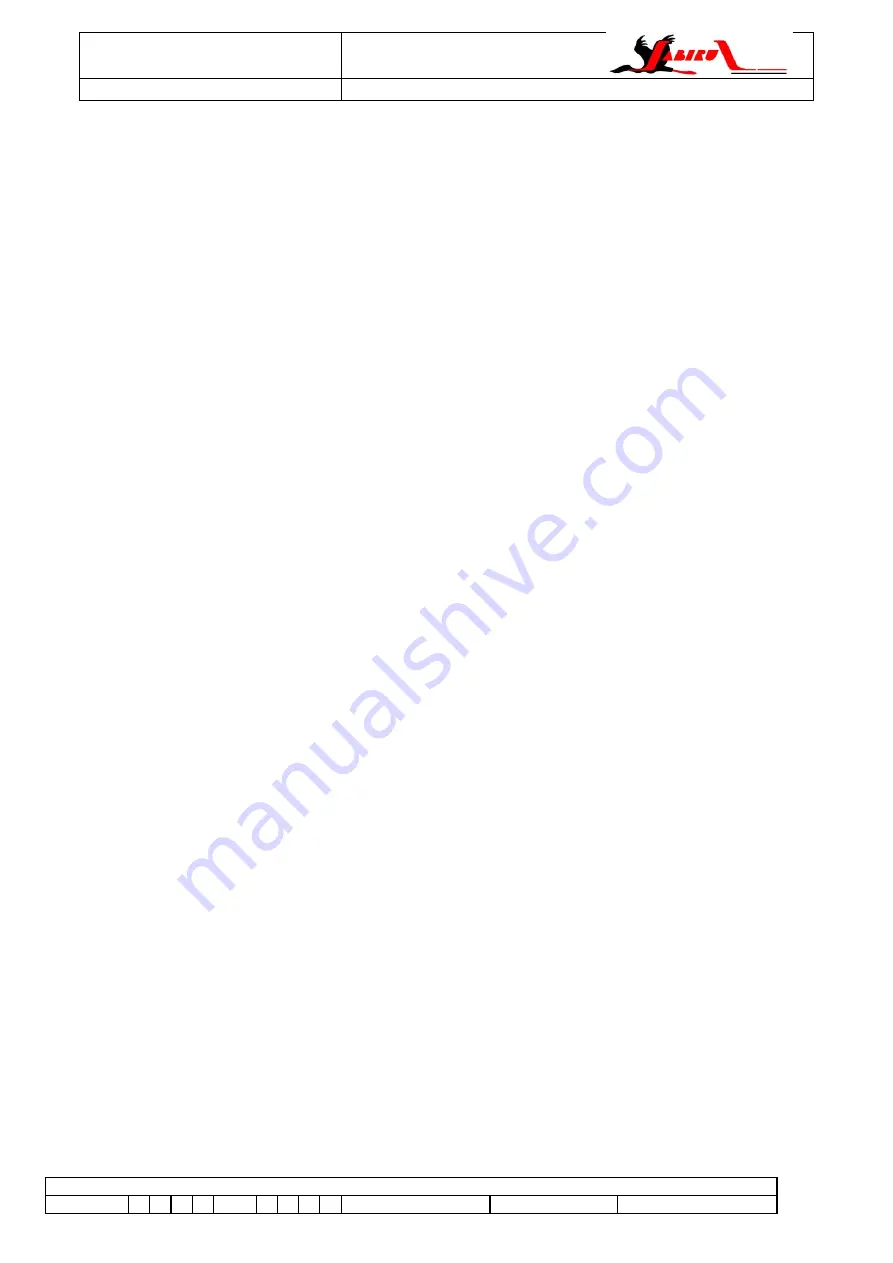
Engine Overhaul Manual
Jabiru Aircraft
Pty Ltd
Jabiru 2200 & 3300 Aircraft Engines
This document is controlled while it remains on the Jabiru server. Once this no longer applies the document becomes uncontrolled.
ISSUE
1
2
3
4
5
6 7
Dated : 28/10/2014
Issued By: AS
Page: 151 of 201
L:\files\Manuals_For_Products\Engine_Manuals\Overhaul_Manual\JEM0001-7_Overhaul_Manual_DRAFT_(29_10_14).docx
sure the tap engages properly with the thread and does not damage it. Prop flange retaining screw
holes are
3/8” UNF while the rear flywheel retaining screw holes are 5/16” UNF or 3/8” UNF. After
removing the tap use compressed air to blow out any debris from inside the holes.
Dry fit the cap screws to the propeller flange and verify that there is sufficient thread engagement into
the crankshaft
– a minimum 9mm (0.0.354”) of full thread engagement is required – which generally
equates to a total of around 11-12mm (0.433-
0.472”) measured from the tip of the screw to the flange
mating face. If a Belleville (cone or spring washer) is used, the compressed thickness of the washer
must be accounted for
– the numbers given here assume a std Jabiru Belleville washer is fitted (and
compressed) while measuring. While this is not normally an issue when using a Jabiru propeller flange,
manufacturing tolerances mean that this must still be checked. If using a non-Jabiru flange then this
dry fit stage is of critical importance to ensure that the flange is fitting properly (not binding on the crank,
is sitting co-axial with t
he crank etc). If replacement hardware is used ensure that it is “Unbrako 1960”
grade or equivalent.
Clean the threads of the screws using Loctite 7471 cure accelerator & allow to air dry. After priming,
ensure the threads stay clean
– contamination with oil (even skin oils from fingers) can reduce the
strength of the bond of the retaining compound.
Clean the threads in the crankshaft using Loctite 7471 cure accelerator & air dry.
Ensure that there is no paint, Loctite or other contaminants on the internal face of the propeller flange
where the mounting screws and washers seat.
Because the retaining compound sets quickly it is recommended to pre-heat the propeller flange to
around 60
– 80°C using a heat gun or similar. At this temperature the flange expands and will fit over
the dowel pins more easily.
Fit the flange to the crankshaft; this can be done most quickly by carefully positioning the pre-heated
flange in place with the dowels lined up with the holes in the flange. Then, using a piece of timber as a
“soft” driver fitting inside the flange, drive the flange into position with a hammer.
Alternative method for flange installation:
-
After initial cleaning of the threads of the crankshaft and of the cap screws fit the flange to the
crankshaft using 3 of the screws, tightening evenly to ensure flange is pulled correctly into position.
-
Do Not Apply Loctite! Tighten to the torque specified in Table 9.
-
Visually inspect the flange and ensure it is correctly fitted: ensure there is no gap between the
flange and the crank and that the flange is sitting straight.
-
Remove screws; the flange will remain in place on the dowel pins.
-
Repeat the steps given above for final cleaning and application of Loctite.
WARNING
It is vitally important that the screws are removed, male and female threads are cleaned and the
screws re-installed with Loctite: failure to apply retaining compound can result in engine failure.
Once the flange is in place and both male and female threads are clean apply a small amount
–
approximately the size of a large match head
– of Loctite 620 retaining compound to the flange screws.
Roll the threads of two screws together to spread the compound evenly over the threads of both,
ensuring that the same amount adheres to both and is evenly spread.
Apply the same amount (approximately the size of a large match head) of Loctite 620 to the threads in
the crankshaft. Apply the compound as shown in Figure 195: Use a scribe or small probe to apply the
Loctite to the threads inside the crankshaft. Apply in the range 1
– 6mm from the front face of the
crank.