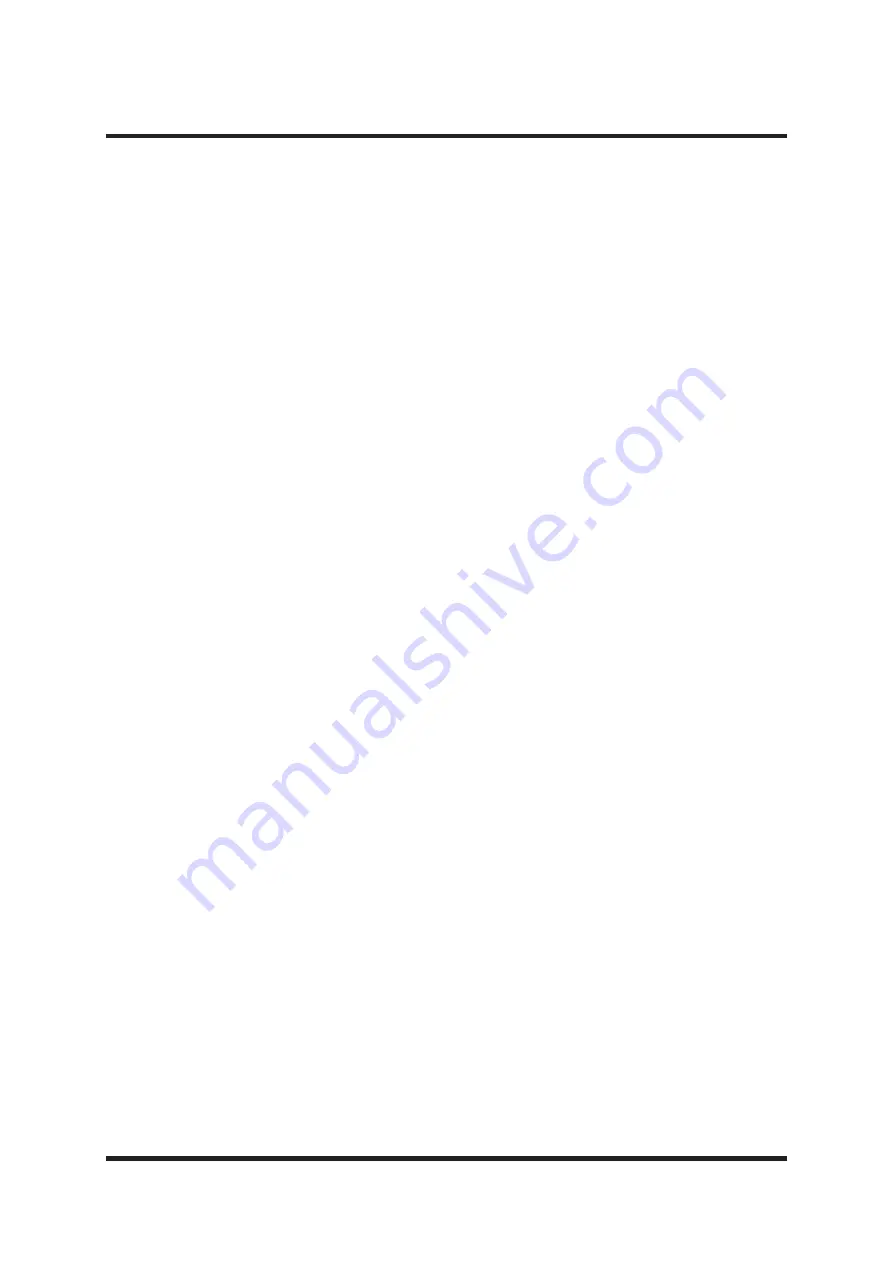
Pre-checks and Visual Inspections
General
When the installation is complete, and before making the
final connections, the following checks should be made:
Mechanical Checks
Inspect protected area closely for conformance to original
risk specifications and for enclosable openings or sources
of agent loss which may have been overlooked in the
original specification��
Building work should be thoroughly checked to
ensure that enclosures have been properly constructed
and that voids in floors and above suspended ceilings
have been sealed��
All back channels should be secured firmly to the
wall or bulk head��
Containers should be securely held within brackets��
Piping should be securely fixed within hangers��
All pipe connections must be tight��
Nozzles to be the proper type, correctly placed, and
properly orientated��
Check model and weight markings on container
nameplates to verify that correct containers and
charges have been installed as required��
Verify that all warning and instruction plates are
mounted where required��
Electrical Checks
The electrical systems may include interfaces with many
other systems for alarm, indication, actuation, shutdown,
etc�� For complex electrical systems the scope and operating
requirements will be described in other documents��
Electrical checks are given below for a basic system using
electrical actuation of the container valve;
Remove top mounted electrical actuator or side
mounted solenoid (which is connected via the
solenoid adaptor) from valve�� Check that solenoid is
activated when system is triggered�� If the solenoid
adaptor is not present, remove electrical connections
from side mounted solenoid and check wiring voltage
is correct for actuation when system is triggered��
•
•
•
•
•
•
•
•
•
During detection system actuation verify the following
functions operate;
All apertures in hazard enclosure are closed by
dampers or other suitable methods��
Electrical equipment in the protected area is tripped
and isolated��
Pneumatic Checks
The slave actuators on manifolded systems are fired by
agent discharge�� Pneumatic checks are detailed below;
Remove all pneumatic actuators from container
valves��
Disconnect pilot hose from the master container
valve adaptor (see Figure 62)��
Provide 4 bar (58 psi) pressure to the master
container valve pilot hose��
Verify all pneumatic actuator pistons are in the fired
position��
Check for leaks�� There must be less than 10% loss in
pressure within 1 minute)��
Provide 34 bar (493 psi) pressure to the master
container valve pilot hose��
Verify all pneumatic actuator pistons are in the fired
position��
Check for leaks�� There must be less than 10% loss in
pressure within 1 minute)��
Before replacing the pneumatic actuators, ensure that
all pistons are fully reset (see Figure 60)�� After reinstalling
the pneumatic actuators, reconnect the pilot hose to the
master container valve adaptor (see Figure 62)��
Final Connections
Discharge Piping
The final connection of the discharge piping occurs at the
container valve assembly�� For single container systems,
the valve anti-recoil cap can be removed and the discharge
pipe connected to the container outlet�� For multi-container
systems, the valve anti-recoil caps can be removed and all
discharge hoses fitted��
•
•
•
•
•
•
•
•
•
•
© 2010 Macron Safety Systems (UK) Limited
SECTION 5 - INSTALLATION
EQUIPMENT:
FM-200® (UL/FM)
PUBLICATION:
14A-07H
ISSUE No.
02
DATE:
2010-03
Содержание FM-200
Страница 100: ...100 APPENDIX C FM 200 DATA SHEET FM 200 Material Safety Data Sheet MSDS 5 PAGES FM 200 UL FM 14A 07H 02 2010 03...
Страница 102: ...3ULQW DWH 102 APPENDIX C FM 200 DATA SHEET FM 200 UL FM 14A 07H 02 2010 03...
Страница 104: ...3ULQW DWH 104 APPENDIX C FM 200 DATA SHEET FM 200 UL FM 14A 07H 02 2010 03...