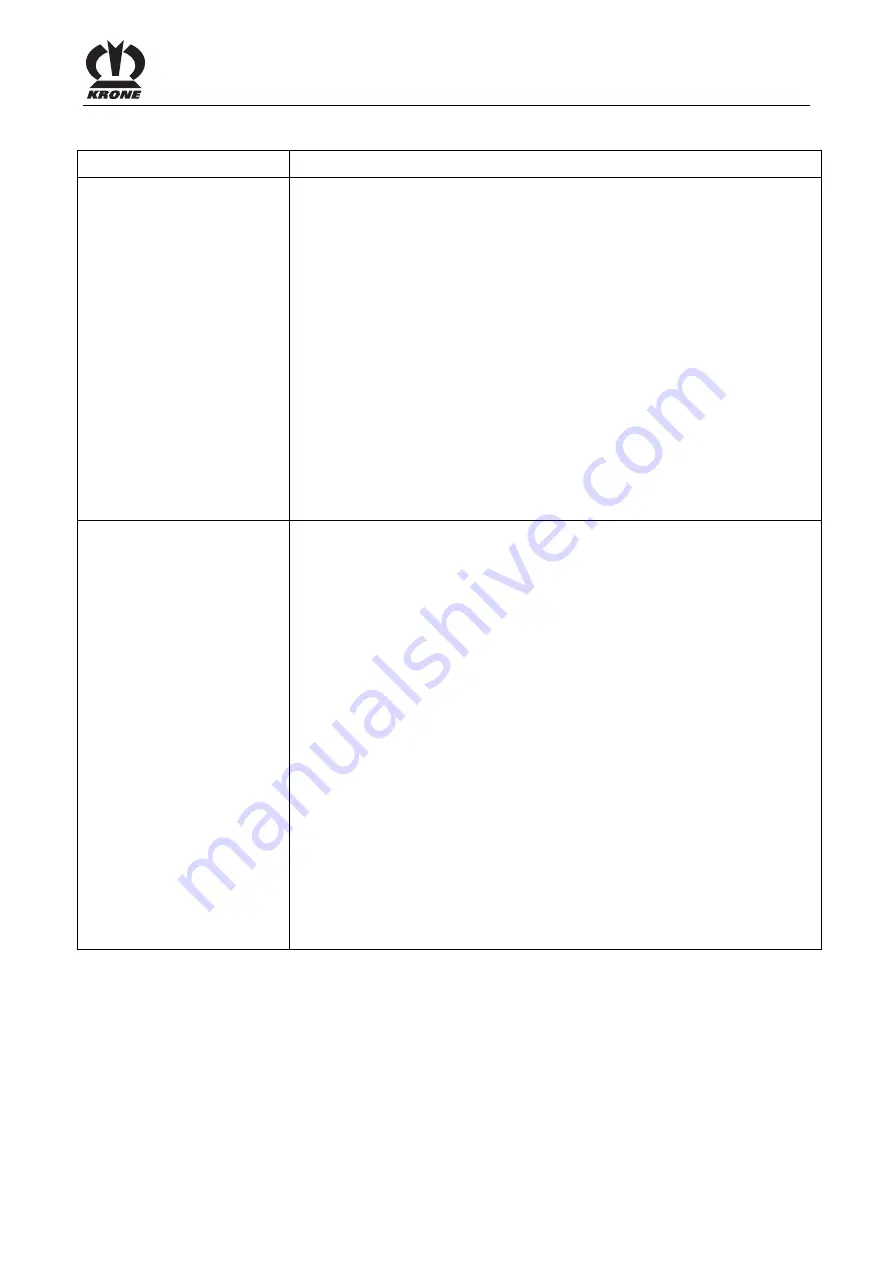
Malfunctions - Causes and Remedies
301
Pos: 40.36 /Überschriften/Überschriften 2/F-J/Fehlersuche in der Zentralschmierung @ 25\mod_1242052030604_78.docx @ 249788 @ 22 @ 1
16.4
Troubleshooting in the central lubrication
Pos: 40.37 /BA/Störungen - Ursachen und Behebung/Großpackenpressen/Störungen-Ursachen-Behebung Zentralschmierung T1 @ 25\mod_1242051129385_78.docx @ 249717 @ 2 @ 1
Malfunction
Cause and/or remedy
Blockage in the system or
in any bearing connected
to it.
Manually activated systems.
The hand lever cannot be
moved or is hard to move.
Find out what is causing the blockage and eliminate the cause.
PROCEDURE
First check whether the conveyor pump is working and is supplying lubricant
to the main distributor. To do this, loosen the pump outlet and activate the
pump. When the pump is working properly, connect the pump outlet again.
(Conclusion: there is no problem with the pump).
Let the pump work until the next blockage or until the next time the pressure
rises inadmissibly. Leave the pressure level as is.
One after the other, loosen the threaded input connections on the
subdistributors or on the main distributor, and for single-level systems the
threaded input connections. The distributor from which lubricant suddenly
leaks when the threaded input connection is loosened under pressure will
lead to the source of the fault.
The threaded input connections have to be screwed tight again. The
corresponding threaded bearing input connections should be loosened one
after the other. The bearing from which lubricant suddenly leaks when its
threaded input connection is loosened under pressure is the blocked bearing.
Eliminate the blockage on the bearing.
Blockage in the distributor
After you have loosened all
outlets of the main distributor
and/or the subdistributors, no
lubricant leaks from the
outlets. The distributor is
blocked.
Replace the blocked distributor.
If necessary, the distributor can be cleaned if the following conditions are
met.
The workplace must be clean. Remove all tube end screwed pieces. Remove
the plunger lock screws with a strong screwdriver. If necessary loosen them
by tapping with a hammer. Drive out the plungers with a soft mandrel (with a
diameter of less than 6 mm, if possible made of plastic).
Very important:
You must keep a record of which plunger belongs in which drill hole, since
the plungers must not be interchanged. Thoroughly rinse the distributor body
several times in grease-dissolving agent and blow it out with compressed air.
There are diagonal channels with a diameter of 1.5 mm on the ends of the
threading. You can press through them with a wire or pin. Rinse and blow out
the distributor several times. There could be hardened grease in the plunger
lock screws. This must be removed. Assemble the distributor. All the copper
discs must be replaced.
Before screwing in the tube outlet threaded pieces, you should pump out the
distributor with a hand pump or similar tool, if possible pumping oil through it
several times. The counter pressure in the distributor should not be any
greater than 25 bar as you do this. Any higher counter pressure means that
the distributor is not clean or than the plunger drill hole is damaged. If the
operating pressure of the distributor does not sink below 25 bar / 362,5 PSI in
spite of all your efforts, the distributor should be replaced.
Pos: 41 /BA/---------------Seitenumbruch---------------- @ 0\mod_1196175311226_0.docx @ 4165 @ 1 @ 1
Содержание Big Pack 4x4
Страница 331: ......