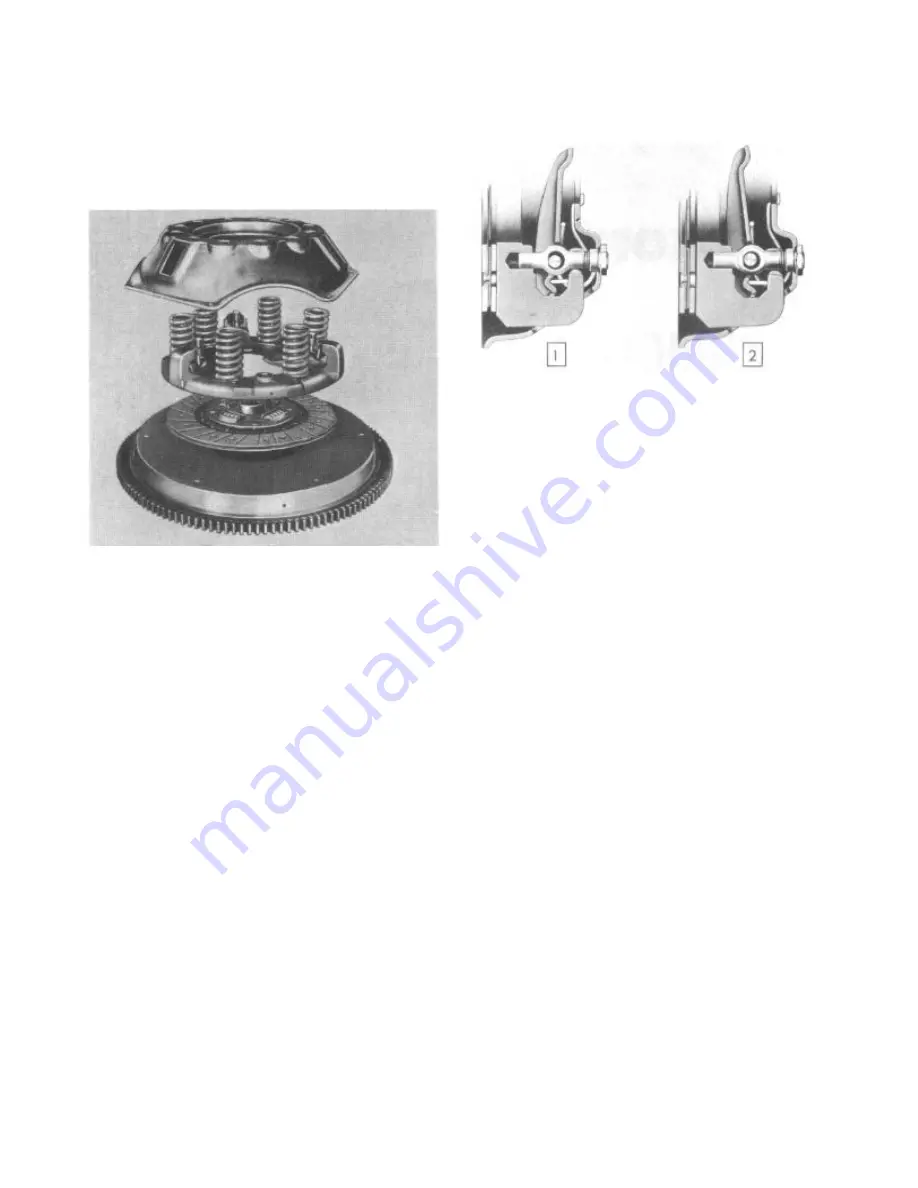
CLUTCH SECTION
The is a single plate, dry disc type. A steel
covet bolted to the flywheel contains the drive
plate, the pressure plate, levers, and springs
(Fig. 1).
FIGURE 1—Component Parts of Clutch
The clutch drive plate is spring cushioned with
a facing riveted to both sides. The coil springs
around the hub absorb the power shocks and
cushion the driving mechanism.
The clutch throw-out bearing is of the ball
type, packed at time of manufacture, and
requires no further lubrication.
No adjustment for wear is provided in the
clutch itself. An individual adjustment is built
into the clutch cover to adjust the height of
the release levers. This adjusting nut is locked
in position and should never be disturbed unless
the clutch assembly has been disassembled for
the replacement of worn parts.
When the clutch pedal is depressed, the
release bearing is moved toward the flywheel and
contacts the inner ends of the release levers.
Each lever is pivoted on a floating pin which
remains stationary in the lever and rolls across
a short flat portion of the enlarged hole in the
eyebolt. The outer ends of the eyebolts extend
through holes in the stamped cover and are fitted
with adjusting nuts to secure the levers in the
correct position. The outer ends of the release
levers engage the pressure plate lugs by means
of fulcrums, which provide knife-edge contact
between the outer ends of the levers and the lugs
(Fig. 2).
REMOVING THE CLUTCH ASSEMBLY
Always mark the cover, pressure plate and
flywheel on original production assemblies
before removing, so that when they are reassembled
1. Engaged Position
2. Released Position
FIGURE 2—Clutch Lever
they will be in their same relative positions
(Fig. 1).
CAUTION:
When removing the clutch cover
from the flywheel, loosen each cap screw
a few turns until the spring tension on
the cover has been released. The clutch
cover is a steel stamping which could be
sprung by incorrect removal, resulting in
clutch chatter when reused.
CRANKSHAFT PILOT BUSHING
When a assembly is removed from the flywheel,
always inspect the crankshaft pilot bushing
for scoring or loose condition. The bushing
may be removed by using a tap. After the tap
has bottomed in the bore, the bushing will be
forced out. To provide initial lubrication for
this bushing, coat lightly with a short fiber,
medium wheel bearing grease.
CLUTCH DISASSEMBLY
The clutch cover and pressure plate are under
spring tension at all times. Therefore, care
must be exercised when a cover assembly is
disassembled. Place the cover assembly in an
arbor press with a hard wood block under the
pressure plate. Have the block of such a
length that the cover can move down and not
interfere with the blocks. Place a wood block
across the top of the cover so that it rests
on the spring bosses and does not interfere
with the eyebolt adjust. ing nuts (Fig. 3).
Compress the clutch cover in the press
until the clutch release levers are free.
Remove the adjusting nuts (Fig. 3). Release
the press slowly to prevent the springs from
flying out.
CAUTION:
When relieving the spring
pressure, be sure the cover does not
stick on the pressure plate bosses.
Содержание 1955 Rambler
Страница 1: ......
Страница 2: ......
Страница 3: ......
Страница 4: ......
Страница 28: ......
Страница 38: ......
Страница 42: ......
Страница 87: ...46 T E C H N I C A L S E R V I C E M A N U A L...
Страница 88: ...ELECTRICAL WIRING DIAGRAMS...
Страница 89: ......
Страница 90: ......
Страница 91: ...ELECTRICAL WIRING DIAGRAMS...
Страница 92: ......
Страница 93: ......
Страница 94: ......
Страница 95: ......
Страница 96: ......
Страница 97: ......
Страница 98: ......
Страница 99: ......
Страница 100: ......
Страница 101: ......
Страница 102: ......
Страница 103: ......
Страница 119: ......
Страница 127: ......
Страница 151: ...OVERDRIVE 5...
Страница 165: ......
Страница 178: ...14 TECHNICAL SERVICE MANUAL TECHNICAL SERVICE LETTER REFERENCE Date Letter No Subject Changes Information on Page No...
Страница 179: ......
Страница 199: ......
Страница 200: ...2 TECHNICAL SERVICE MANUAL...
Страница 223: ......
Страница 243: ......
Страница 250: ...8 TECHNICAL SERVICE MANUAL TECHNICAL SERVICE LETTER REFERENCE Date Letter No Subject Changes Information on Page No...
Страница 251: ......
Страница 255: ...ALL SEASON AIR CONDITIONING SYSTEM 5 Figure 2 Freon 12 Temperature Pressure Relation Curve...
Страница 287: ......
Страница 288: ......
Страница 289: ......
Страница 290: ...TECHNICAL SERVICE MANUAL TECHNICAL SERVICE LETTER REFERENCE Date Letter No Subject Changes Information on Page No...
Страница 291: ......
Страница 292: ......