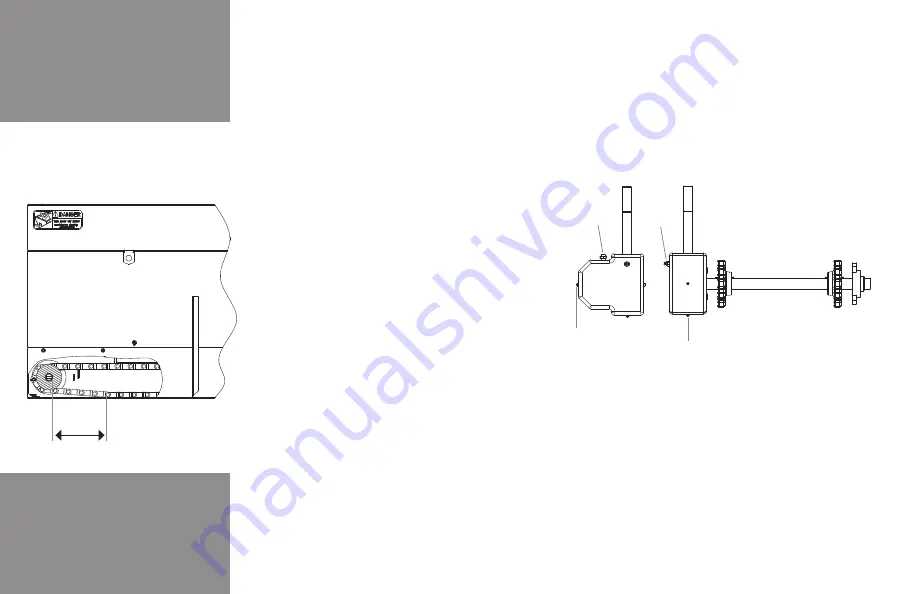
60
61
Maintenance
Inspection:
Before and after each use, spreader should be
inspected for loose, missing, or damaged mounting hardware,
parts, or safety guards. Spreader should also be inspected to
ensure it is securely attached to vehicle.
Cleaning:
Empty all material from spreader after each snow
or ice event. Wash entire spreader with soap and warm water
paying special attention to the conveyor drag chain. Do not
clean spreader with any corrosive chemicals or products that
contain chlorides or ammonium. Any commercially available
salt neutralizer may be applied.
Adjusting Drag Chain Tension:
Loosen rear jam nut on
take-up bolt and tighten take-up bolt until drag chain is
properly tensioned. Drag chain is properly tensioned when
the distance between the centerline of the front idler and
point where chain contacts flange of longitudinal is between
( . . cm). oth sides of drag chain must be
adjusted evenly.
Adjusting V-belt/ Roller Chain Tension:
Loosen the gasoline
engine or electric motor mounting bolts and slide motor away
from gearbo (towards passenger side of vehicle) until proper
tension is achieved. Tighten motor mounting bolts to hold motor
in position. V-belt or roller chain should have between 1/4"– 5/16"
(. cm . cm) de ection midway between the sprockets.
Adjusting Spinner Roller Chain:
Loosen four spinner shaft
or spinner drive shaft ( olyhawk models only) mounting bolts
and slide shaft away from gearbo (towards passenger side
of
vehicle) until proper tension is achieved and shaft is straight
up and down, then tighten shaft mounting bolts to hold shaft
in position. Roller chain should have between 1/4" – 5/16"
deflection midway between sprockets. To prevent roller chain
failure, both sprockets must be realigned. For olyhawk
models spinner shaft may need to be aligned with the spinner
drive shaft after adjusting roller chain tension.
Gearbox Oil Level:
Check the gearbo oil level every
hours of operation or monthly. Gearbox should be filled until
oil reaches oil level plug. Oil should be flushed prior to start of
season and replaced with an W
gear type lubricant.
Electrical System:
Electrical system should be inspected for
loose connections and corrosion every hours of operation
or weekly. Dielectric grease should be applied to all electrical
connections.
General Maintenance
Gearbox Maintenance
Breather
Grease
Zerk
Drain Plug
Oil Level Plug
Drag Chain Tension
Adjustment
8.0"– 20.0"
(20.3cm – 50.8cm)
Maintenance
Gearbox
Input Shaft
Bearing
Bearings
Bearings
Lubrication
Transmitter Battery
Replacement
Lubrication:
After every hours of operation or weekly,
lubricate drag chain and roller chains with any commercial chain
lubricant or a mi ture of
motor oil
diesel fuel. After
every hours of operation or weekly, lubricate drive shaft,
spinner drive shaft and spinner shaft bearings with high quality
chassis grease. After every hours of operation or monthly,
lubricate gearbox input shaft bearing with high quality chassis
grease.
CAUTION:
over greasing gearbox input shaft bearing
will result in damage to the gearbox input shaft seal.
Wireless Remote Transmitter Battery Replacement:
Wireless controller transmitter battery should be replaced before
the start of each season. It is also recommended to keep a spare
battery with the vehicle. Wireless transmitter requires a standard
CR
lithium button cell battery.
1.
Gently press and slide off the battery cover from the
wireless transmitter.
2.
Remove the battery by sliding it out from underneath the
retainer. Do not attempt to remove the battery by lifting it
up from the retainer.
3.
Install new battery by sliding it under the retainer. Battery
must be installed with the positive ( ) symbol visible.
Electric Clutch:
The electric clutch on new spreaders and re-
placement clutches should be burnished before use to achieve
maximum torque. The clutch burnishing procedure is as follows:
1.
Idle Engine
2.
ngage clutch for seconds
3.
Disengage clutch for seconds
4.
Repeat steps ,
times to achieve ma imum
clutch torque.
At the end of the winter season remove the electric clutch, add a
coat of light oil to each mating half and store indoors to prevent
corrosion. Prior to start of next season, oil should be removed
and clutch should be reassembled onto spreader.
Gasoline Engine:
Follow engine manufacturer s maintenance
recommendations.
Содержание LPV 3
Страница 14: ...14 1 2 3 4 5 6 7 8 9 10 11 12 13 14 15 LPV Component Identification GASOLINE ENGINE...
Страница 16: ...16 ELECTRIC LPV Component Identification 1 2 3 4 5 6 7 8 9 10 11 12 13 14 15...
Страница 18: ...18 PV Spreader Component Identification 1 2 3 4 5 6 7 8 9 10 11 12 13 14 15 16 17 18 GASOLINE ENGINE...
Страница 20: ...20 PV Spreader Component Identification ELECTRIC 1 2 3 4 5 6 7 8 9 10 11 12 13 14 15 16 17 18...
Страница 22: ...22 PV Spreader Component Identification HYDRAULIC 1 2 3 4 5 6 7 8 9 10 11 12 13 14 15 16 17 18 19...
Страница 24: ...24 GAS ENGINE Polyhawk Component Identification 1 2 3 4 5 6 8 9 10 11 12 13 14 15 16 17 18 19 7...
Страница 26: ...26 ELECTRIC Polyhawk Component Identification 1 2 3 4 5 6 8 9 10 11 12 7 13 14 15 16 17 18 19...
Страница 28: ...28 1 2 3 4 5 6 8 9 10 11 12 HYDRAULIC Polyhawk Component Identification 7 13 14 15 16 17 18 19 20...
Страница 53: ...53 Operating Instructions Left Right Pattern Left Spread Pattern Right Spread Pattern WindRow Spread Pattern...
Страница 71: ...71 Notes...
Страница 72: ...72...