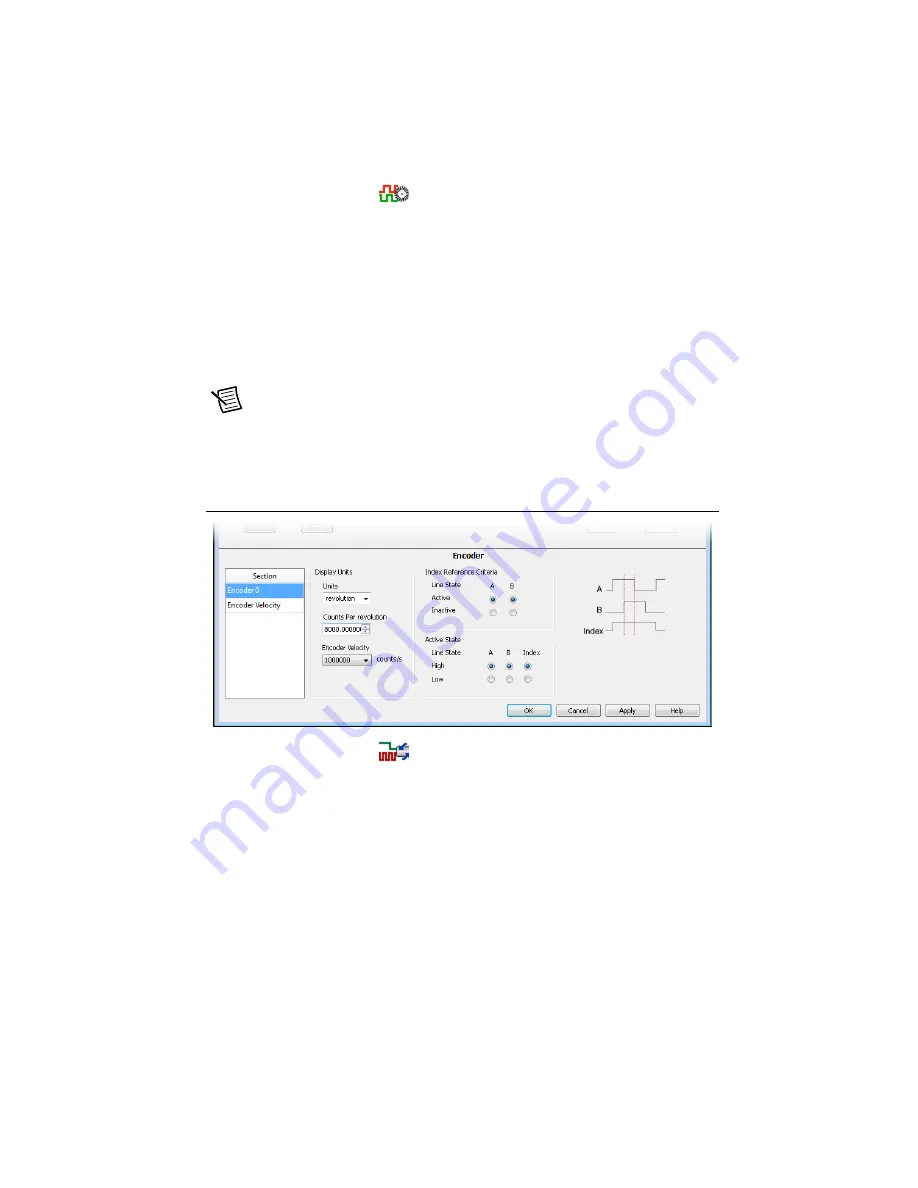
Getting Started with NI 9512 Modules and AKD Servo Drives
|
© National Instruments
|
21
3.
Click the Encoder button (
) and configure the Units and Counts Per Unit.
a.
In the
Active State
section set the
Line State
for
A
,
B
, and
Index
to
High
.
b.
In the
Index Reference Criteria
section set the
Line State
for
A
and
B
to
Active
.
c.
Select
rev
from the
Units
text box, or type
revolutions
if you prefer.
d.
Set the
Counts per Unit
to 8,000. This setting is the encoder resolution in quadrature
counts per revolution and must correspond to the AKD WorkBench emulated encoder
output
Resolution
setting in lines per revolution multiplied by four. You may want to
choose a different resolution depending on your application needs. A setting of 8,000
assumes an AKD WorkBench Emulated Encoder output
Resolution
setting of 2,000
lines per revolution.
Note
You configure the emulated encoder output
Resolution
setting in
Install AKD WorkBench and Configure the Drive
When you are finished the Encoder Settings page will look similar to Figure 15.
Figure 15.
Axis Configuration Encoder Page
4.
Click the
Stepper
button (
) to open the
Stepper
page.
a.
Ensure that the Stepper Output settings match the following:
•
Output Mode
—Step/Direction
•
Output Type
—Single-Ended
•
Active State
—Active Low
b.
Configure the Units and Steps Per Unit.
•
Select
rev
from the
Units
text box, or type
revolutions
if you prefer.
•
Set
Steps Per revolution
to 8,000.
Содержание NI 9512 C Series
Страница 1: ...NI 9512...