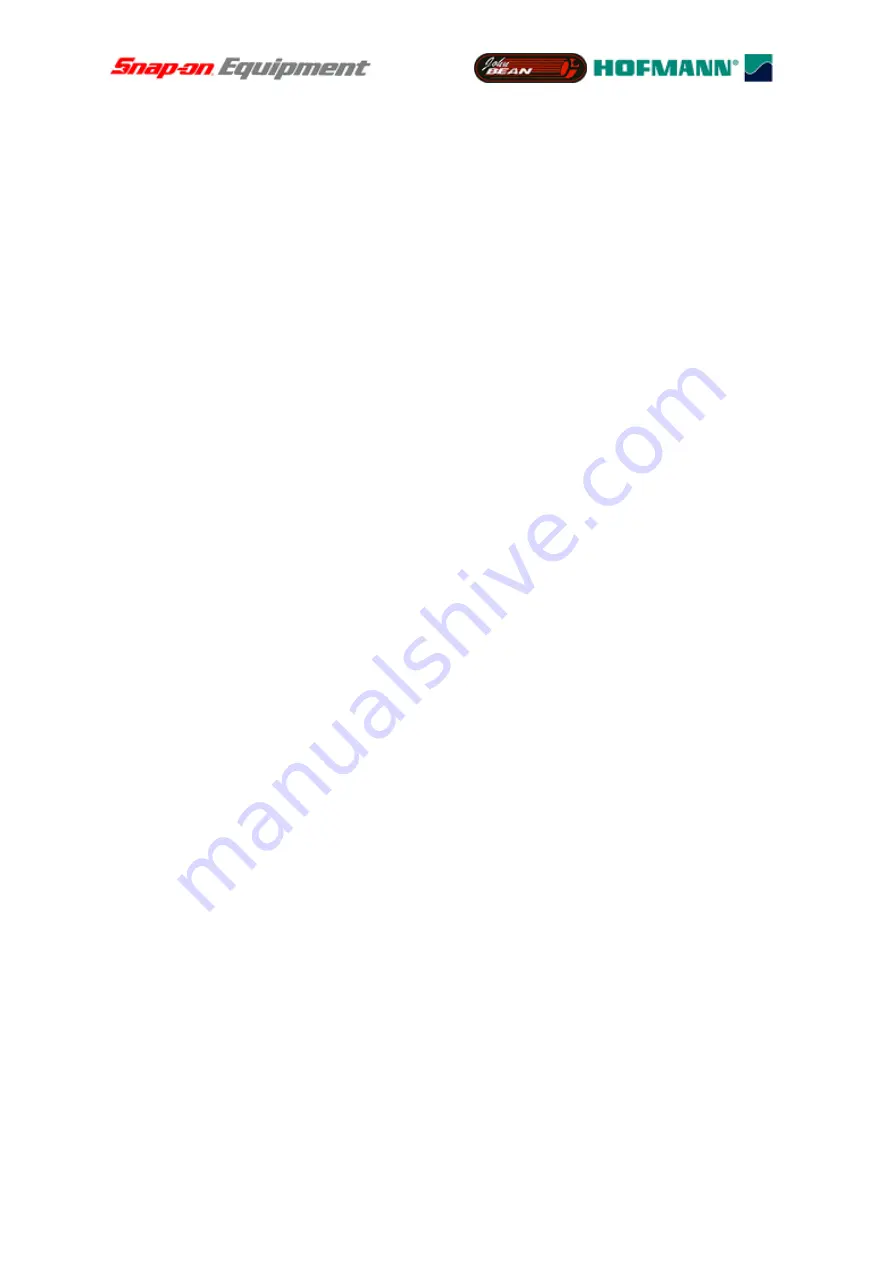
Non-volatile memory at Optoelectronic unit
Beside the EEPROM on the Controller board, there is a second non-volatile memory soldered
to the Optoelectronic unit. Both EEPROMs should hold the same data: machine model,
adjustment data, counts of counters, selected modes of operation and stored error-codes.
Having two non-volatile memories becomes beneficial when the Controller board or the
electronic box has to be replaced.
With service code C86, the contents of the EEPROM on the Optoelectronic unit can be copied
to the EEPROM located on the Controller board, saving to set machine model number via
C47 and to carry out calibration.
On power up self-test, the contents of the EEPROMs are compared. If differing but valid data
is detected, with the
b9000
and
b9450
, C85 "Copy contents of the EEPROM on the Controller
board to the Optoelectronic unit" is displayed.
Do not un-plug connector X3 or X10 with power connected. A difference in memory contents
of the non-volatile memories may occur!
15.3.2 The Incremental encoder for the power-clamp
Incremental encoder B9 acquires the rotational travel, direction of rotation and the absolute
angular position of the big pulley at the vibratory assembly with power-clamp. The travel of
the tie-rod is derived by program from rotational travel of the pulley.
The pattern of a code strip, fixed to the circumference of the big pulley, is sensed optically by
an encoder board positioned 1-mm above the pulley.
The adhesive code strip (Snap-on P/N EAM0005D64A, HOFMANN Mat-Nr. 6419096)
consists of a transparent foil with alternating black and white zones (32 increments) printed
on.
CAUTION! The wider zone of the zero reference has to be positioned to the edge of the
pulley.
The small encoder board D72.6392 (Snap-on P/N EAP0201D20A, HOFMANN Mat-Nr.
6726392) carries four SMT reflective interrupters, some resistors, an integrated circuit (Hex-
Schmitt-Trigger) and a 4-position ribbon cable with receptacle.
The reflective interrupters A and A` respectively B and B` are placed with a radial offset of
half an increment, so the interrupters work in a push pull arrangement. The push pull mode of
operation makes the encoder insensitive to the light output of the infrared LEDs and the
reflectance of the code strip. The lateral offset of the interrupters A to A` respectively B to B`
is essential for the push pull operation for the zero reference as well. In this way the zero
reference marking with its 25 to 75% mark to space ratio can be mapped complementary on
the two tracks.
The analogue waveforms at the phototransistors of the interrupters are converted to sharp
edge square-waves with low output impedance by the Schmitt-Trigger circuit.
The encoder board is fastened via a plate screwed to a corner bracket to the stator of the
electromagnetic brake. The corner bracket and the plate serve also to keep the abrasion of the
brake lining away from the encoder. To compensate for lateral work tolerance, the encoder
board can be aligned to the code strip with the aid of the movable plate. The two standing
back edges of the encoder board should be in line with the left-hand edge of the code strip.
Incremental encoder B9 can be checked with code C98.
CAUTION! Too much abrasion from the brake lining on the encoder board or code strip will
degrade the function of the incremental encoder. Both parts should be cleaned with a soft
cloth or brush occasionally.
Seite 20 von 99
Содержание Snap-on Y2k
Страница 1: ...SERVICE of the Y2k balancing platform Seite 1 von 99 ...
Страница 2: ...The vibratory assemblies of the Y2k balancing platform L R L R S S M Seite 2 von 99 ...
Страница 10: ...S S M Fig 12 Two systems arranged one above the other with a parallel pair of springs Seite 10 von 99 ...
Страница 32: ......
Страница 35: ...Seite 35 von 99 ...
Страница 66: ...Seite 66 von 99 Figure 1 JBEG B9000 B9450 User Interface ...
Страница 67: ...Seite 67 von 99 Figure 2 JBEG B9460 User Interface ...