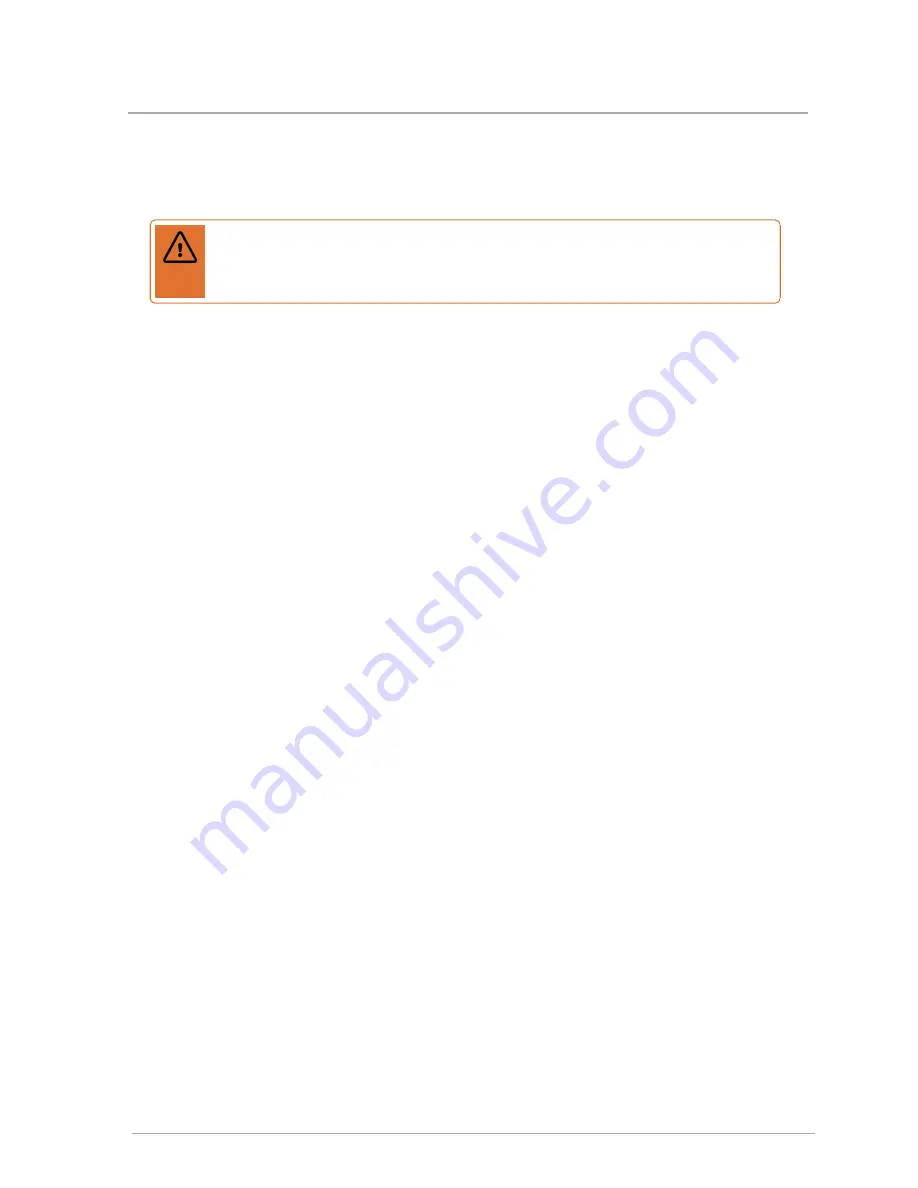
closed loop hydronic systems. In areas where water quality is in question, or when chemical
treatment or glycol is required, other options should be considered. Follow the applicable codes
and good piping practice.
Warning
Close the fill valve after any addition of water to the system, to reduce risk of water
escaping.
Today there are a number of boiler feed and pressurization devices on the market that may be a
better choice than a raw water fill from the mains. When regular maintenance requires relief
valve blow-off, the discharge may be directed back into the pressurization appliance for recycling
of boiler fluid and chemicals back into the system. In buildings that may be unoccupied for long
periods of time, pressurization appliances are useful to prevent flood damage should leakage
occur from any component in the system. An additional benefit is that backflow prevention
devices are not required when using these devices.
Do not place any water connections above the boiler to avoid damage to the fan and controls. If
needed, create a shield over the top of the cover, but allow clearance for airflow and service
access.
3.11.2.1 Primary-Secondary piping
For best results use a primary / secondary piping system, with a boiler loop piped in 1" or 1¼".
Primary / Secondary piping ensures adequate flow and de-couples Δ°T issues (boiler vs.
distribution). Aim for a 20°F to 30°F Δ°T across the heat exchanger at high fire (there is a boiler
protection throttle fence limiting the Δ°T to 40°F).
These boilers can supply three different heating loads within the temperature range of 34°F to
180°F to meet three separately-piped loads. Use closely spaced tees to connect each pumped
“load” (e.g. DHW, baseboards or radiant floor) to the primary loop. Alternatively, use a hydraulic
separator between the boiler loop and the system. As well, two load systems may also be piped
in parallel.
To ensure adequate water flow through the boiler under high-head / single-zone space heating
conditions, a pressure-activated bypass or other means of bypass must be used on any load
where the flow rate might drop below minimum requirements.
Ensure that the pump is rated for the design circulating water temperatures; some pumps have a
minimum water temperature rating above the low temperature potential of the boiler. Following
installation, confirm the actual performance by measuring Δ°T (under high and low flow
conditions).
Check valves or thermal traps should be used to isolate both the supply and return piping for
each load - to avoid thermal siphoning and reverse flow.
53
3.11.2 System piping
Содержание CX Series
Страница 6: ...Boiler part diagrams CX 150 CX 199 118 Installation Commissioning Report 122 6 Section Contents...
Страница 10: ...Intentionally left empty...
Страница 13: ...Figure 2 Top and bottom view CX 150 CX 199 dimensions Figure 3 Front and side view CX 199 13 CX 199 dimensions...
Страница 70: ...Intentionally left empty...
Страница 84: ...Intentionally left empty...
Страница 102: ...Intentionally left empty...
Страница 114: ...Appendices Wiring diagrams Figure 48 Controller electrical diagram 114 Section Troubleshooting...
Страница 115: ...Figure 49 Internal wiring diagram 115 Wiring diagrams...
Страница 116: ...Figure 50 Sequence of Operation 116 Section Troubleshooting...
Страница 117: ...8 4 Exploded views of the CX 150 CX 199 appliance 117 8 4 Exploded views of the CX 150 CX 199 appliance...
Страница 119: ...119 Boiler part diagrams CX 150 CX 199...