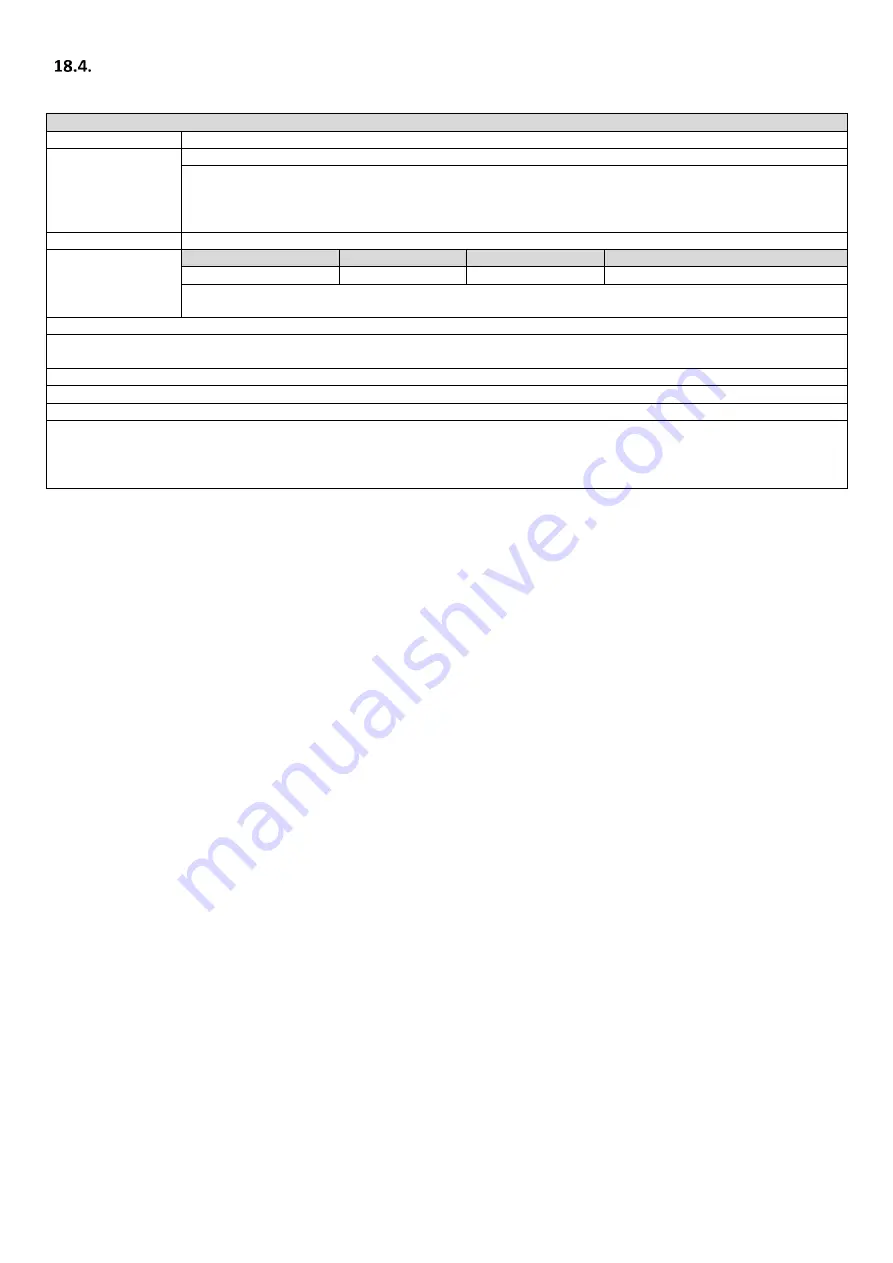
68
Optidrive P2 Elevator User Guide V2.30
Technical Data
www.InvertekDrives.com
Additional Information for UL Approved Installations
Optidrive P2 is designed to meet the UL requirements. In order to ensure full compliance, the following must be fully observed.
Input Power Supply Requirements
Supply Voltage
380 – 480 Volts for 400 Volt rated units, + / - 10% variation allowed, Maximum 500 Volts RMS
Imbalance
Maximum 3% voltage variation between phase – phase voltages allowed
All Optidrive P2 Elevator drives have phase imbalance monitoring. A phase imbalance of > 3% will result in the drive
tripping. For input supplies which have supply imbalance greater than 3% (typically the Indian sub- continent & parts
of Asia Pacific including China) Invertek Drives recommends the installation of input line reactors. Alternatively, the
drives can be operated as a single phase supply drive with 50% derating.
Frequency
50 – 60Hz + / - 5% Variation
Short Circuit Capacity
Voltage Rating
Min kW (HP)
Max kW (HP)
Maximum supply short-circuit current
230V/400V
0.75 (1)
37 (50)
100kA rms (AC)
All the drives in the above table are suitable for use on a circuit capable of delivering not more than the above
specified maximum short-circuit Amperes symmetrical with the specified maximum supply voltage.
Incoming power supply connection must be according to section 6.3.1
All Optidrive P2 Elevator drives are intended for indoor installation within controlled environments which meet the condition limits shown in
section 18.1
Branch circuit protection must be installed according to the relevant national codes. Fuse ratings and types are shown in section 18.3
Suitable Power and motor cables should be selected according to the data shown in section 18.3
Power cable connections and tightening torques are shown in section 5 and 6.
Optidrive P2 Elevator drives provide motor overload protection in accordance with the National Electrical Code (US).
Where a motor thermistor is not fitted, or not utilised, Thermal Overload Memory Retention must be enabled by setting P4-12 = 1
Where a motor thermistor is fitted and connected to the drive, connection must be carried out according to the information shown
in section 6.6.2