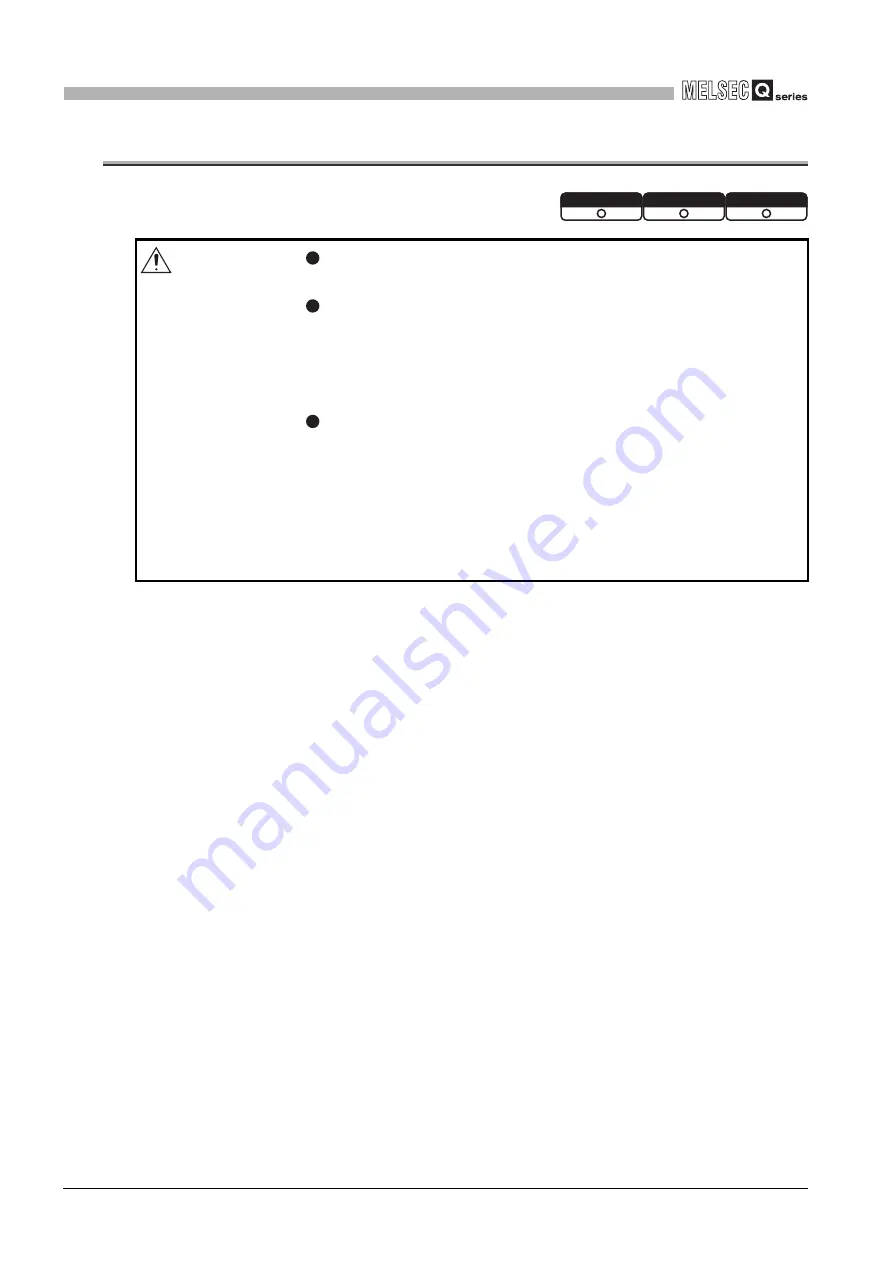
6
- 92
6.12 Maintenance and Inspection
6
PREPARATORY PROCEDURES AND SETTING
6.12 Maintenance and Inspection
WARNING
Do not touch any terminal while power is on.
Doing so will cause electric shock.
Correctly connect the battery connector.
Do not charge, disassemble, heat, short-circuit, solder, or throw the
battery into the fire.
Doing so will cause the battery to produce heat, explode, or ignite,
resulting in injury and fire.
Shut off the external power supply for the system in all phases
before cleaning the module or retightening the terminal screws or
module fixing screws.
Undertightening the terminal screws can cause short circuit or
malfunction.
Overtightening can damage the screw and/or module, resulting in
drop, short circuit, or malfunction.
Q12DCCPU-V
Q06CCPU-V
Q06CCPU-V-B
Содержание Q06CCPU-V
Страница 2: ......
Страница 612: ...APPX 48 Appendix 11 Functions Added by Version Upgrade APPENDICES Memo ...
Страница 617: ......