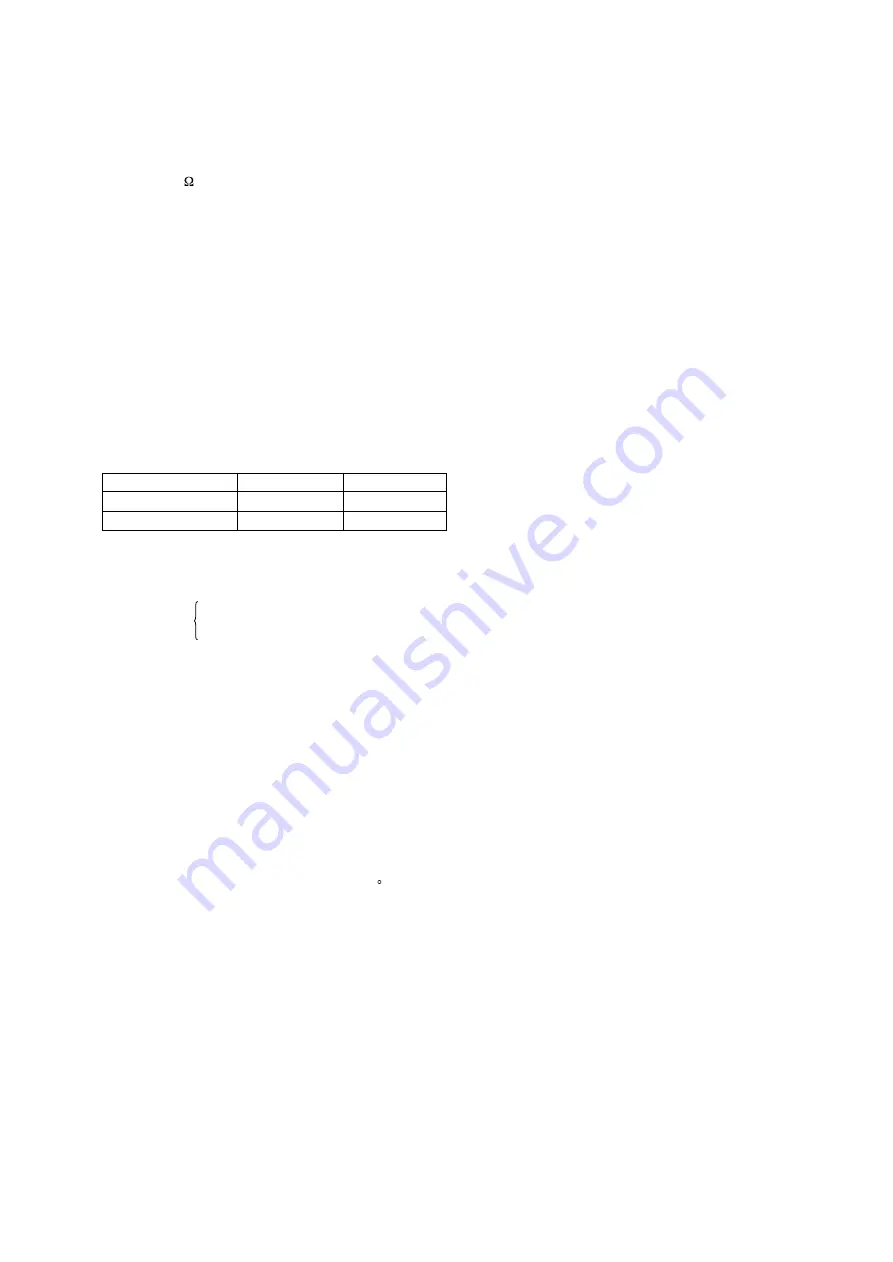
-140-
Constant Capacity Unit
Observe the following notes when changing the compressor
1) Make sure the main power supply is turned off.
If the reason for the compressor replacement is faulty insulation resistance, if the insulation resistance (Mega-
check) is 1 M or greater, it is possible that it has dropped due to the dormancy of the refrigerant to the compres-
sor, so after turning on the power for 12 hours with a belt heater heating, turn off the power and check the insulation
resistance again.
2) Remove the fin guard, front panel, and front panel of the divider panel.
3) Drain out the refrigerant from the high pressure and low pressure check joints.
4) Remove the compressor terminal cover, then disconnect the power cable.
5) Disconnect the discharge temperature sensor.
6) Disconnect the crankcase heater.
7) Heat up the soldered portions of the discharge piping, suction piping, and process piping and disconnect the piping.
8) Remove the compressor mounting nuts, then remove the compressor.
Caution: When removing the compressor, be careful not to let oil from inside the compressor overflow from the
suction piping and process piping.
9) Replace the compressor (service parts).
Caution: Do not use a compressor for another model.
The refrigerator oil is different for each model, so be sure to check!
10) Braze the discharge piping, suction piping, volume control valve piping and process piping.
11) Shut the ball valves (liquid, gas, and oil balance pipe) on the outdoor unit and apply nitrogen from the high and low
pressure service check joint, up to a pressure of A, checking to make sure there is no leakage.
12) Discharge the nitrogen gas.
13) Open the ball valves (liquid, gas, and oil balance pipe) on the outdoor unit and apply a vacuum.
14) Install the crankcase heater
15) Mount the discharge temperature sensor and attach the insulating cover.
16) Connect the power cable to the compressor’s terminals.
Caution: Be careful not to misalign the three phases. If the wires are connected wrong, it could damage the
compressor.
17) When applying the vacuum is completed, charge the unit with the amount of refrigerant it is charged with at the
factory, and with the supplementary amount it is charged with upon installation.
18) After reconfirming the phase of the power cable wires at the compressors’ terminals, carry out an insulation
the crankcase heater.
Caution: When the ambient temperature is 5 C or lower, if you do not spend 4 hours with the power on to the
heater, the unit will not function even when the remote controller is operated.
19) Make sure the ball valves of liquid, gas, and oil balance pipe are opened.
20) Run all the indoor units and make sure they are operating normally.
2.94 MPa ------- PUHN-YEM(K,C)-A
2.98 MPa ------- PUHN-P-YEM-A
❇
A =
Type 200
Type250
PUHN-YEM(K,C)-A
ZH133YDA
ZH165YDA
PUHN-P-YEM-A
ZEC133YAA
ZEC165YAA
resistance check, then install the terminal cover and turn on the main power supply, checking if current is flowing to
Содержание 500YEMK-A
Страница 15: ... 12 FANCON board G A board CNFAN CNFC2 CNPOW CNE CNDC1 CN15V1 CNDR1 CNIPM1 ...
Страница 16: ... 13 Y C board SNB board ...
Страница 17: ... 14 RELAY board CNRT2 CNCH CN52C2 CN52F CN51C2 CNOUT2 ...
Страница 19: ... 16 CONT board CNTR SWU2 SWU1 SW3 SW2 CNS1 M NET transmission CNFC1 CN20 Power supply 1 N 3 L1 ...
Страница 20: ... 17 FANCON board CNW CNV CNU CNFC2 ...
Страница 207: ... 204 ...