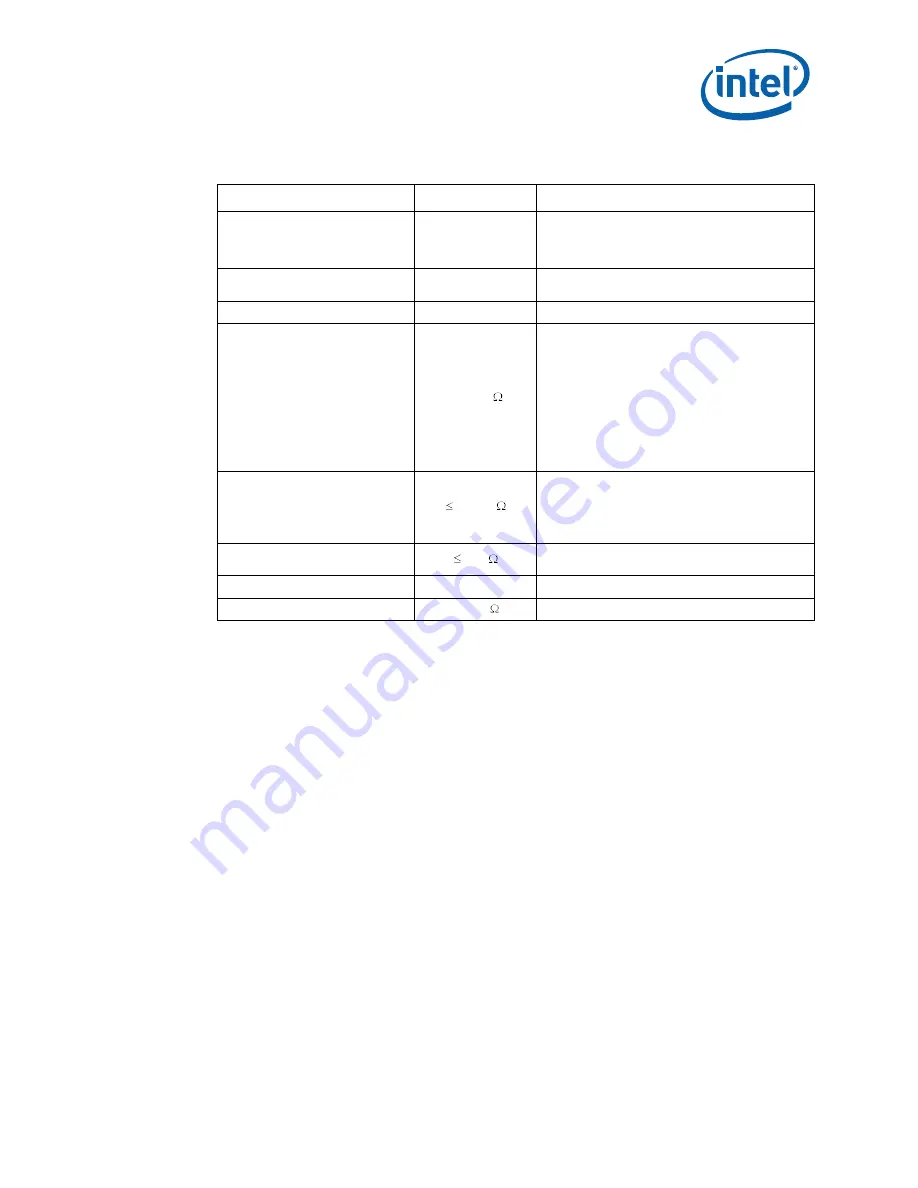
Thermal/Mechanical Design Guide
29
LGA1366 Socket and ILM Electrical, Mechanical, and Environmental Specifications
4.6
Environmental Requirements
Design, including materials, shall be consistent with the manufacture of units that meet
the following environmental reference points.
The reliability targets in this chapter are based on the expected field use environment
for these products. The test sequence for new sockets will be developed using the
knowledge-based reliability evaluation methodology, which is acceleration factor
dependent. A simplified process flow of this methodology can be seen in
Figure 4-1
.
Table 4-4.
Electrical Requirements for LGA1366 Socket
Parameter
Value
Comment
Mated loop inductance, Loop
<3.9nH
The inductance calculated for two contacts,
considering one forward conductor and one return
conductor. These values must be satisfied at the
worst-case height of the socket.
Mated partial mutual inductance, L
NA
The inductance on a contact due to any single
neighboring contact.
Maximum mutual capacitance, C.
<1 pF
The capacitance between two contacts
Socket Average Contact Resistance
(EOL)
15.2 m
The socket average contact resistance target is
derived from average of every chain contact
resistance for each part used in testing, with a
chain contact resistance defined as the resistance
of each chain minus resistance of shorting bars
divided by number of lands in the daisy chain.
The specification listed is at room temperature
and has to be satisfied at all time.
Socket Contact Resistance: The resistance of
the socket contact, solderball, and interface
resistance to the interposer land.
Max Individual Contact Resistance
(EOL)
100 m
The specification listed is at room temperature
and has to be satisfied at all time.
Socket Contact Resistance: The resistance of
the socket contact, solderball, and interface
resistance to the interposer land; gaps included.
Bulk Resistance Increase
3 m
The bulk resistance increase per contact from
24 °C to 107 °C
Dielectric Withstand Voltage
360 Volts RMS
Insulation Resistance
800 M
Содержание X5550 - Quad Core Xeon
Страница 8: ...8 Thermal Mechanical Design Guide ...
Страница 12: ...Introduction 12 Thermal Mechanical Design Guide ...
Страница 24: ...Independent Loading Mechanism ILM 24 Thermal Mechanical Design Guide Figure 3 3 ILM Assembly ...
Страница 26: ...Independent Loading Mechanism ILM 26 Thermal Mechanical Design Guide ...
Страница 48: ...Component Suppliers 48 Thermal Mechanical Design Guide ...
Страница 50: ...Mechanical Drawings 50 Thermal Mechanical Design Guide Figure B 1 Board Keepin Keepout Zones Sheet 1 of 4 ...
Страница 51: ...Thermal Mechanical Design Guide 51 Mechanical Drawings Figure B 2 Board Keepin Keepout Zones Sheet 2 of 4 ...
Страница 52: ...Mechanical Drawings 52 Thermal Mechanical Design Guide Figure B 3 Board Keepin Keepout Zones Sheet 3 of 4 ...
Страница 53: ...Thermal Mechanical Design Guide 53 Mechanical Drawings Figure B 4 Board Keepin Keepout Zones Sheet 4 of 4 ...
Страница 54: ...Mechanical Drawings 54 Thermal Mechanical Design Guide Figure B 5 1U Reference Heatsink Assembly Sheet 1 of 2 ...
Страница 55: ...Thermal Mechanical Design Guide 55 Mechanical Drawings Figure B 6 1U Reference Heatsink Assembly Sheet 2 of 2 ...
Страница 58: ...Mechanical Drawings 58 Thermal Mechanical Design Guide Figure B 9 Heatsink Shoulder Screw 1U 2U and Tower ...
Страница 59: ...Thermal Mechanical Design Guide 59 Mechanical Drawings Figure B 10 Heatsink Compression Spring 1U 2U and Tower ...
Страница 60: ...Mechanical Drawings 60 Thermal Mechanical Design Guide Figure B 11 Heatsink Retaining Ring 1U 2U and Tower ...
Страница 61: ...Thermal Mechanical Design Guide 61 Mechanical Drawings Figure B 12 Heatsink Load Cup 1U 2U and Tower ...
Страница 82: ...Mechanical Drawings 82 Thermal Mechanical Design Guide ...
Страница 88: ...Socket Mechanical Drawings 88 Thermal Mechanical Design Guide ...
Страница 95: ...Thermal Mechanical Design Guide 95 Embedded Thermal Solutions Figure E 5 UP ATCA Heat Sink Drawing ...
Страница 102: ...Processor Installation Tool 102 Thermal Mechanical Design Guide Figure F 1 Processor Installation Tool ...