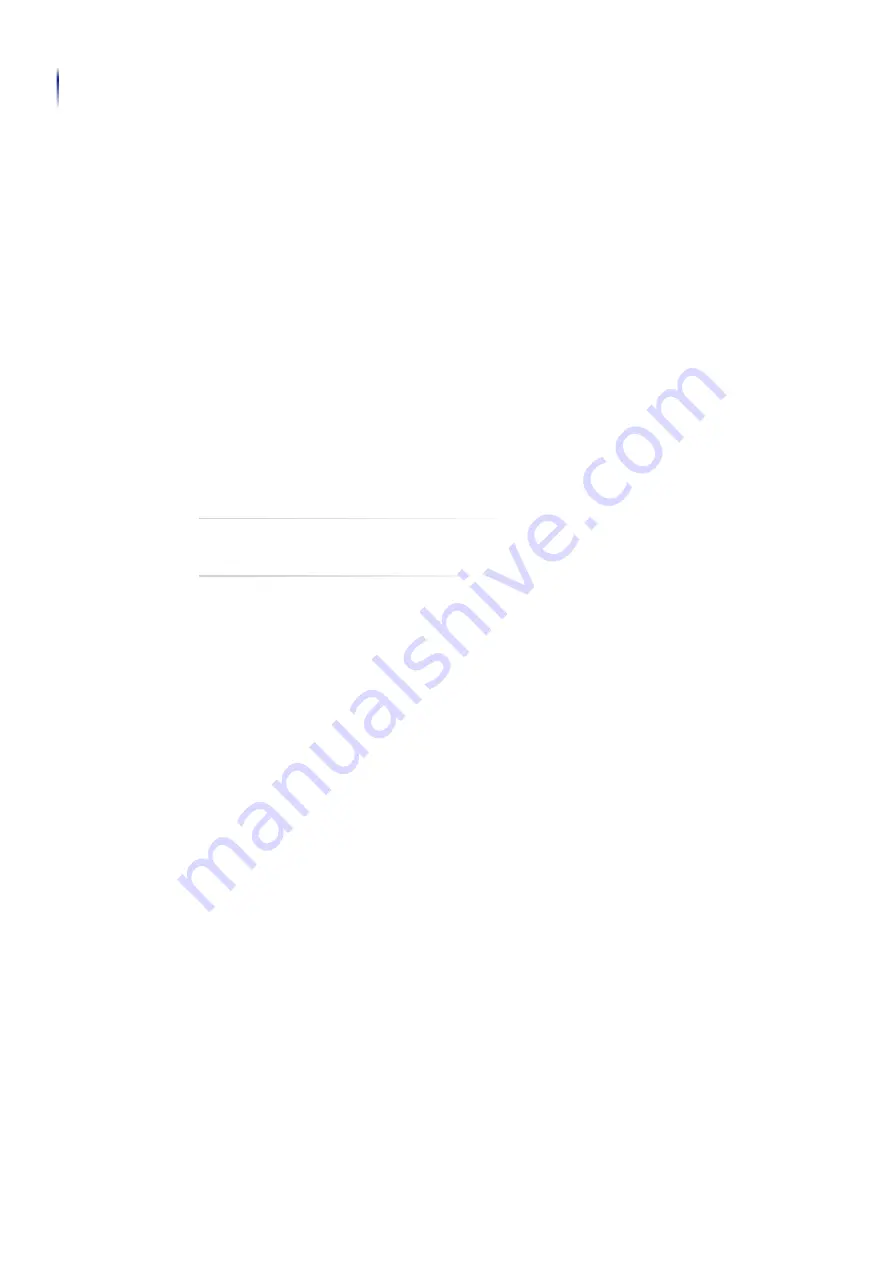
Safety
Qualification of Staff
10
Operating Instructions · GEA Index Cleaner Fury 602
Edition 01/08/2016
The operator's duty of care includes planning the necessary safety measures and moni-
toring that these measures are observed. The following principles apply:
•
Only allow qualified staff to work on the cleaner.
•
The operator must authorize the staff to carry out the relevant tasks.
•
Working areas and the entire environment of the cleaner must be neat and clean.
•
The staff must wear suitable work clothing and personal protective equipment. As
the operator of the facility make sure that work clothing and personal protective
equipment are used.
•
Instruct the staff with regard to any properties of the product which might pose a
health risk and the preventative measures to be taken.
•
Have a qualified first-aider on call during the operation, who can initiate the neces-
sary first-aid measures in case of an emergency.
•
Clearly define processes, lines of authority and responsibilities associated with the
cleaner. Everybody must know what to do in case of an emergency. Instruct the staff
in this respect at regular intervals.
•
The signs relating to the cleaner must always be complete and legible. Check, clean
and replace the signs as necessary at regular intervals.
NOTE
Carry out regular checks. This way you can ensure that these measures are actually
observed.
Qualification of Staff
This section contains information about the qualifications that staff working on the
cleaner must have.
Operating and maintenance staff must
•
have the necessary qualification to carry out their tasks,
•
be instructed with regard to possible dangers,
•
know and observe the safety instructions given in the documentation.
Only allow qualified electricians to carry out work on the electrical equipment or have a
qualified electrician supervise the work.
Only allow specially trained staff to carry out any work on explosion-protected equip-
ment. When working on explosion-protected equipment observe the standards DIN EN
60079-14 for gases and DIN EN 50281-1-2 for dusts.
The following minimum qualifications are required:
•
Vocational training as a skilled worker who can work on the cleaner independently.
•
Sufficient instruction to work on the cleaner under the supervision and direction of a
qualified specialist.