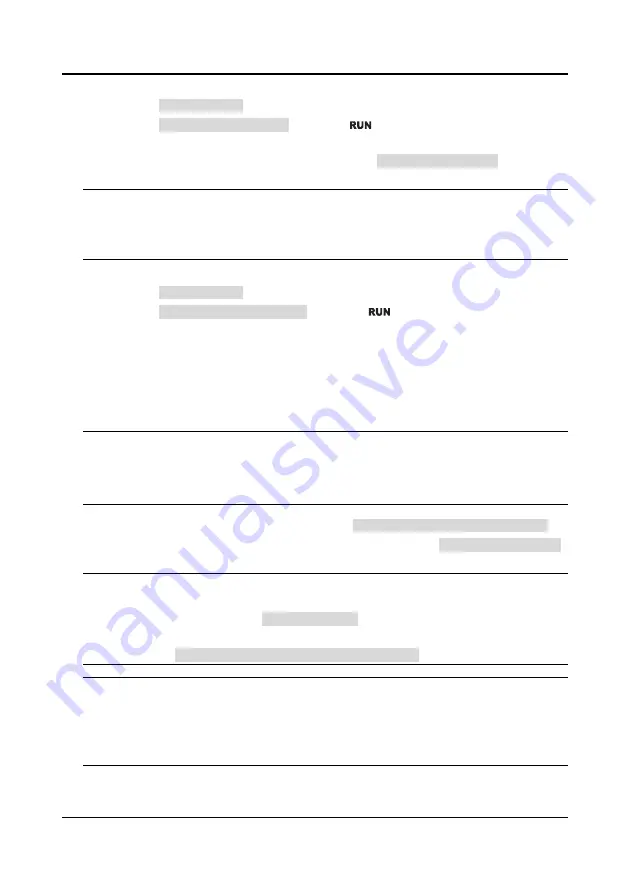
Chapter 7 Elevator Application Guidance
Shenzhen Hpmont Technology Co., Ltd.
―
82
―
HD5L Series Controller User Manual V1.4
Syn. motor rotary auto-tuning with serial communication encoder
1. Set F00.05 as 0 (keypad control).
2. Set F10.10 as 2 (rotary angle auto-tuning), then press
key to start parameter auto-tuning.
3. Auto-tuning steps: The controller with DC fixes the motor to one direction, then slowly starts the
motor for a while and finally stops. When auto-tuning finishes, F10.12 (motor start angle) will be
obtained.
Note:
1. During step 2 and step 3, manually open the brake contactor and the run contactor together.
2. If the system has syn. motor radial contactor, the short-circuit signal of radial contactor should be
removed. Otherwise it will cause over-current fault.
Syn. motor stationary auto-tuning with serial communication encoder
1. Set F00.05 as 0 (keypad control).
2. Set F10.10 as 1 (stationary angle auto-tuning), then press
key to start parameter auto-tuning.
3. During auto-tuning, the controller will make a serial pulse voltage and the motor will buzz. When
buzz is over and the keypad returns to stop status, please check and record D04.05.
4. Restart step 2 and step 3, check and record D04.05. Then compare the twice obtained value of
D04.05.
If the comparison value is smaller than 5000, it means that the steps are successful. Otherwise check
the encoder connection and then restart step 2 - 4.
Note of step 4:
If the comparison value is too large, you could count it according to the following formula. And if the result
is smaller than 5000, it means that the above steps are also successful.
Formula:
65535 + smaller value – larger value < 5000
5. Set F00.05 according to elevator control mode, and set F06.00 as 0 (no pre-torque compensation).
6. Set inspection run command and direction so that the motor slowly runs, F10.12 (motor start angle)
will be obtained the auto-tuning process is finished.
Pay attention to the following circumstances at step 6 of inspection running:
1. The setting direction and the actually running direction are not the same.
Take measures:
Set the reverse value of F00.08 (run direction), then restart auto-tuning.
2. There is fault such as over-current or encoder reversion enabled etc. It may be encoder reversion enabled.
Take measures:
Set F11.02 as 1 (the reverse direction of PG interface board), then restart auto-tuning.
.123
Note:
1. During step 2 and step 3, it needs manually open the run contactor.
2. If the system has syn. motor radial contactor, the short-circuit signal of radial contactor should be
removed. Otherwise it will cause over-current fault.
3. If the system is power off before step 6 finishes, restart auto-tuning.