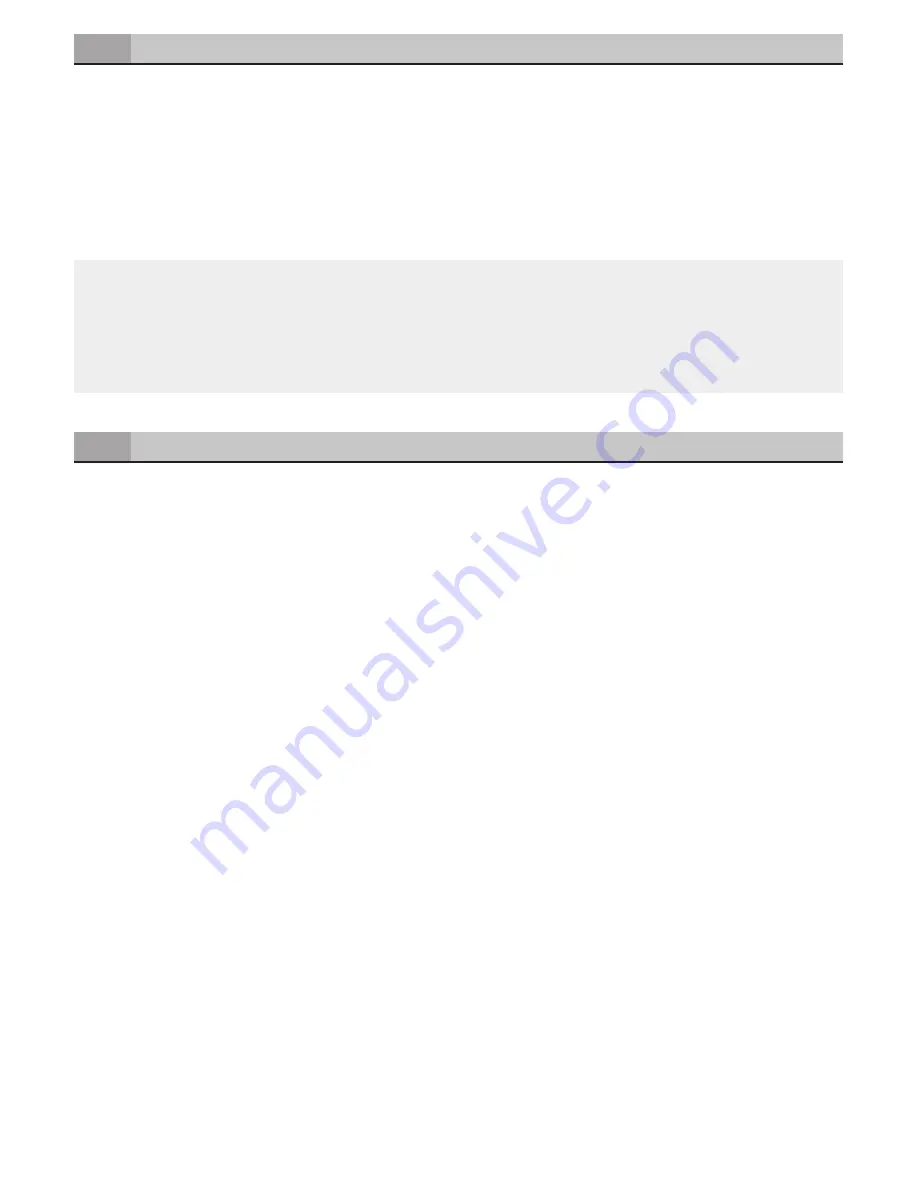
www.goetze-armaturen.de
Assembly and maintenance instructions - 481/681, 482/682
5
Replacing the Valve Insert
Type : 681 SP/ 481 SP/ 682 SP/ 482 SP /
681 HP/ 481 HP/ 682 HP/ 482 HP:
1. Remove plastic protective cap; loosen counter-nut
2. Tension spring by turning the setting spindle counter-clockwise
3. Unscrew spring housing or remove screws
4. Remove spring housing, spring plate, setting spindle, copper ring and spring.
5. By means of 2 screwdrivers lever-out the complete valve insert ( fig. a) and
replace with a new one. In the case of DN65, DN80, DN100 re-fit two screws on
opposite sides of the body, as these are required as supports for the screwdri-
vers ( fig. b)
6. Installation is carried-out in reverse order. For nominal width DN65, DN80,
DN100, tighten screws equally, the maximum tightening torque may not be
exceeded! For DN65 and DN80, the maximum torque is 20Nm, for DN100 the
maximum torque is 30Nm.
Fig. a): Removal and installation of control unit 681 / 481 / 682 / 482 (DN15 - DN50)
Fig. b): Removal of control unit 682 / 482 (DN65 - DN100)
Type : 681 LP/ 481 LP/ 682 LP/ 482 LP:
1. Remove plastic cap, release lock nut (do not unscrew!)
2. De-tension the spring by turning the setting spindle clockwise.
3. Release and unscrew bonnet with open end spanner
4. Remove spring and slide ring
5. Release and unscrew hexagon nuts with open end spanner and screwdriver
(fig. c)
6. Remove spring seat
7. Loosen membranes on the outer figmeter along entire length with a screwdriver
and unscrew (fig. d)
4
Maintenance
According to DIN EN 806-5, an annual inspection and service at least must be per-
formed, in order to correct possible malfunctions that which can arise due to dirt,
corrosion, calcification and natural wear. This interval may be shortened, depending
on the operating conditions.
During this service, the sieve must be cleaned, the good condition of the valve
insert must be checked and if necessary must be replaced.
After long periods of non-use the function of the valve must be tested.
Caution!!!
When carrying out assembly work on the pressure reducer the corresponding
system part must always be relieved of pressure and emptied, depending on the
medium used. At high temperatures you must always wait for the temperature to
cool down to ambient temperature.