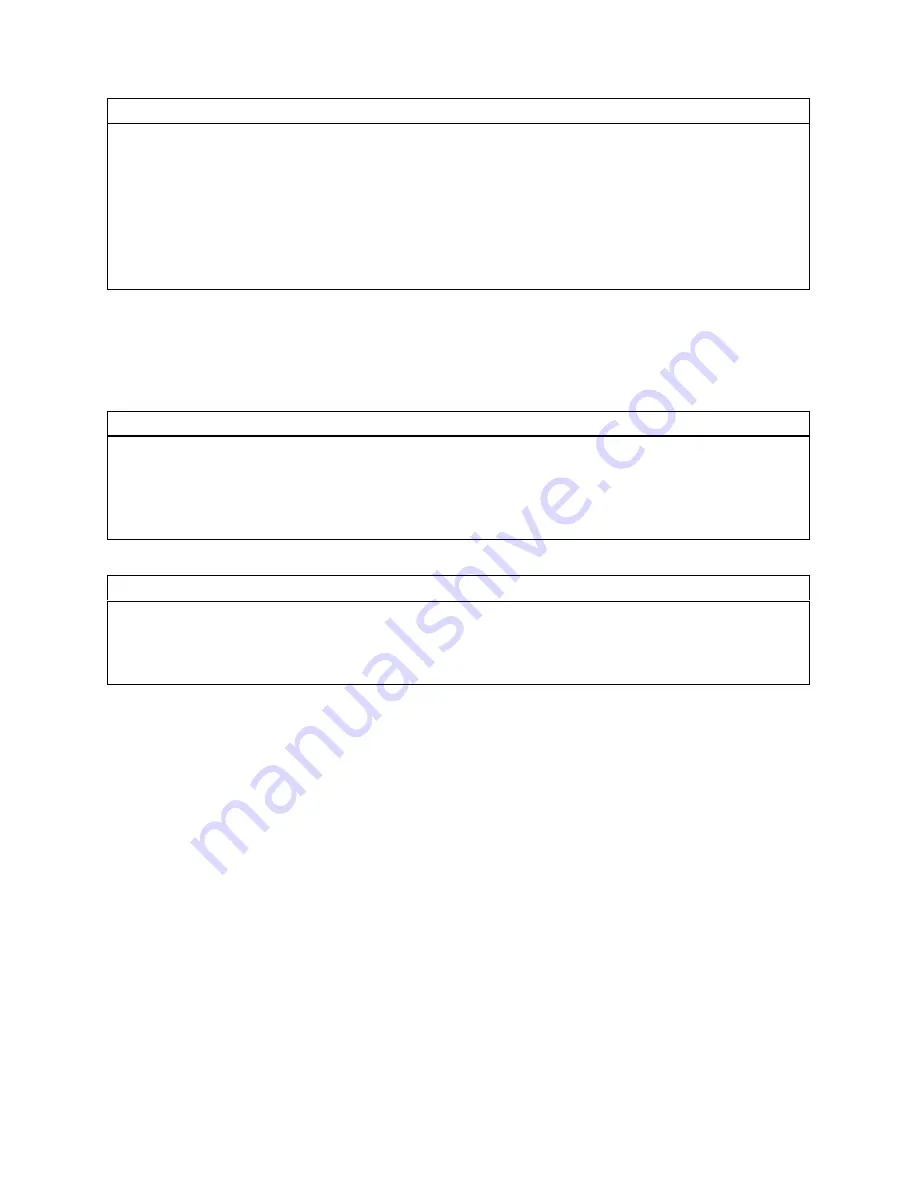
13-9-666 Page 46
NOTICE
When removing the cooling module from the package for remote operation, do
not use the flexible coupling (when supplied) between the air/oil separator
housing and the minimum pressure/check valve. The discharge piping from the
air/oil separator housing should be piped into the minimum pressure/check
valve, then into piping to the cooler, with a flexible connection between the
minimum pressure/check valve and aftercooler to keep the weight of the piping
off of the cooler.
HEAT EXCHANGER (OIL) PIPING
- All remote elevated cooler applications must be sent through
Engineering for approval and for recommending pipe size. When the cooling module is removed from the
package, the thermal mixing valve (H) remains on the package. Control group part number 200ECM4002
will be mounted on package at the factory. This group controls the oil stop valve as well as not allowing
machine to run blown down. See Figure 5-4, page 44.
NOTICE
Remote mounted elevated coolers have a maximum pipe length of 30 feet (9 M)
(each way) and a maximum height of 20 feet (6 M) with a minimum of fittings. A
remote elevated cooler form, J214, is required to be filled out. Customer
Service will review all forms while in the quote stage. Customer Service will
include the filled out J214 form on any special orders sent to Engineering.
NOTICE
When removing the cooling module from the package for remote operation, the
oil stop valve and the check valve that are shipped loose should be mounted as
close to the compressor package as possible. Flexible connections should be
used to keep the weight of the piping off of the cooler.
Kit number 301EAQ4013 (125-150 HP) or 301EDP4013 (200 HP) including the oil stop valve, check
valve and flanges must be installed on all remote elevated coolers per Figure 5-4, page 44, and the
following instructions:
1.
Mount the check valve (90J113) as shown.
2.
Mount the drain valves in the lowest section of the pipe on each side of the cooler connections.
3.
Mount the oil stop valve (90AR243) in the line after the thermal mixing valve as shown.
Modifications to the control lines will be made at the factory per 288ECM810 schematic. Air to the oil stop
valve must come from the upper fitting in the separator housing, then pass through the 3-way pneumatic
valve. Control air to the valve must be from the line between the tee and the orifice in the blowdown
muffler line per Figure 5-4, page 44. When the machine blows down, it will activate the pneumatic valve
and it will shut off the air and vent the line between the pneumatic control valve and the oil stop valve to
atmosphere. This will shut the oil stop valve and prevent excessive oil from running into the reservoir.
Failure to install these parts or installations with pipe lengths and/or vertical runs outside the
recommended limits could result in high oil carryover and cause the machine to shutdown on
high discharge temperature.
Содержание ELECTRA-SAVER EAQ99Q
Страница 10: ...13 9 666 Page 3 Figure 1 4 COMPRESSOR MOTOR SIDE Figure 1 5 COOLER RESERVOIR SIDE 200EDM797 A Ref Drawing...
Страница 11: ...13 9 666 Page 4 Figure 1 6 AIR OIL FLOW DIAGRAM 202EDM797 Ref Drawing...
Страница 13: ...13 9 666 Page 6 DECALS 206EAQ077 212EAQ077 218EAQ077 211EAQ077 207EAQ077...
Страница 14: ...13 9 666 Page 7 DECALS 216EAQ077 217EAQ077 222EAQ077 221EAQ077 208EAQ077...
Страница 43: ...13 9 666 Page 36 Figure 4 13 WIRING DIAGRAM WYE DELTA EBQ EBU UNITS 300EDM546 A Ref Drawing...
Страница 44: ...13 9 666 Page 37 Figure 4 14 WIRING DIAGRAM FULL VOLTAGE EBQ EBU UNITS...
Страница 45: ...13 9 666 Page 38 Figure 4 15 WIRING DIAGRAM WYE DELTA EAQ EAU UNITS ONLY 301EAQ546 B Ref Drawing...
Страница 46: ...13 9 666 Page 39 Figure 4 16 WIRING DIAGRAM FULL VOLTAGE EAQ EAU UNITS ONLY 303EAQ546 Ref Drawing...
Страница 50: ...13 9 666 Page 43 Figure 5 3 FLOW DIAGRAM AIR OIL SYSTEM 203EDM797 A Ref Drawing...