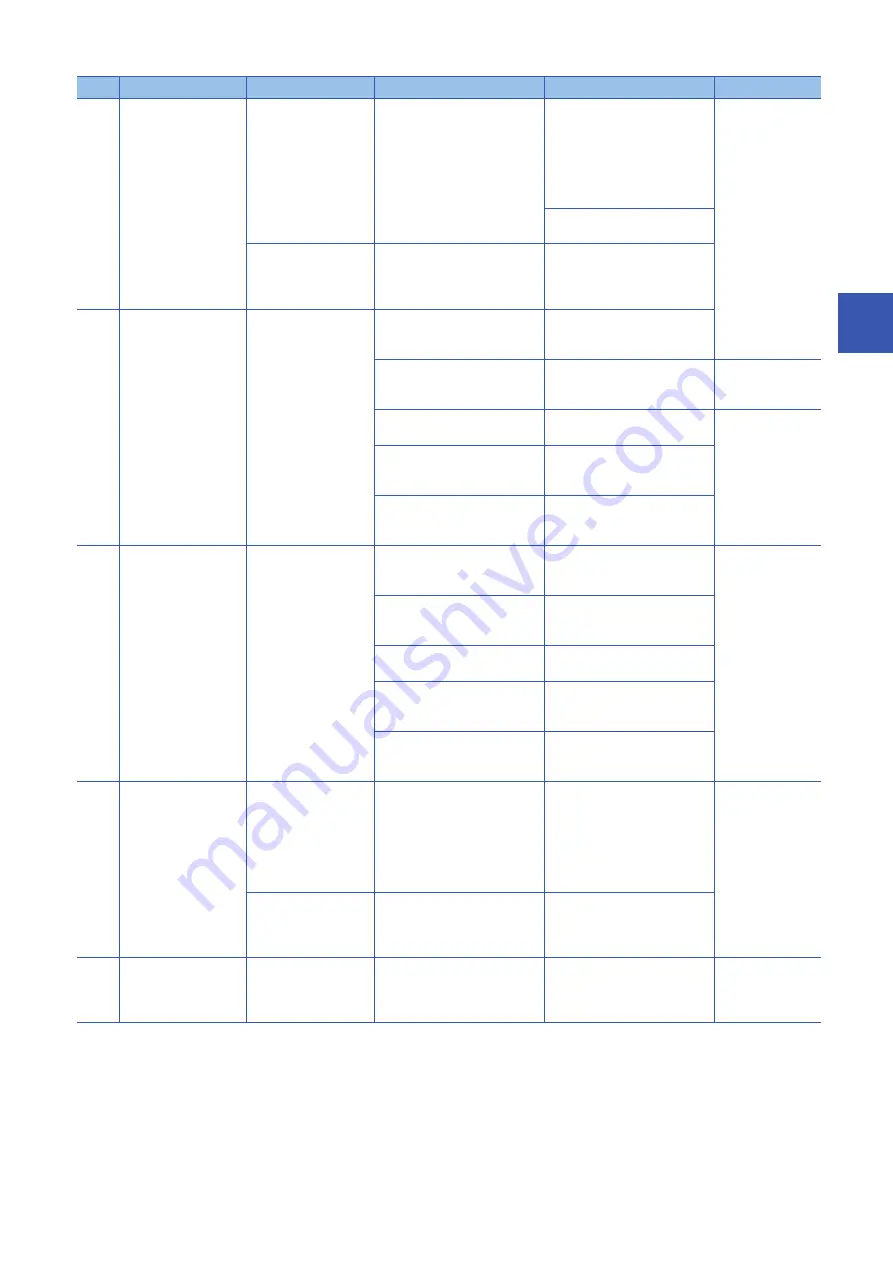
4 STARTUP
4.3 Troubleshooting at startup
55
4
3
Operation of the servo
motor alone by
command
(Position control mode)
The servo motor does
not operate.
Check the cumulative command
pulses on the status display.
1. The wiring is incorrect.
• For the open collector pulse
train input, 24 V DC power is
not supplied to OPC.
• LSP and LSN are not on.
2. A pulse is not inputted from the
controller.
The setting in [Pr. PA13] is
incorrect.
The servo motor
operates in the opposite
direction.
Check the cumulative command
pulses on the status display.
1. The wiring to the controller is
incorrect.
2. The setting in [Pr. PA14] is
incorrect.
4
Operation of the servo
motor alone by
command
(Speed control mode)
The servo motor does
not operate.
Check the input voltage of VC
(Analog speed command) on the
status display.
The analog speed command is 0
V.
Check the on/off status of input
signal with the external I/O signal
display.
LSP, LSN, ST1, and ST2 are off.
Check [Pr. PC05 Internal speed 1]
to [Pr. PC11 Internal speed 7].
The setting is "0".
Refer to "Speed
control mode (S)" in
the following
manual.
MR-J5 User's
Manual (Function)
Check [Pr. PA11 Forward rotation
torque limit] and [Pr. PA12
Reverse rotation torque limit].
The torque limit level is too low
against the load torque.
When TLA (Analog torque limit) is
usable, check the input voltage on
the status display.
The torque limit level is too low
against the load torque.
5
Operation of the servo
motor alone by
command
(Torque control mode)
The servo motor does
not operate.
Check the input voltage of TC
(Analog torque command) on the
status display.
The analog torque command is 0
V.
Refer to "Torque
control mode (T)" in
the following
manual.
MR-J5 User's
Manual (Function)
Check the on/off status of input
signal with the external I/O signal
display.
RS1 and RS2 are off.
Check [Pr. PC05 Internal speed 1]
to [Pr. PC11 Internal speed 7].
The setting is "0".
Check the value of [Pr. PC13
Analog torque command
maximum output]
The torque command level is too
low against the load torque.
Check [Pr. PA11 Forward rotation
torque limit] and [Pr. PA12
Reverse rotation torque limit].
The setting is "0".
6
Gain adjustment
Ripples (speed
fluctuations) are large at
low speed.
Follow the procedure shown
below when adjusting the gain.
1. Improve the auto tuning
responsiveness.
2. Repeat acceleration/
deceleration three times or more
to complete the auto tuning.
Faulty gain adjustment.
MR-J5 User's
Manual
(Adjustment)
Large load inertia
moment causes the
servo motor shaft to
oscillate side to side.
If the servo motor can be run
safely, repeat acceleration/
deceleration three times or more
to complete the auto tuning.
Faulty gain adjustment.
7
Actual operation
Position mismatch
occurs
Confirm the cumulative command
pulses, cumulative feedback
pulses, and actual servo motor
position.
Pulses are miscounted due to
noise and other factors.
Investigating the
cause of a position
mismatch
No.
Startup sequence
Fault
Investigation
Possible cause
Reference
Содержание Melservo MR-J5-A
Страница 1: ...MR J5 A User s Manual Introduction MR J5 _A_ Mitsubishi Electric AC Servo System ...
Страница 2: ......
Страница 75: ...6 COMPLIANCE WITH GLOBAL STANDARDS 6 5 Compliance with the China RoHS directive 73 6 MEMO ...
Страница 79: ......