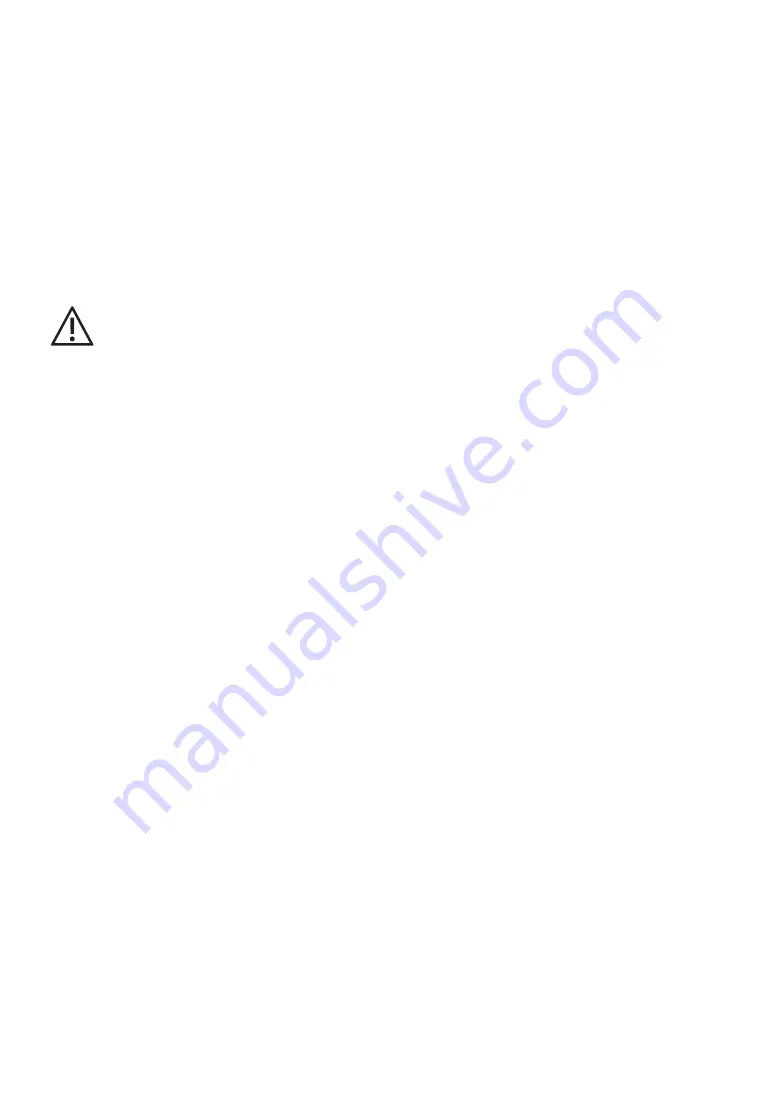
39
Page 16
Inspection of the rotor-head linkage:
Call a helicopter programme with a 3-point 120° swash-plate control (HR-3) on your remote control transmitter and set the
servo paths in the swash plate mixer programme to 50%.
1.
Move the pitch control lever from bottom upwards and ensure that the swash plate also moves horizontally from
bottom up. In the centre position of the control lever, the levers of the three swash plate servos must be horizontally
aligned. If required, change the motion direction of individual servos.
2.
Move the control lever to the right and then to the left for the roll function. The swash plate then also has to tilt to the
right and then to the left. If the swash plate motions are opposite to the control directions, change the running direction
for the roll function at the transmitter (reverse setting).
3.
Move the control lever for the nod function to the front and then back. The swash plate then also has to tilt to the front
and then to the back. If the swash plate motions are opposite to the control directions, change the running direction for
the nod function at the transmitter (reverse setting).
Important!
The swash plate motions for the roll and nod functions should equally strong in all directions.
4.
Check the centre position of the servo. If the control lever for the pitch function is in the centre position, the servo
levers must be aligned perfectly horizontally. Strong malpositions of the servo levers can be removed by repositioning
the servo lever. The fine settings are made with the sub-trimming function at the transmitter.
5.
Check the angle of attack of the rotor blades with a rotor blade setting gauge. If the control lever for the pitch function
is in the centre position, the angle of attack of the rotor blades should be 0°. If required, re-adjust the angle with the
linkage rod „B“ (see page 14).
6.
At correct settings, the servo levers, swash plate, pitch compensator levers and paddles must be aligned horizontally
when the control lever is in its centre position.
7.
Push the control lever for the pitch function to the top position. The angle of attack of the rotor blades now has to be
between 11° and 13°. The pitch curve at the transmitter should be set linearly (see page 17, lower right figure). If the
control lever for the pitch function is moved to the bottom-most position, the rotor blades must reach an angle of attack
of -11° to -13°. If required, set the pitch function with the swash plate mixer or the servo path setting at the transmitter.
These settings are required for the flight mode „freestyle“.
8.
For the flight mode „normal“, light the pitch curve in the bottom-most setting to 40 to 45%. Lift the pitch curve to 55
to 60% in the middle range. The rotor-blade angle of attack should then be -2° or -3° in the bottom-most position of
the pitch control lever. In the centre position, the angle should be approx. 3°.
Pitch Settings:
1.
The entire pitch range for 3D flight manoeuvres comprises 30° (-15 to 15°)
2.
The recommended rotor head speed for hover flight should not exceed 3000 rpm. This may be verified with a speed
meter if required. If the helicopter is not stable in hover flight or reacts slowly, increase the rotor head speed. This can
be done by lowering the pitch curve in the middle range or by lifting the throttle curve.
3.
The included rotor blades are perfectly suitable for 3D-flight but should always be finely balanced.
The four sketches present the detail settings for the pitch values in the respective flight conditions. It is important for
verification that the rotor blade setting gauge is always aligned precisely with the paddle rod.