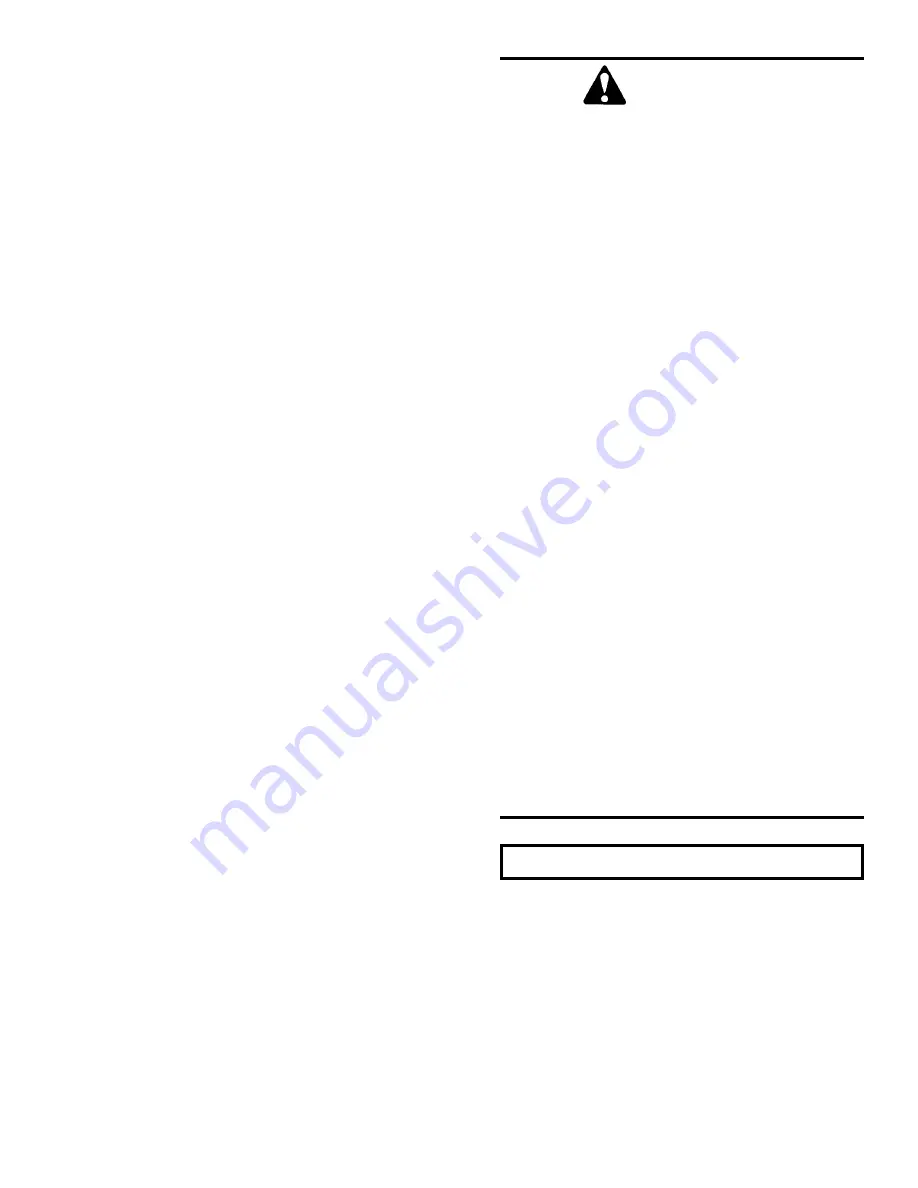
ELECTRICAL COMPONENTS
An Electrical system diagram is provided which
includes instrumentation, electrical components and
switch connections. The schematic (located at the end
of this chapter) can be used as a guide for trou-
bleshooting and service reference, as required.
OPERATOR SERVICES
Some of the operator related services will require
access to components located inside the superstructure
under shields, hoods and covers.
Choose a clean, level work area. Make sure you have
sufficient room, clearances, and adequate ventilation.
Clean the walking and working surfaces. Remove oil,
grease and Water to eliminate slippery areas. Utilize
sand or oil absorbing compound, as necessary, while
servicing the Paver.
Before starting inspection and repair, move the Paver
onto a level surface, shut down Engine, and release all
hydraulic pressure. Always lower the Hopper to “full
down” position. If the area under the Hopper requires
service, raise the Hopper to “full up” and swing up the
two Safety Props. Place all controls in neutral.
Disconnect the Battery and remove the Ignition Key.
Remove only guards or covers that provide needed
access. Wipe away excess grease and oil.
Excessively worn or damaged parts can fail and cause
injury or death. Replace any cracked or damaged part.
Care should be taken to assure that all replacement
parts are interchangeable with original parts and of
equal quality.
Use care NOT to damage machined and polished sur-
faces. Clean or replace all damaged or painted over
plates and decals that can NOT be read.
NOTE:
NEVER leave guards or access off when
the Paver is unattended. Keep bystanders away if
access Covers are removed.
After servicing, check the work performed, NO parts
left over, etc. Install all guards, covers and reconnect
the Battery.
SPRAY DOWN ASPHALT CONTACT
AREAS
The following areas should be sprayed with asphalt
releasing agent before paving, at least four times dur-
ing operation, and after each use of the Paver.
1. Hopper and Augers
2. Screed (bottom)
3. Push Roller Assembly
WARNING
Do NOT smoke or allow any open flames in the
area while checking and/or servicing
hydraulic, battery or fuel systems; all contain
flammable liquids or explosive gases which
can cause an explosion or fire if ignited.
Wear a face shield when you disassemble
spring loaded components or work with
Battery acid. Wear a helmet or goggles with
special lenses when you weld or cut with a
torch.
When working beneath a raised machine,
always use blocks, jack-stands or other rigid
and stable supports. Wear appropriate protec-
tive clothing, gloves, shoes. Keep feet, cloth-
ing, hands and hair away from moving parts.
Always wear safety glasses or goggles for eye
protection from electric arcs from shorts, flu-
ids under pressure, and flying debris or loose
material when the Engine is running or tools
are used for grinding or pounding.
NEVER weld on Bucket, forks, boom, support
frame or overhead guards without the consent
of the manufacturer. Special metals may be
used which require special welding tech-
niques or have a design which should NOT
have welded repairs. NEVER cut or weld on
fuel lines or tanks.
If repair welding is ever required, BE SURE to
attach the ground (-) cable from the welder as
close as possible to the area to be repaired.
Also remove Battery (+) positive terminal con-
nection before proceeding to weld
Daily or 10 Hours
Printed In U.S.A.
45
907389/AP297
Discount-Equipment.com
Содержание PowerBox 1639
Страница 13: ...SAFETY Continued Printed In U S A 13 907389 AP297 D i s c o u n t E q u i p m e n t c o m...
Страница 14: ...SAFETY Continued 907389 AP297 14 Printed In U S A D i s c o u n t E q u i p m e n t c o m...
Страница 54: ...1639 Electrical Schematic 907389 AP297 56 Printed In U S A D i s c o u n t E q u i p m e n t c o m...
Страница 55: ...1649 Electrical Schematic Printed In U S A 57 907389 AP297 D i s c o u n t E q u i p m e n t c o m...
Страница 65: ...INTERNATIONAL SYMBOLS D i s c o u n t E q u i p m e n t c o m...