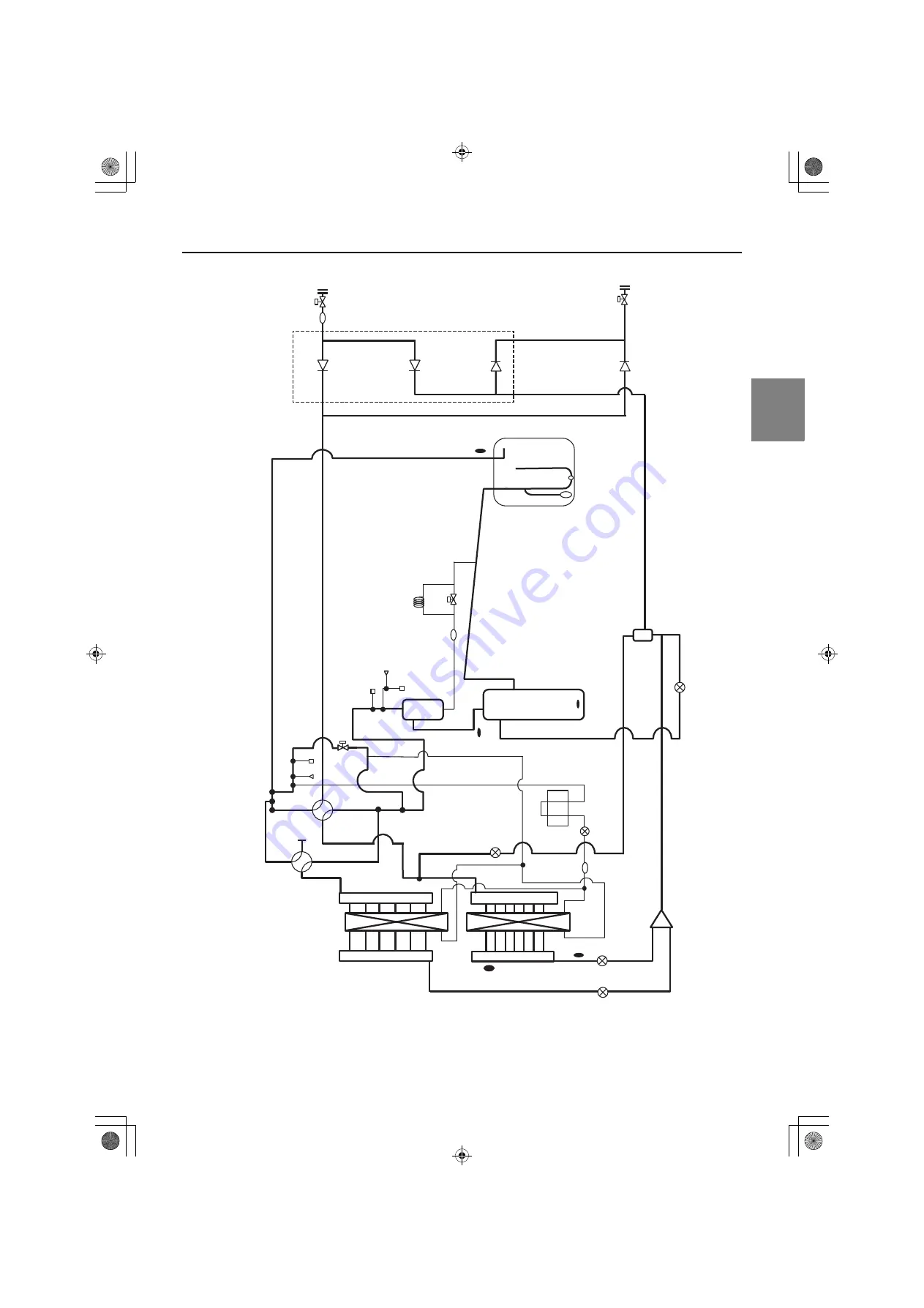
[3-2 Outdoor Unit Refrigerant Circuit Diagrams ]
BS_03_L
chapter 3 -
9
3 Major Compon
ent
s
, Their Fun
ct
io
ns
a
n
d
Re
frig
e
ra
n
t
Circ
ui
ts
(2) PURY-EM200 - EM300YNW-A1
SV
1
a
Gas-liquid separator
63H
1
ST
3
ST
6
TH
4
21S
4
b
CP
1
CJ
1
63L
S
ST
1
BV2
BV1
AC
C
Co
m
p
O/
S
21S
4
a
LE
V2
a
LE
V2
b
LE
V4
SV
2
HE
X
LE
V2
d
CV
2
a
CV
3
a
CV
5
a
CV
6
a
TH
5
LE
V9
Hex for INV
cooling
ST
1
8
CJ
2
63H
S
1
TH
15
ST
7
TH
3
TH
7
CH
E
C
K
V
A
L
V
E
B
L
O
C
K
0000006412.BOOK 9 ページ 2021年10月12日 火曜日 午後4時33分
Содержание City Multi PURY-EM200YNW-A1
Страница 1: ......
Страница 11: ...GB_BS_01_L 0000006448 BOOK 2 ページ 2021年10月6日 水曜日 午後1時57分 ...
Страница 35: ...GB_BS_02_L 0000006407 BOOK 2 ページ 2021年10月12日 火曜日 午後4時22分 ...
Страница 69: ...GB_BS_03_L 0000006412 BOOK 2 ページ 2021年10月12日 火曜日 午後4時33分 ...
Страница 97: ...GB_BS_04_L 0000006414 BOOK 2 ページ 2021年10月12日 火曜日 午後4時43分 ...
Страница 131: ...GB_BS_05_M 0000006450 BOOK 2 ページ 2021年10月26日 火曜日 午後7時2分 ...
Страница 165: ...GB_BS_06_F2 0000006532 BOOK 2 ページ 2021年10月8日 金曜日 午前11時51分 ...
Страница 173: ...GB_BS_07_M 0000006452 BOOK 4 ページ 2021年10月27日 水曜日 午前9時38分 ...
Страница 267: ...GB_BS_08_L 0000006416 BOOK 4 ページ 2021年10月26日 火曜日 午後5時30分 ...
Страница 451: ...GB_BS_09_F 0000006418 BOOK 2 ページ 2021年10月13日 水曜日 午前10時38分 ...
Страница 469: ...GB_BS_10_M 0000006456 BOOK 2 ページ 2021年10月26日 火曜日 午後7時49分 ...
Страница 502: ......