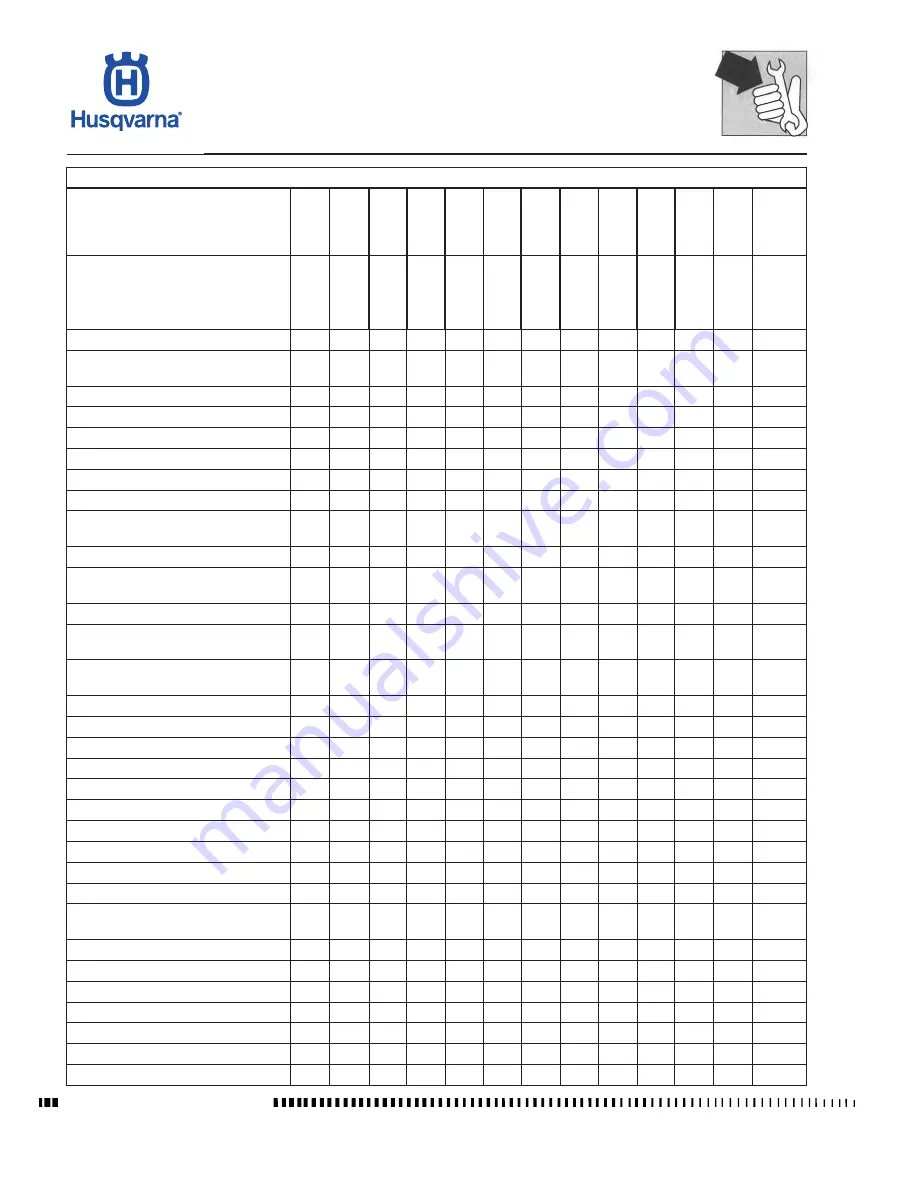
B.2
TE 250R - 310R 2013 I.E. / TE 310R 2013 I.E. USA
TC 250R 2013 - TC 250R 2013 I.E. USA
TXC 250R - 310R 2013 I.E. USA
MAINTENANCE
Workshop Manual Ed. 07-2012
SCHEDULED MAINTENANCE CHART (TO BE CARRIED OUT AT THE HUSQVARNA DEALER)
TXC - TE 250R / TXC - TE 310R
RACING MOTORCYCLE, FOR RAC
-
ING USE: FULL POWER RATING
AFTER THE
FIRST
2,5 h
EVER
Y
5 h
EVER
Y
10 h
EVER
Y
20 h
EVER
Y
30 h
EVER
Y
40 h
EVER
Y
50 h
EVER
Y 60 h
EVER
Y
70 h
EVER
Y 80 h
EVER
Y 90 h
EVER
Y
100 h
REPLACE
AS
REQUIRED
PARTICOLARE
CHECK
CHECK
SER
VICE
COUPON
SER
VICE
COUPON
SER
VICE
COUPON
SER
VICE
COUPON
SER
VICE
COUPON
SER
VICE
COUPON
SER
VICE
COUPON
SER
VICE
COUPON
SER
VICE
COUPON
SER
VICE
COUPON
AIR FILTER
P,L
P,L
REAR CHASSIS MNTG BOLTS, EN
-
GINE MNTG BOLTS
C
C
WHEEL SPOKE TENSION
C
C
SPROCKET BOLT TIGHTENING
C
C
TORQUE OF NUTS AND BOLTS
C
C
COOLANT
C
X,
*
BRAKE PADS
C
X
REAR CHAIN SPROCKET
C
X
HANDLEBAR MOUNTS AND FAS
-
TENERS
C
REAR SWINGING ARM BUSHING
L
REAR SUSPENSION LINKAGE BUSH
-
INGS
L
CHAIN GUIDE/CHAIN GUARD
C
X
SWINGING ARM AXLE ROLLER
CAGES
L
ROLLER CAGES, LINKAGE PINS OF
REAR SUSP.
L
COMPLETE THROTTLE CONTROL
C, L
EXHAUST PIPE AND SILENCER
C
X
FUEL PIPES
C
S
X
SECONDARY DRIVE CHAIN
C, L
C, L
X
KICK START PEDAL
L
GEAR SHIFT PEDAL
C
RADIATORS
C
WATER HOSES AND CLAMPS
C
RADIATORS TO WATER PUMP HOSE
C
FOOTPEGS, PINS, SPRINGS
C
X
STEERING HEAD, BOTTOM YOKE
WITH STEM
L
REAR CHAIN SLIDER
C
X
FRONT BRAKE DISC
C
X
REAR BRAKE DISC
C
X
CHAIN GUIDE ROLLER, BEARINGS
C
SIDESTAND
C
COMPLETE CLUTCH CONTROL
R
THROTTLE CABLES
C/L
X