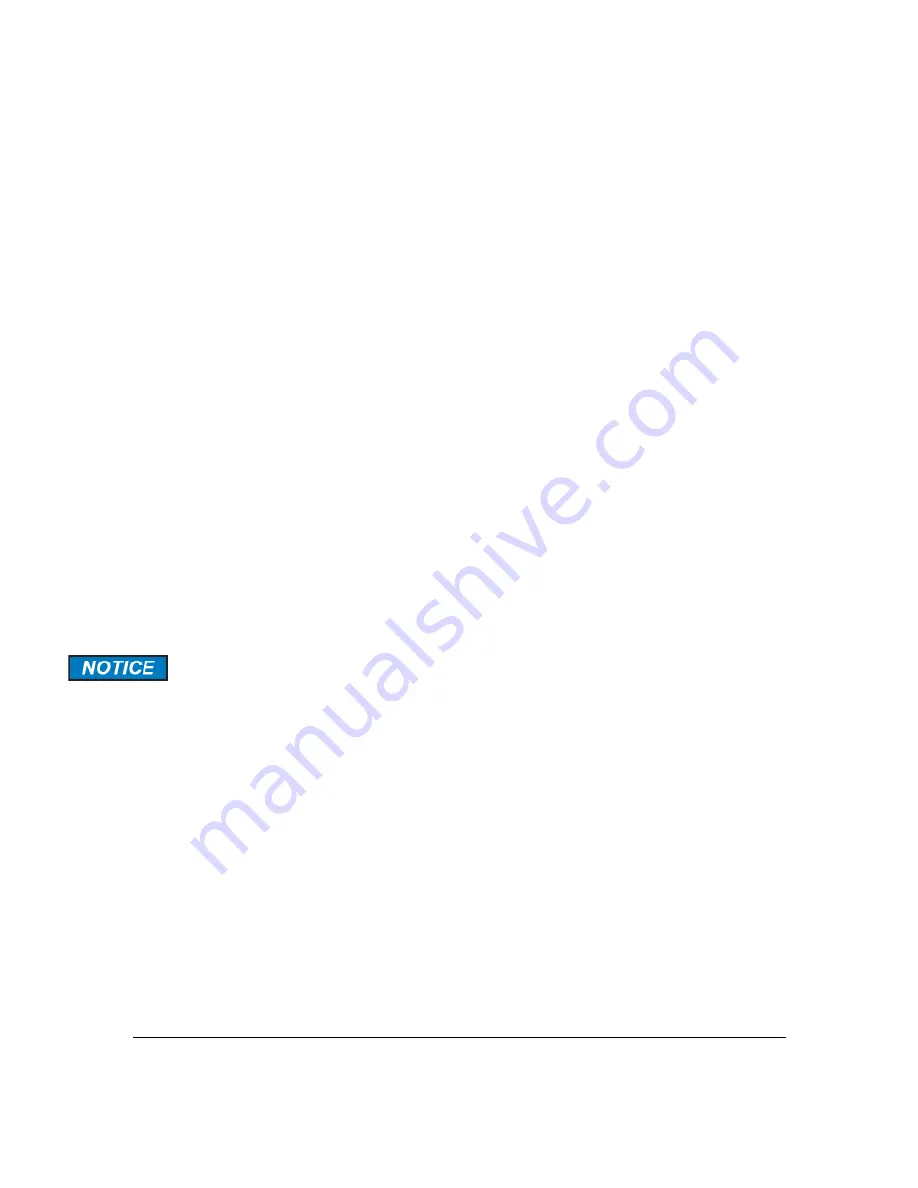
Revision 4
17
April 2020
(probe to vent) and allows readings to be taken through the measurement cell when no
absorbing species are present. To the sample system, zeroing and back purging are the same
thing. The default state (power ‘off’) of the analyzer is to have the sample system in the
back
purge
mode. Valving is provided for isolating the sample system components from the process
stream. A provision is included in the oven plumbing for the
steam purging
of the sample probe
after a plant shut-down or turn-around, or in the event of plugging of the sample probe, should
it be required.
A temperature-controlled
oven enclosure
maintains all components exposed to the tail gas
sample at higher than dew point values. The oven and sample probe are mounted to an interface
plate, which in turn is directly mounted to the steam heated process duct
sample nozzle
(typically a 2-inch, 150 pound pipe flange configuration). Electrical heat is applied to the
measurement cell to achieve precise temperature control of the entire oven enclosure, which
contains the measurement cell block and the associated sample handling system tubing and
valves.
1.5
System Operating Control
The analyzer system operation is controlled by a dedicated data acquisition system which
provides supervisory control of all analyzer inputs and outputs, performs all calculations, and
provides the user interface.
The system includes an onboard computer system which provides a graphic display of key
system control parameters and their status, a digital display of the instantaneous value of the
Air Demand, H
2
S, SO
2
, and COS, and historical graphic displays of the Air Demand, H
2
S and
SO
2
. The entire control computer system, consisting of a
Control Board
and a
Display Board
,
is mounted on the door of the control cabinet. Control cabinet access is not required for viewing
or operation.
The measurement of carbonyl sulfide (CS
2
) is an optional measurement. Analyzers
which have not been ordered with this option cannot measure CS
2
.
Four loop-powered 4
– 20 mA
analog outputs
are provided for the output of analyzer
measurement parameters. These four analog outputs are user-configurable for the output
parameter and range. Additionally, four solid-state relay outputs are provided for the output of
system status data. An RS485 serial port is also provided which can be used for available for
Modbus
communication. Two Ethernet ports are provided for use either for Modbus TCP/IP
communication OR for connection of a computer for GUI access. Aside from the Ethernet ports,
which are located on the control board,
all inputs and outputs are found on the analyzer’s
Input
/ Output Board
inside the control cabinet.
A handheld
keypad
is provided for user interface with the analyzer. Operation of the system
with the keypad is described in Section 4. As an alternative, a web based graphical user
interface (GUI) can be used to view and enter information on a remote basis. Operation using
the
web GUI
is described in Section 5.
Содержание 943-TGX-CE
Страница 132: ...Revision 4 132 April 2020 Figure 81 Oven Cabinet Door Removed ...
Страница 133: ...Revision 4 133 April 2020 Figure 82 Control Cabinet Door Removed ...
Страница 134: ...Revision 4 134 April 2020 Figure 83 Power Steam Air Signals Connection Details ...
Страница 135: ...Revision 4 135 April 2020 Figure 84 AC Wiring Schematic ...
Страница 136: ...Revision 4 136 April 2020 Figure 85 DC Signals and Wiring Diagram ...
Страница 137: ...Revision 4 137 April 2020 Figure 86 Flow Diagram ...