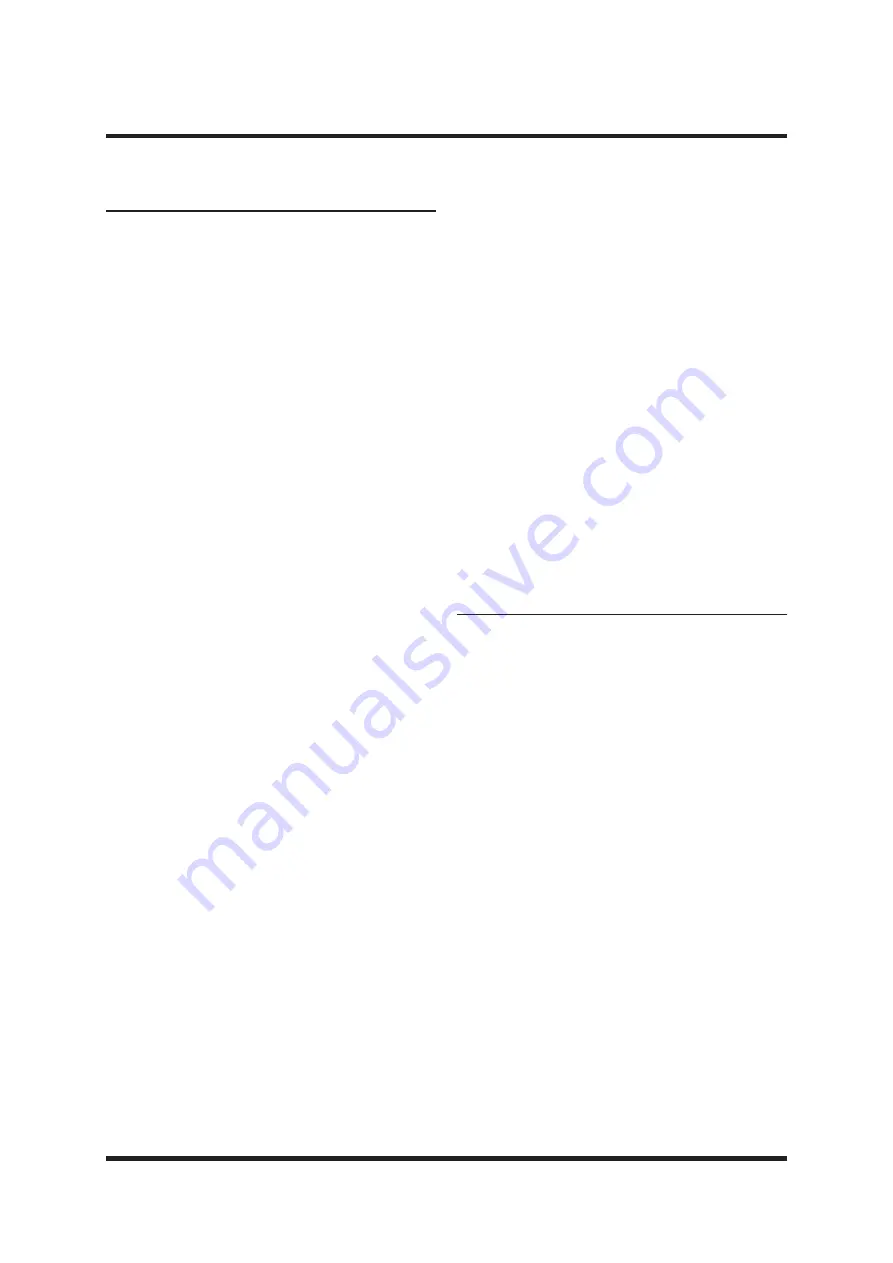
iii) Examine the auxiliary electrical device/alarm,
door closers etc��, have all operated correctly��
iv) Ensure actuator is reset before refitting, using the
reset tool provided��
d�� For master/slave system, remove the appropriate
port plug and reconnect the pilot actuation line to
the slave port on the back of the master valve��
e�� Reset pressure switches after the test has been
completed��
(1) An approved distributor is carrying out the
maintenance on the detection system��
(2) If the servicing of the detection system is being
carried out at the same time as the mechanical
service by another nominated body��
Specialised Maintenance Duties
Container Hydrostatic Pressure Testing
In countries where NFPA 2001 applies the following
criteria are used for hydrostatic pressure testing :
Containers only need hydrostatic pressure testing after
discharge�� Systems under local jurisdiction may have
other rules of hydrostatic pressure testing, please follow
these rules��
Finally
Carry out a final visual inspection of the system and
the protected area to ensure that all equipment has been
reinstalled and reconnected properly�� Ensure that any
associated control/indication panel is displaying normal
operation�� Complete the site log book, recording work
carried out and parts used�� Inform the responsible person
that the work is complete and that the system is back
on-line��
Mechanical Servicing Procedure
a�� Remove valve actuator(s) from the container
valve(s)��
b�� For master/slave system complete the following
steps to check the slave actuation system:-
1�� Disconnect pneumatic valve actuators from the
slave container valves��
2�� Disconnect the pilot loop from the master container
valve and install the appropriate plug��
3�� Introduce 4 bar (58 psi) pressure into the pilot
actuation line to the pneumatic actuators��
4�� Check that the pistons in the pneumatic valve
actuators have fully operated��
5�� Check for leaks�� There must be less than 10% loss in
pressure within 1 minute)��
6�� Vent pressure in the pilot actuation line and re-set all
of the actuators��
7�� Introduce 34 bar (493 psi) pressure into the pilot
actuation line to the pneumatic actuators��
8�� Check that the pistons in the pneumatic valve
actuators have fully operated��
9�� Check for leaks�� There must be less than 10% loss in
pressure within 1 minute)��
10�� Vent pressure in the pilot actuation line and re-set all
of the actuators��
c�� To check the electrical actuation system (for single
container systems only electrical actuators are
fitted):
i) Remove electrical actuators from valve
assembles��
ii) Activate the detection system in accordance with
procedures provided with the system�� When this
test is performed, the release circuit of the detection
system must operate the electric actuators causing
the plungers to be firmly extended��
77
© 2010 Macron Safety Systems (UK) Limited
SECTION 8 - MAINTENANCE
EQUIPMENT:
FM-200® (UL/FM)
PUBLICATION:
14A-07H
ISSUE No.
02
DATE:
2010-03
Содержание FM-200
Страница 100: ...100 APPENDIX C FM 200 DATA SHEET FM 200 Material Safety Data Sheet MSDS 5 PAGES FM 200 UL FM 14A 07H 02 2010 03...
Страница 102: ...3ULQW DWH 102 APPENDIX C FM 200 DATA SHEET FM 200 UL FM 14A 07H 02 2010 03...
Страница 104: ...3ULQW DWH 104 APPENDIX C FM 200 DATA SHEET FM 200 UL FM 14A 07H 02 2010 03...