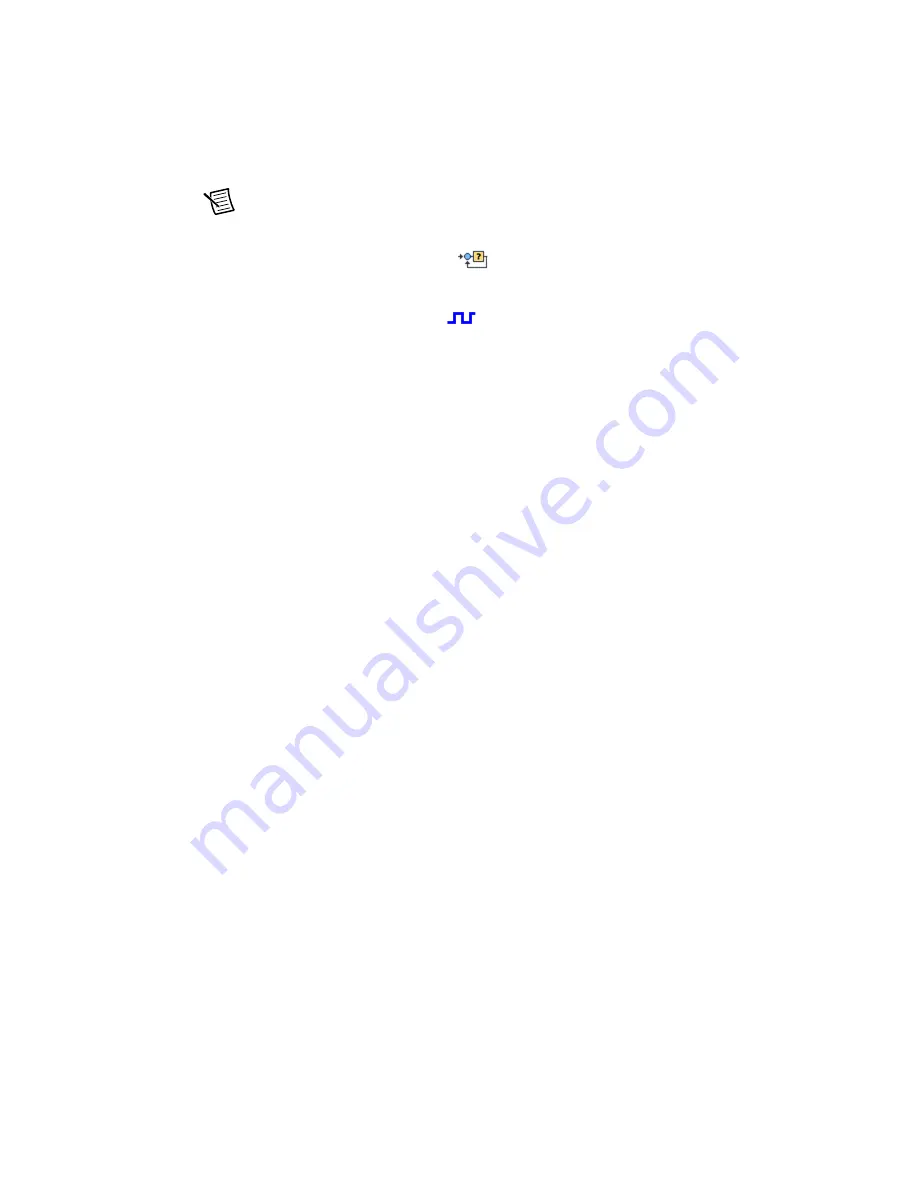
22
|
ni.com | Getting Started with NI 9512 Modules and AKD Servo Drives
Note
The
Steps Per revolution
setting
must
match the AKD WorkBench
Feedback 2 Resolution
Step 5: Install AKD WorkBench and
.
c.
(Optional) Click the
Monitor
button (
) and enable the
Enforce Position Error
Limit
checkbox. This causes NI SoftMotion to disable the drive and turn off the Drive
Enable signal when the specified position error limit is exceeded.
5.
(Optional) Click the
Digital I/O
button (
) to open the
Digital I/O
page and map the
following optional status inputs.
a.
Complete the following steps to map DI 1 (DSUB Pin 8) to
Drive Fault/Alarm
. When
the
Drive Fault/Alarm
signal is active, the module does not generate command
signals.
1)
Double-click the text in the
Mapping
column and select
Drive Fault/Alarm
from the dropdown list.
2)
Ensure that the DI 1 settings match the following:
•
Input Type
—Sinking
•
Active State
—Off
•
Digital Filter
—50 µs
b.
Complete the following steps to map DI 2 (DSUB Pin 4) to
Servo/Drive Ready
. This
signal is active when the drive is enabled.
1)
Double-click the text in the
Mapping
column and select
Servo/Drive Ready
from the dropdown list.
2)
Ensure that the DI 2 settings match the following:
•
Input Type
—Sourcing
•
Active State
—On
•
Digital Filter
—50 µs
c.
Complete the following steps to map DI 3 (DSUB Pin 3) to
In-Position
. The
In-Position
signal from the AKD servo drive is active when the current position is
within a user-specified distance from the target position. This distance is set in
Install AKD WorkBench and Configure the Drive
when the
Position Error Monitor
output is configured.
1)
Double-click the text in the
Mapping
column and select
In-Position
from the
dropdown list.
2)
Ensure that the DI 3 settings match the following:
•
Input Type
—Sourcing
•
Active State
—On
•
Digital Filter
—50 µs
Содержание NI 9512 C Series
Страница 1: ...NI 9512...