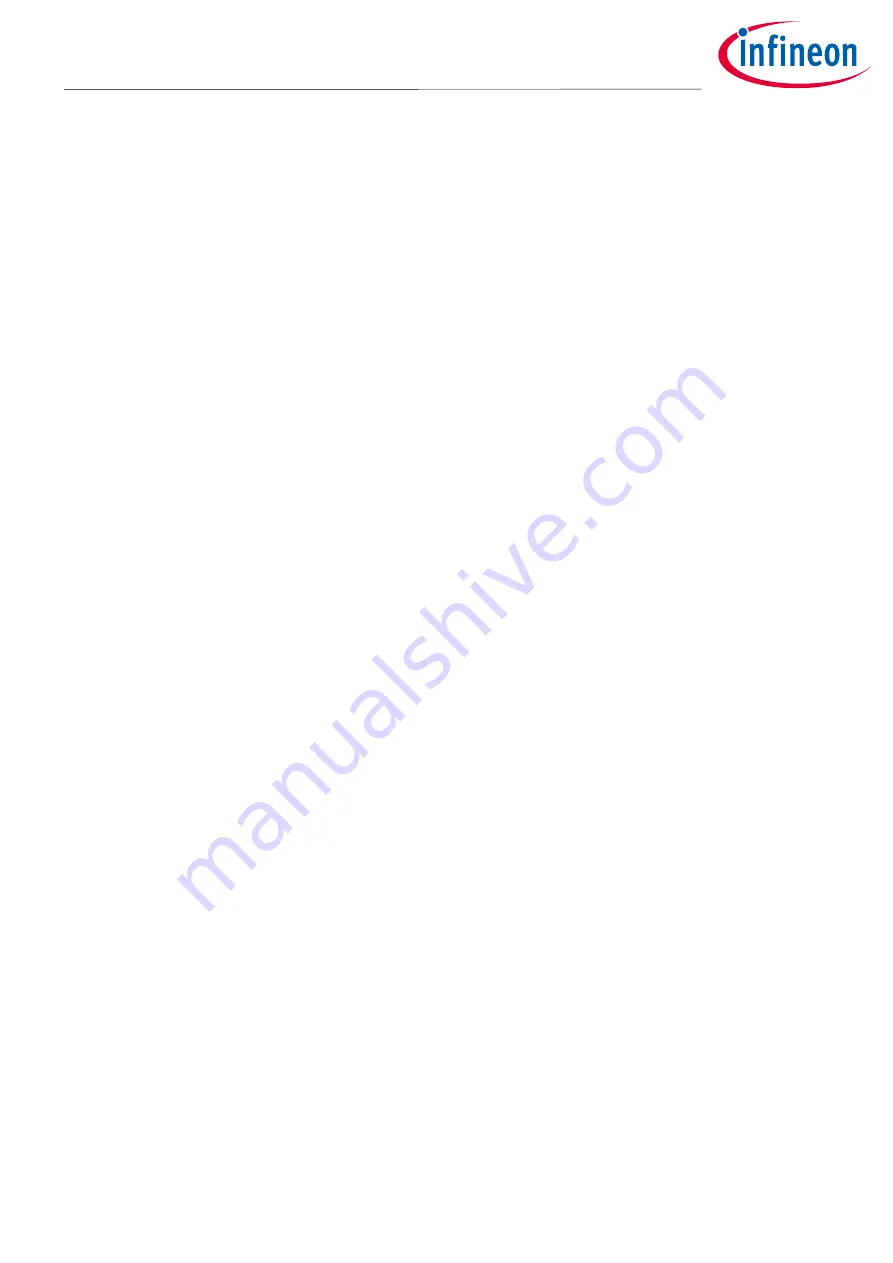
Additional information
16 of 31
Revision 4.0
2021-10-11
Recommendations for board assembly of Infineon transistor outline
type packages
Mounting of through-hole devices
4
Mounting of through-hole devices
The following factors have to be taken into account to achieve the best quality assembly for a given
application:
Insulating material (e.g. washers, spacers)
Screws
Thermal grease
Mounting torque
PCB and heat sink
Attachment holes for heat sink screw mounting
Soldering method, especially temperature profile
4.1
Pre-mounting processes and mounting materials
Through-hole packaged parts are mostly supplied with the leads projecting straight out of the mold body. Many
practical power circuits use bulky heat sinks in contact with the device tabs to enhance thermal performance.
This may preclude the straight-leaded orientation arrangement of the standard part. Consequently it is
common to change the lead length and direction to make a more convenient electrical connection on an
adjacent printed circuit board. This section is intended to address the frequently asked package related
question of how the leads of TO THD may be safely bent without endangering part reliability.
Lead cutting
The leads of THDs can be cut before mounting or after mounting and soldering. In case of cutting after
soldering, the leads are embedded in the solder joint. Severe mechanical mishandling during the cutting
process could cause solder joint failure, but generally does not harm the component body. When cutting prior
to mounting, the leads have to be fixed by a clamp that should be similar to a clamp used for lead bending as
outlined below.
Lead bending
In order to insert the terminals of THDs in the holes of the PCB, the terminals may have to be bent to match the
pitch of the respective PCB holes for various reasons.
The original straight alignment of the leads (gate, drain, source of a transistor package) may not provide an
adequate electrical clearance and creepage distance between the track pads. By offsetting the centre leg this
problem may be avoided.
For some mechanical arrangements the heat sink and the lead termination point may be subjected to relative
movement. In these cases where these forces are unavoidable, it is desirable to introduce a stress relieving lead
bend in order to reposition this stress. With a simple bend of this sort, the stresses which would normally have
degraded either the lead-to-body joint or the lead-to-PCB joint, will be absorbed along the lead length.