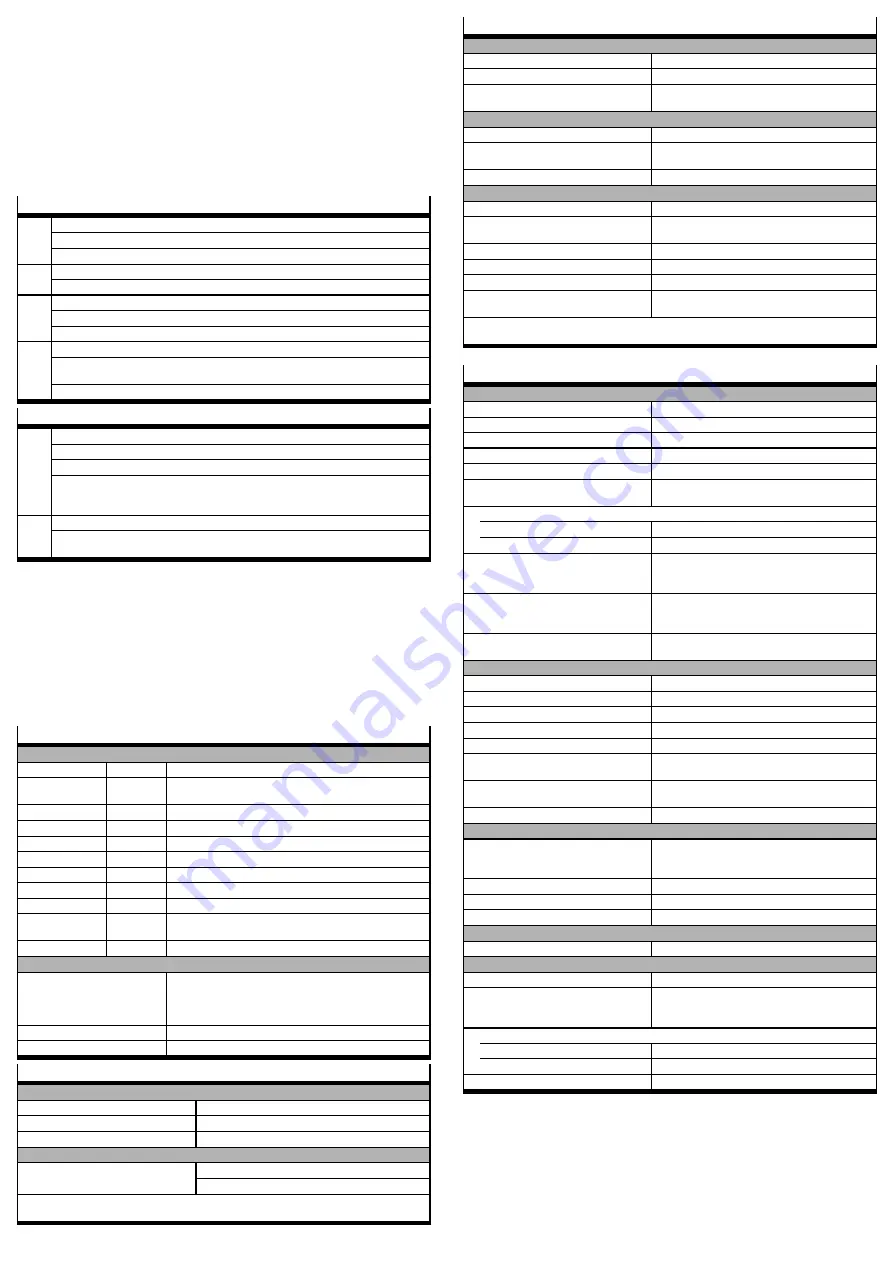
9.2 Error messages
The motor controller displays malfunctions cyclically in the 7-segments display on
the front side of the motor controller. Error messages with “E” (for error), a main
index (xx) and a subindex (y) display, e.g. E 5 1 0. Warnings have the same number,
but are represented with previous and subsequent middle benches, e.g. - 1 7 0 -.
The error messages relevant for functional safety in combination with the safety
module CAMC-G-S1 are listed subsequently.
The complete list of error messages can be found in the hardware documenta-
tion GDCP-CMMP-M3-HW-... of the motor controller used.
Where error messages cannot be acknowledged, you must first eliminate the
cause. Then reset the motor controller, and check whether the cause of the error,
and the error message, have been eliminated.
Error group 51: Safety module/function
51-0
No/unknown safety module or driver supply faulty
Internal voltage error of the safety module or micro switch module.
No safety module detected or unknown module type.
51-2
Safety module: Unequal module type
Type or revision of the module does not fit the project engineering.
51-3
Safety module: Unequal module version
Type or revision of the module is not supported.
The module type is correct but the module version is not supported by the basic unit.
51-5
Safety module: Error in brake control
Internal hardware error (brake activation control signals) of the safety module or micro
switch module.
Error in brake driver circuit section in the basic unit.
Error group 52: Safety function
52-1
Safety function: Discrepancy time overrun
Control ports STO-A and STO-B are not actuated simultaneously.
Control ports STO-A and STO-B are not wired in the same way.
Upper and lower switch supply not simultaneously activated (discrepancy time exceeded)
Error in control / external circuitry of safety module.
Error in safety module.
52-2
Safety function: Failure of driver supply with active PWM control
This error message does not occur with equipment delivered from the factory. It can
occur with use of a user-specific device firmware.
10
Replacement of the safety module, repair
Repair of the module is not permissible. If necessary, replace the complete
module.
11
Removal from operation and disposal
Observe the local regulations for environmentally appropriate disposal of elec-
tronic modules.
12
Technical data
Safety engineering
Safety reference data
Safety function
STO
STO, Safe Torque Off in accordance with EN 61800-5-2
SIL
SIL 3 /
SIL CL 3
Safety integrity level in accordance with EN 61800-5-2 / EN
62061
Category
4
Grading in categories in accordance with EN ISO 13849-1
PL
Pl e
Performance level in accordance with EN ISO 13849-1
DCavg
[%]
97.5
Average diagnostic coverage
HFT
1
Hardware fault tolerance
SFF
[%]
99.2
Safe failure fraction
PFH
1.07 x 10
–10
Probability of dangerous failure per hour
PFD
2.3 x 10
–5
Probability of dangerous failure on demand
T
[Years]
20
Proof test interval
Operating life in accordance with EN ISO 13849-1
MTTF
d
[Years]
1450
Mean time to dangerous failure.
Safety information
Type test
The functional safety engineering of the product has been
certified by an independent testing body in accordance with
section 1.4, see EC-type examination certificate
www.festo.com
Certificate issuing authority
TÜV 01/205/5165.01/14
Reliable component
Yes
General
Mechanical
Dimensions (L x W x H):
[mm]
Approx. 112.6 x 87.2 x 28.3
Weight
[g]
Approx. 75
Note on materials
RoHS-compliant
Certifications (safety module CAMC-G-S1 for motor controller CMMP-AS-...-M3)
CE marking (see declaration of
conformity)
www.festo.com
In accordance with EU EMC Directive
In accordance with EU machine directive
The device is intended for industrial use. Measures for interference suppression may need to be
implemented in residential areas.
Operating and environmental conditions
Conveying
Permissible temperature range
[°C]
–25 … +70
Air humidity
[%]
0 ... 95, at max. 40 °C ambient temperature
Maximum transportation
duration
[Weeks]
Maximum 4 in the total product lifecycle
Storage
Permissible temperature range
[°C]
–25 … +55
Air humidity
[%]
5 ... 95, non-condensing or protected against
condensation
Permissible height
[m]
<
3000 (above sea level)
Ambient conditions
Ambient temperature
[°C]
0 … +40 (outside the motor controller)
Cooling
By means of ambient atmosphere in the motor
controller, no forced ventilation
Permissible setup altitude
[m]
<
2000 (above sea level)
Degree of protection
IP20 (mounted in the CMMP-AS-…-M3).
Air humidity
[%]
Relative air humidity up to 90 % non-condensing
Degree of contamination in
accordance with EN 61800-5-1
2
This must always be ensured through appropriate measures, e.g. through installation in a control
cabinet.
Electrical data
Control ports STO-A, 0V-A / STO-B, 0V-B [X40]
Nominal voltage
[V]
24 (related to 0V-A/B)
Voltage range
[V]
19.2 … 28.8
Permissible residual ripple
[%]
2 (related to nominal voltage 24 V)
Overvoltage discharge
[V]
31 (disconnect in case of error)
Nominal current
[mA]
20 (typical; maximum 30)
Starting current
[mA]
450 (typical, duration approx. 2 ms; max. 600 at
28.8 V)
Input voltage threshold
Switching on
[V]
Approx. 18
Switching off
[V]
Approx. 12.5
Switching time from high to
low
(STO-A/B_OFF)
[ms]
10 (typical; maximum 20 at 28.8 V)
Switching time from low to
high
(STO-A/B_ON)
[ms]
1 (typical; maximum 5)
Maximum positive test
impulse length at logic 0
[µs]
<
300 (related to nominal voltage 24 V and intervals
>
2 s between impulses)
Feedback contact C1, C2 [X40]
Version
Relay contact, normally open
Max. voltage
[V DC]
<
30 (overvoltage-proof up to 60 V DC)
Nominal current
[mA]
<
200 (not short-circuit proof )
Voltage drop
[V]
≤
1
Residual current (contact open) [µA]
<
10
Switching time closing
(T_C1/C2_ON)
[ms]
<
(STO-A/B_OFF + 5 ms)
Switching time opening
(T_C1/C2_OFF)
[ms]
<
(STO-A/B_ON + 5 ms)
Service life
[n
op
]
10 x 10
6
(at 24 V and I
Contact
= 10 mA
)
Auxiliary supply 24 V, 0 V [X40] – output
Version
Logic power supply of the motor controller.
Protected against reverse polarity,
overvoltage-proof up to 60 V DC
Nominal voltage
[V]
24
Nominal current
[mA]
100 (short circuit proof, max 300 mA)
Voltage drop
[V]
≤
1 (for nominal current)
Galvanic isolation
Galvanically isolated potential areas
STO-A / 0V-A; STO-B / 0V-B; C1 / C2; 24 V / 0 V
Cabling
Max. cable length
[m]
30
Screening
When wiring outside the control cabinet, use
screened cable. Guide screening into the control
cabinet / attach to the side of the control cabinet.
Cable cross section (flexible conductors, wire end sleeve with insulating collar)
One conductor
mm²
0.25 … 0.5
Two conductors
mm²
2 x 0.25 (with twin wire end sleeves)
Tightening torque M2
[Nm]
0.22 … 0.25