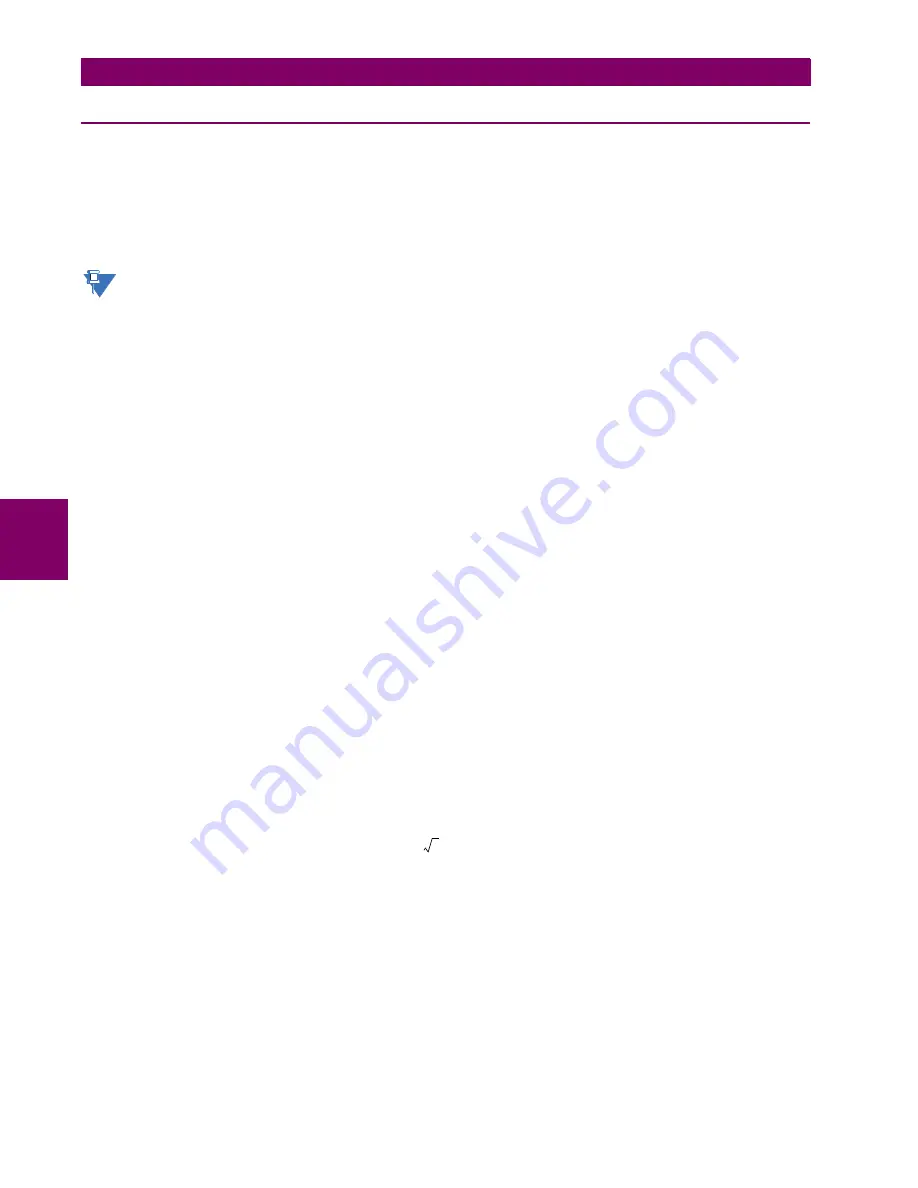
5-4
C70 Capacitor Bank Protection and Control System
GE Multilin
5.1 OVERVIEW
5 SETTINGS
5
5.1.2 INTRODUCTION TO ELEMENTS
In the design of UR relays, the term
element
is used to describe a feature that is based around a comparator. The compar-
ator is provided with an input (or set of inputs) that is tested against a programmed setting (or group of settings) to deter-
mine if the input is within the defined range that will set the output to logic 1, also referred to as
setting the flag
. A single
comparator may make multiple tests and provide multiple outputs; for example, the time overcurrent comparator sets a
pickup flag when the current input is above the setting and sets an operate flag when the input current has been at a level
above the pickup setting for the time specified by the time-current curve settings. All comparators use analog actual values
as the input.
An exception to this rule is digital elements, which use logic states as inputs.
Elements are arranged into two classes,
grouped
and
control
. Each element classed as a grouped element is provided with
six alternate sets of settings, in setting groups numbered 1 through 6. The performance of a grouped element is defined by
the setting group that is active at a given time. The performance of a control element is independent of the selected active
setting group.
The main characteristics of an element are shown on the element logic diagram. This includes the inputs, settings, fixed
logic, and the output operands generated (abbreviations used on scheme logic diagrams are defined in Appendix F).
Some settings are specified in per-unit (pu) calculated quantities:
pu quantity
= (actual quantity) / (base quantity)
Where the current source is from a single CT, the
base quantity
is the nominal secondary or primary current of the CT. Use
the secondary current base to convert per-unit current settings to/from a secondary current value, and use the primary cur-
rent base to convert to/from a primary current value.
Where the current source is the sum of two or more CTs with different nominal primary current, the primary base quantity is
the largest nominal primary current. For example, if CT1 = 300 / 5 A and CT2 = 100 / 1 A, then in order to sum these, CT2
is scaled to the CT1 ratio. In this case, the base quantity is 300 A primary, 5 A secondary for CT1, and 300/(100/1) = 3 A
secondary for CT2.
For voltage elements the primary base quantity is the nominal phase-to-phase primary voltage of the protected system pro-
vided that the VT ratio setting is set to the nominal ratio of the VTs and the secondary voltage setting is set to the phase-to-
phase voltage seen by the relay when the voltage of the protected system in nominal. The UR uses the convention that
nominal voltages in a three-phase system are phase-to-phase voltages.
For example, on a system with a 13.8 kV nominal primary voltage, the base quantity is 13800 V. With 14400:120 V delta-
connected VTs, the secondary base quantity and secondary voltage setting is:
(EQ 5.1)
For wye-connected VTs, the primary and secondary bases quanitities are as before, but the secondary voltage (here a
phase-to-phase ground value) is:
(EQ 5.2)
Many settings are common to most elements and are discussed below:
•
FUNCTION setting:
This setting programs the element to be operational when selected as “Enabled”. The factory
default is “Disabled”. Once programmed to “Enabled”, any element associated with the function becomes active and all
options become available.
•
NAME setting:
This setting is used to uniquely identify the element.
•
SOURCE setting:
This setting is used to select the AC source to be monitored. See the Introduction to AC Sources
section later.
•
PICKUP setting:
For simple elements, this setting is used to program the level of the measured parameter above or
below which the pickup state is established. In more complex elements, a set of settings may be provided to define the
range of the measured parameters which will cause the element to pickup.
NOTE
13800
14400
----------------
120
×
115 V
=
13800
14400
----------------
120
3
----------
×
66.4 V
=
Содержание C70
Страница 10: ...x C70 Capacitor Bank Protection and Control System GE Multilin TABLE OF CONTENTS ...
Страница 30: ...1 20 C70 Capacitor Bank Protection and Control System GE Multilin 1 5 USING THE RELAY 1 GETTING STARTED 1 ...
Страница 394: ...5 270 C70 Capacitor Bank Protection and Control System GE Multilin 5 10 TESTING 5 SETTINGS 5 ...
Страница 452: ...8 18 C70 Capacitor Bank Protection and Control System GE Multilin 8 1 OVERVIEW 8 THEORY OF OPERATION 8 ...
Страница 474: ...9 22 C70 Capacitor Bank Protection and Control System GE Multilin 9 4 SETTING EXAMPLE 9 APPLICATION OF SETTINGS 9 ...
Страница 486: ...10 12 C70 Capacitor Bank Protection and Control System GE Multilin 10 6 DISPOSAL 10 MAINTENANCE 10 ...
Страница 630: ...B 110 C70 Capacitor Bank Protection and Control System GE Multilin B 4 MEMORY MAPPING APPENDIX B B ...
Страница 676: ...E 10 C70 Capacitor Bank Protection and Control System GE Multilin E 1 OVERVIEW APPENDIX E E ...
Страница 688: ...F 12 C70 Capacitor Bank Protection and Control System GE Multilin F 2 DNP POINT LISTS APPENDIX F F ...
Страница 698: ...H 8 C70 Capacitor Bank Protection and Control System GE Multilin H 3 WARRANTY APPENDIX H H ...