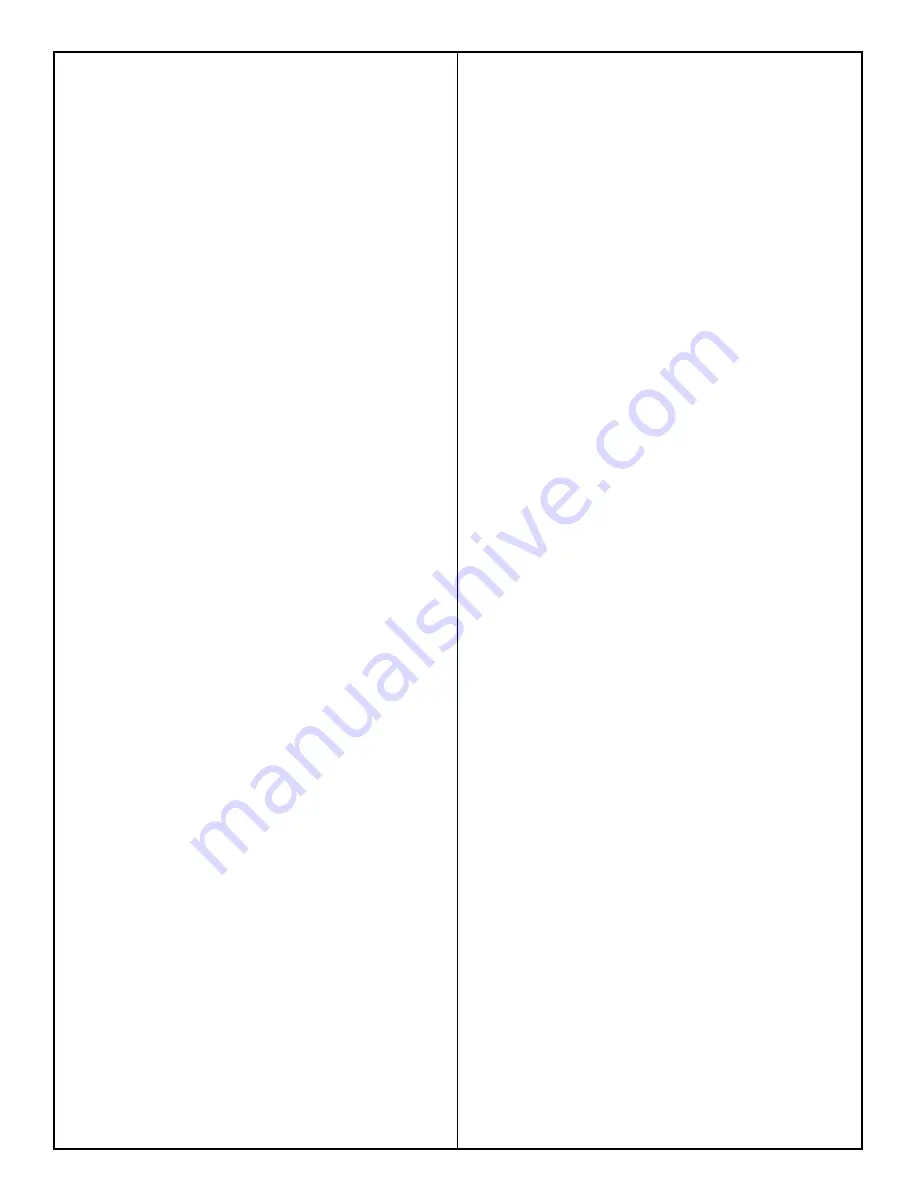
ALL SEASON AIR CONDITIONING SYSTEM
29
The seal bellows can be removed by forcing a
screw driver behind the brass stamped flange
at various points and prying it out of the
seal plate. Remove the neoprene "0" ring from
the seal plate. Discard seal bellows and "0"
ring.
Wash the seal plate and shaft with a clean
cloth and solvent, and coat both with clean
refrigerant oil.
Dip the new "0" ring in clean refrigerant
oil and install in seal plate.
Press the seal bellows assembly into place.
It is not a metal to metal press fit, but rests
only on the neoprene "0" ring in the seal
plate and must go in perfectly square and the
flange must bottom all the way around against
the seal plate.
Wash the seal seat in clean solvent and dry
with a clean cloth. Dip in clean refrigerant
oil with the neoprene "0" ring in place. Press
onto shaft evenly with the lapped surface
toward the compressor body. After the seal
face is over the spline of the shaft, install
the snap ring over the spline using reverse
"Truarc" pliers. Do not spread the snap ring
more than necessary. Slide the seal ring and
snap ring together onto the shaft until the
snap ring snaps into its groove in the shaft.
Install the flywheel and clutch plate. The
cap screw lock plate is installed behind the
flat washer in the clutch hub. Torque tighten
the cap screw to 18-22 foot pounds torque and
lock in place with lock plate.
Install the compressor on the mounting
bracket; connect the magnetic clutch wire
lead. Install belts and adjust brackets and/or
idler shaft or power steering pump to tighten
belt tension.
Install the suction and discharge service
valves with the flexible lines intact to the
compressor using new gaskets. Torque the valve
body cap screws to 12 to 15 foot pounds torque.
The suction and discharge service valves
remain closed. Remove gauge port caps and
attach gauge manifold set and lines. The hand
valve on the compound gauge is closed and the
hand valve on the pressure gauge is open.
Start the engine and run the compressor for
a minute or two to pump the air out of the
compressor through the open hand valve and the
center gauge line. After the compressor and
engine are stopped, "crack" the suction
service valve slightly to force what air is
in the cylinder head out of the compressor
with Freon gas.
Close the hand valve on the pressure gauge.
"Crack" both service valves; operate and check
system for pressures and normal operation.
After running the compressor for 10 or 15
minutes, shut off system and check for leaks
with Halide Leak Detector. Oil around the seal
at this time does not indicate a seal leak as
there is a considerable amount on the new
parts when installed.
CAUTION:
Do not put pressure on the
crankcase unless the pulley and clutch
is held firmly in place by the spacer,
cap screw, and lock plate. Excessive
crankcase pressure and a defective snap ring
will allow the seal to be blown out of the
compressor.
NOTE:
Cleanliness, careful handling, and
clean refrigeration oil on all parts are
important for successful seal replacement.
Crankcase Oil Check Valve
There is a small self-operating check valve
between the passage where the refrigerant gas
enters the compressor and the crankcase. Some
oil circulates through the entire system when
the compressor is running. Oil returning with
the suction gas from the evaporator opens the
check valve and flows directly into the
crankcase and the refrigerant gas flows upward
to reduce the amount of oil pumped out of the
compressor after a prolonged idle period. Oil
and Freon-12 are miscible, each in the other
and during such periods, the oil in the
crankcase absorbs some refrigerant. When the
compressor is started under such conditions,
the check valve is closed to a small orifice
by the crankcase pressure so that the pressure
reduces slowly, minimizing foaming of the oil
and the consequent oil pumping.
Service Diagnosis of Compressor
An inefficient compressor is one in which
either or both the suction valve or discharge
valves leak. Both suction and discharge valves
must seat properly to insure efficient opera-
tion to have a compressor that is functioning
up to its capacity. The symptoms of ineffi-
ciency vary with the extent of trouble.
A compressor should be warm when testing as
a cold compressor is not operating at its
greatest efflciency. Turn the compressor over
by hand. A definite compression should be
noted. However, upon turning over at the top
of the compression stroke, there should be no
tendency of the flywheel to follow around. If
it does follow around, a discharge valve leak
is indicated. As a further test, with no
refrigerant in the system, attach compound
gauge to gauge port and close the compressor
suction service valve. Run the compressor for
intermittent intervals of a few seconds dura-
tion and allow to rest for a minute or so in
between. This will allow the Freon to separate
from the oil in the crankcase. This also will
reduce the crankcase pressure. After this has
been done, run a vacuum check. If this
procedure is not followed, false reading may
indicate valve weakness and crankcase oil may
be pulled out. The rapidity with which the
compressor can pump a vacuum determines its
efficiency. In general, a good compressor will
pump down to a 12" or 18" vacuum or better.
A further test is to start the system with a
pressure gauge in place on the discharge
service valve. Close the valve; pump a pressure
of 150 to 200 pounds into the gauge. This
pressure will be pumped rapidly.
Shut off as soon as 200 pounds is reached. If
the pressures hold, the discharge valve is good.
Содержание 1955 Rambler
Страница 1: ......
Страница 2: ......
Страница 3: ......
Страница 4: ......
Страница 28: ......
Страница 38: ......
Страница 42: ......
Страница 87: ...46 T E C H N I C A L S E R V I C E M A N U A L...
Страница 88: ...ELECTRICAL WIRING DIAGRAMS...
Страница 89: ......
Страница 90: ......
Страница 91: ...ELECTRICAL WIRING DIAGRAMS...
Страница 92: ......
Страница 93: ......
Страница 94: ......
Страница 95: ......
Страница 96: ......
Страница 97: ......
Страница 98: ......
Страница 99: ......
Страница 100: ......
Страница 101: ......
Страница 102: ......
Страница 103: ......
Страница 119: ......
Страница 127: ......
Страница 151: ...OVERDRIVE 5...
Страница 165: ......
Страница 178: ...14 TECHNICAL SERVICE MANUAL TECHNICAL SERVICE LETTER REFERENCE Date Letter No Subject Changes Information on Page No...
Страница 179: ......
Страница 199: ......
Страница 200: ...2 TECHNICAL SERVICE MANUAL...
Страница 223: ......
Страница 243: ......
Страница 250: ...8 TECHNICAL SERVICE MANUAL TECHNICAL SERVICE LETTER REFERENCE Date Letter No Subject Changes Information on Page No...
Страница 251: ......
Страница 255: ...ALL SEASON AIR CONDITIONING SYSTEM 5 Figure 2 Freon 12 Temperature Pressure Relation Curve...
Страница 287: ......
Страница 288: ......
Страница 289: ......
Страница 290: ...TECHNICAL SERVICE MANUAL TECHNICAL SERVICE LETTER REFERENCE Date Letter No Subject Changes Information on Page No...
Страница 291: ......
Страница 292: ......