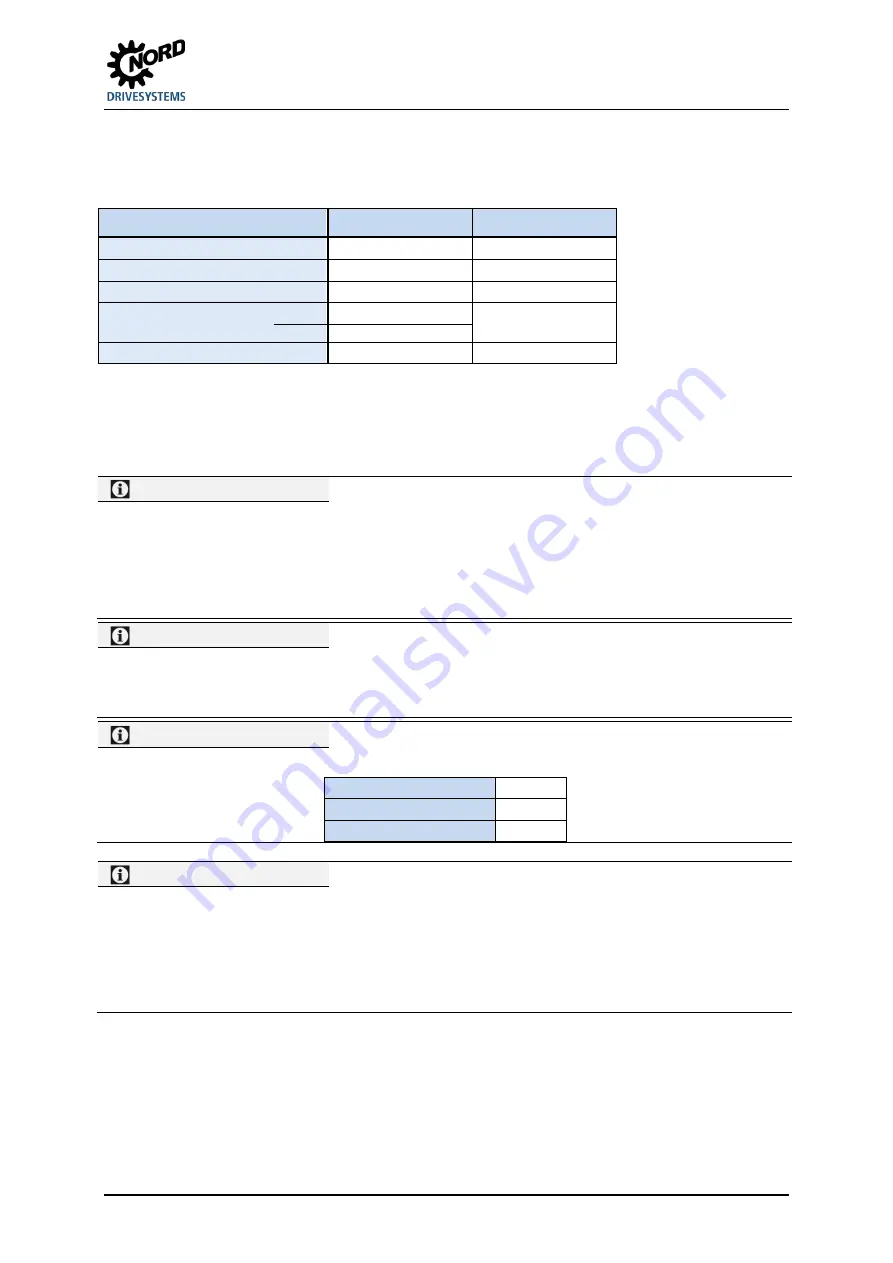
2 Assembly and installation
BU 0180 en-4118
49
2.4.3 Electrical connection of the control unit
Connection data:
Terminal bar
X3
X4, X5
Cable Ø *
[mm²]
0.2 … 1.5
0.2 … 1.5
Ø cable *
[mm²]
0.2 … 0.75
0.2 … 0.75
AWG standard
24-16
24-16
Tightening torque
[Nm]
0.5 … 0.6
Clamping
[lb-in]
4.42 … 5.31
Slotted screwdriver
[mm]
2.0
2.0
*
Flexible cable with wire-end ferrules,
without
plastic collar or rigid cable
**
Flexible cable with wire-end ferrules with plastic collar (for cable cross-section 0.75 mm², a wire-end
ferrule with a length of 10 mm must be used)
The device generates its own control voltage and provides this to terminal 43 (e.g. for connection of
external sensor systems).
Information
Control voltage overload
A control unit overload caused by impermissibly high currents may destroy the unit. Impermissibly high currents
occur if the total current that is actually withdrawn exceeds the permissible total current.
The control unit can also be overloaded and destroyed if the 24 V DC supply terminals of the device are
connected to a different voltage source For this reason, particularly when installing connectors for the control
connection, it must be ensured that any cores for the 24 V DC power supply are not connected to the device but
are insulated accordingly (example of connector for system bus connection SK TIE4-M12-SYSS).
Information
Total currents
If necessary, 24 V can be drawn from several terminals. This also includes e.g. digital outputs or an operating
module connected via RJ45
The total current which is drawn off must not exceed 150 mA.
Information
Reaction time of digital inputs
The reaction time of a digital signal is approx. 4-5 ms and consists of the following:
Scan time
1 ms
Signal stability check
3 ms
Internal processing
< 1 ms
Information
Cable laying
All control cables (including thermistors) must be routed separately from the mains and the motor cables to
prevent interference in the device.
If the cables are routed in parallel, a minimum distance of 20 cm must be maintained from cables which carry a
voltage of > 60 V. The minimum distance may be reduced by screening the cables which carry a voltage, or by
the use of earthed metal partitions within the cable conduits.
Alternative: Using a hybrid cable with shielding of the control lines.
Содержание SK 180E Series
Страница 1: ...BU 0180 en NORDAC BASE SK 180E SK 190E Users Manual for Frequency Inverters...
Страница 4: ...NORDAC BASE SK 180E SK 190E Users Manual for Frequency Inverters 4 BU 0180 en 4118...
Страница 185: ...8 Additional information BU 0180 en 4118 185 8 3 4 EU Declaration of Conformity...
Страница 211: ...Key word index BU 0180 en 4118 211...
Страница 212: ...6071802 4118...