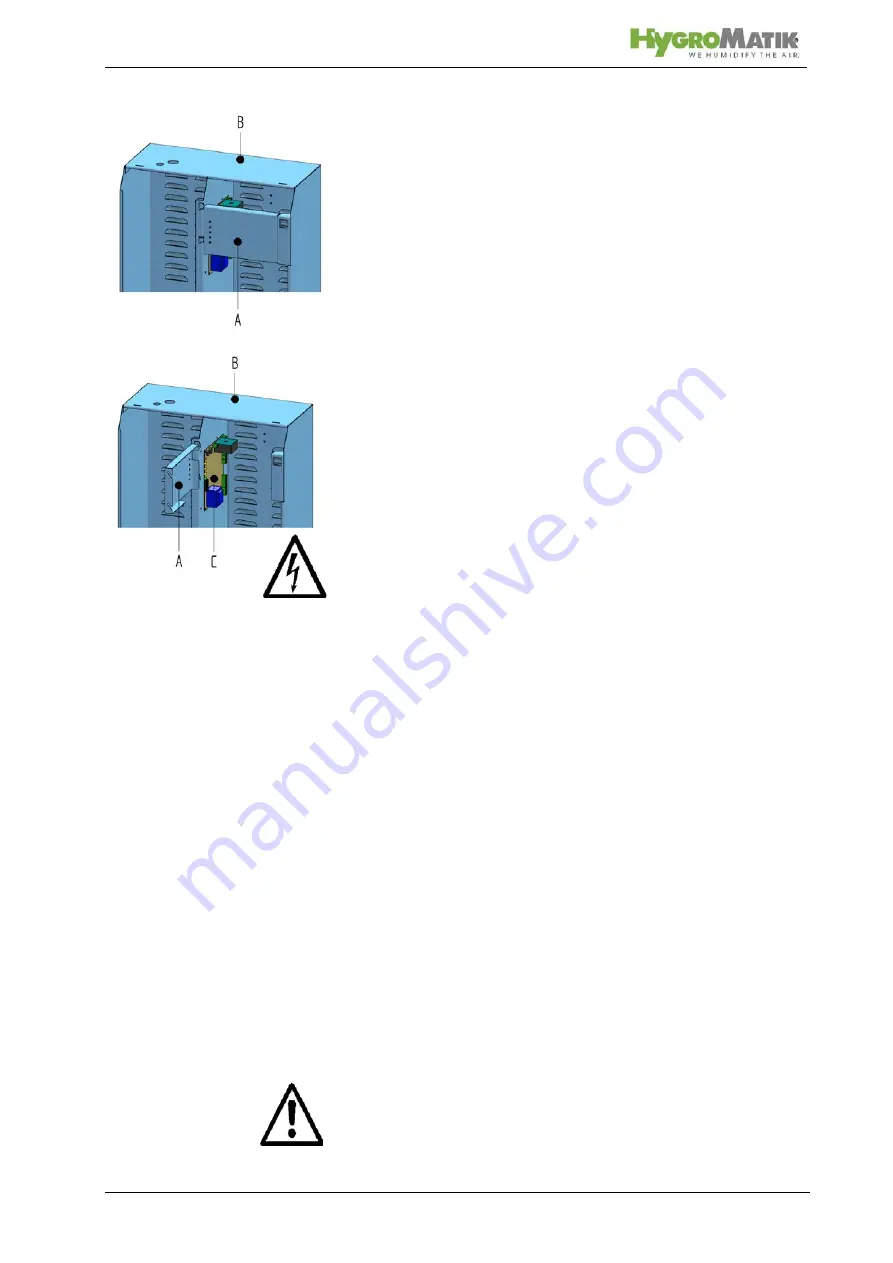
Page 49
9.3
Access to Control Unit
»
Remove cover (or electric compartment cover) and lift
display panel (A) out of its guide.
»
Turn display panel (see drawing) and hang display
panel on the humidifier cabinet (B) by placing the two
guide pins in the two front guides.
»
The PCB (C) is now accessible.
Danger, Hazardous Voltage:
Switch off unit before installing or
removing the display plate.
9.4
Cleaning the Coarse Strainer in the Cylin-
der Base
Removal
»
Shut off water supply.
»
Drain steam cylinder by setting main switch to Pos II.
»
Disconnect power supply and secure against restart
(set main switch to Pos 0, switch, remove main fuse
and control fuse F1).Verify the absence of electric cur-
rent.
»
Remove connector plug for steam cylinder lead.
»
Twist and remove star screw on the steam hose
adapter.
»
Remove clip on the steam hose adapter (2).
»
Push the steam hose adapter up out of the cabinet and
secure with the clip.
»
Undo clamping belt.
»
Lift steam cylinder (9) out of the base (11).
Warning: When lifting the cylinder be aware not to damage the
heating element cable.
Содержание HeaterLine HL 12
Страница 1: ...Electric Heater Steam Humidifier HL CSAK HL CSA IMPORTANT READ AND SAVE THESE INSTRUCTIONS Manual...
Страница 28: ...Page 28 Drill Pattern DN40 1 1 2 not to scale Note Due to variable print media the dimensions are not to scale...
Страница 67: ...Page 67 13 Exploded View...
Страница 68: ...Page 68 14 View of Cabinet...