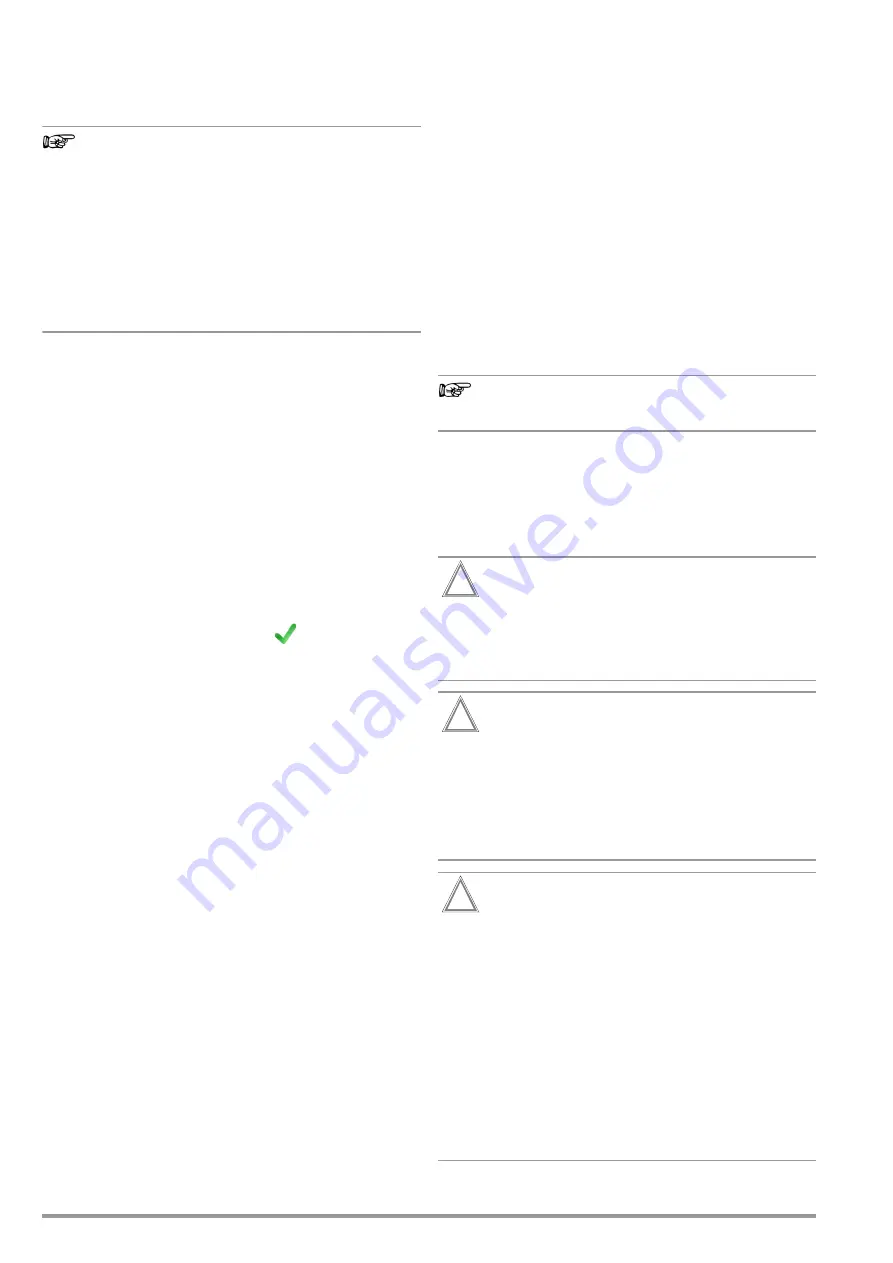
98
Gossen Metrawatt GmbH
A sticker with an instrument-specific guideline value for the cali-
bration interval and information regarding the service provider is
included on the test instrument as an aid.
A factory calibration certificate or test report is included with the
test instrument.
Note
Date on Calibration Certificate / Calibration Interval
Begins Upon Receipt
Your test instrument is furnished with a calibration certifi-
cate on which a date appears. This date may be further in
the past if your test instrument has been stored for some
time prior to sale.
The test instruments are stored in accordance with the
specified conditions. Drift is thus negligible for a duration
of 1 year and longer storage periods are highly unusual.
Consequently, the test instrument’s characteristics lie
within the specifications and the first calibration interval
can be determined as of the date of receipt.
20.6.2 Setting Calibration and Recalibration Dates
The calibration and recalibration dates are registered in the test
instrument:
•
The dates of the last adjustment and calibration are entered
by the calibration center.
•
Date and time of the next calibration (recalibration date) can
be adjusted, either on the tester itself or via a USB connec-
tion.
Viewing the Dates of the Last Adjustment and Calibration
Date and time of the last adjustment or calibration can be viewed
under SETUP > System Info 2/3 > Calibration Dates.
Changing the Recalibration Date at the Test Instrument
Date and time of the next recalibration can be changed under
SETUP > System Info 2/3 > Calibration Dates.
In order to change both as required, press the
EDIT
key and enter
the desired date and time. Confirm with
.
Changing the (Re)Calibration Date via USB Connection
Date and time of the next recalibration can also be set or changed
via the USB interface, for example with a terminal program.
The test instrument is connected to the PC via the USB port to
this end. Data is transferred bidirectionally via a virtual COM port.
The required driver can be installed via Driver Control software:
www.gossenmetrawatt.com/english/produkte/drivercontrol.htm
Communication between the PC and the test instrument is con-
ducted in UTF-8 format.
No checksums are generated for strictly ASCII responses. Com-
munication via the USB port is deemed secure thanks to native
CRC-16 checks.
Each command must be terminated with an LF line break (ASCII
10).
The test instrument must be restarted after data transmission, in
order for the changes to become effective.
Serial Port Settings:
Parameter
Value
Baud rate
9600 … 115,000 (freely selectable)
Data bits
8
Parity
none
Stop bits
1
Setting the Calibration Date:
IDN:SET:CALIB_DATETIME 2016-11-11T10:11:12
(the Thh:mm:ss time setting is optional)
Setting the Recalibration Date:
IDN:SET:RECALIB_DATETIME 2017-11-11T10:11:12
(the Thh:mm:ss time setting is optional)
20.7
Software/Firmware Update (system info parameter)
The current firmware or software version can be queried via
SETUP
2/3
>
System Info 1/3
>
Software Version
.
The test instrument’s firmware can be updated via the USB port
with the help of a PC.
Note
Adjustment data are not overwritten during updating, and
thus recalibration is unnecessary.
Updating is only possible via the proprietary
Firmware Update Tool
.
As a registered user (if you’ve registered your test instrument),
you’re entitled to download the
Firmware Update Tool
and the cur-
rent firmware version free of charge from the
myGMC
page at
www.gossenmetrawatt.com
.
Operating instructions for the
Firmware Update Tool
are available
here as well.
Attention!
!
Data loss!
Before updating the firmware, be sure to save the struc-
tures you’ve created and your measuring data, because
they might be deleted during the update process (see
section 19.3 “Backup and Restore via USB Flash Drive”).
Attention!
!
Damage to the test instrument due to faulty firmware up-
date!
The test instrument:
– must be directly and securely connected to the PC via
USB during the update (no virtualized environments,
no USB virtualization)
– may not be disconnected from supply power during
the update
Attention!
!
Update from Software/Firmware 3.2.0 or Lower to Software/
Firmware 3.3.0 or Higher
The update changes the rotary switch position assign-
ments (A1 … A9), as well as how the standards are
shown at the test instrument, in the test data and in the
test reports!
Due to the fact that the standard display can’t be
changed retroactively, you’ll have to reconfigure your test
instrument immediately after updating the firmware. See
“Selecting a Designation and Deactivating Standards in
Case of Update or Extension (enabling function)” on
page 22.
If different rotary switch position assignments are de-
sired, these must also be customized. Corresponding in-
formation can also be found in the above-mentioned
section.
Содержание SECULIFE ST BASE 25
Страница 111: ...Gossen Metrawatt GmbH 111 ...