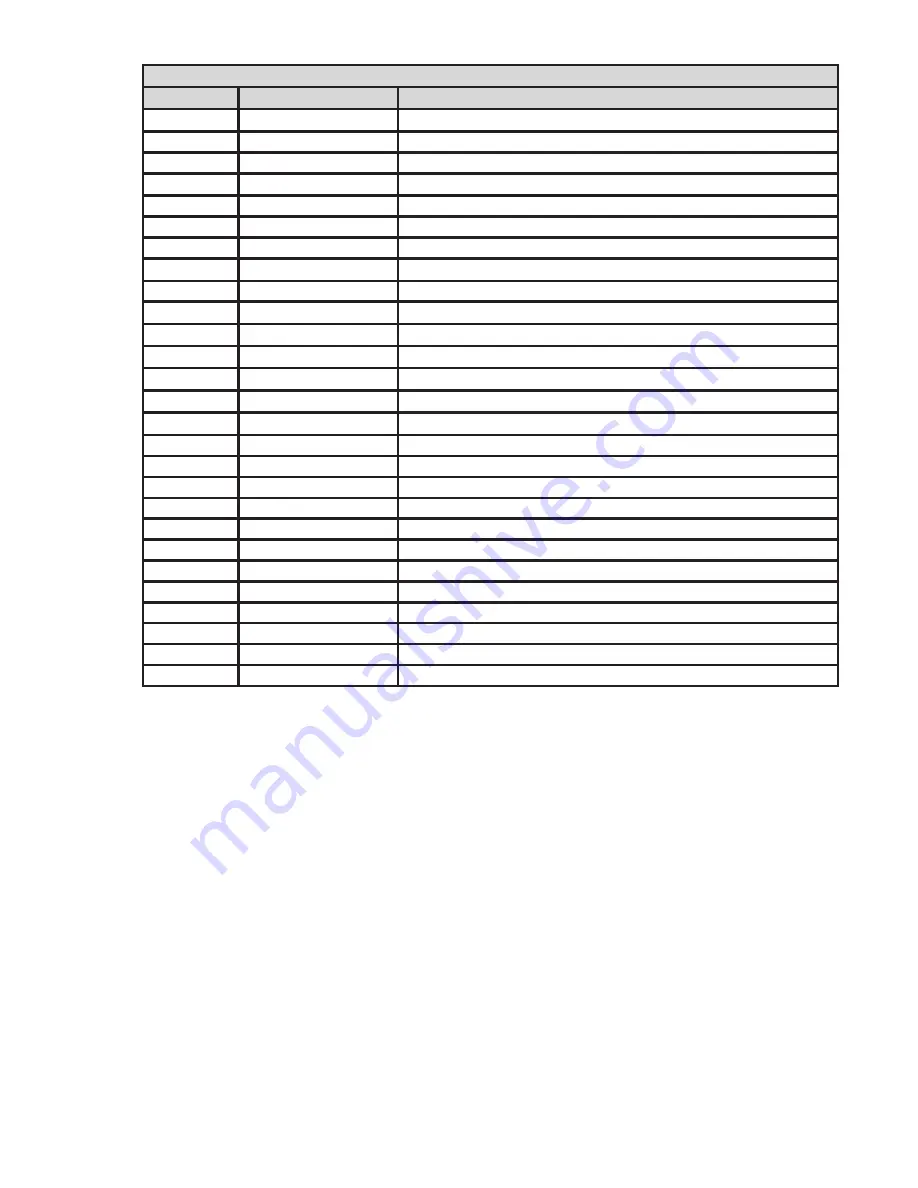
ET 201I AC/DC
0-5346
KEY SPARE PARTS
6-3
ET 220i AC/DC Spare Parts
Item
Part Number
Description
1
W7006300
Clear Control Panel Cover
2
W7006301
Gas Outlet, Front Panel
2
W7006301
Gas Inlet, Rear Panel
4
W7006500
Knob, Control
5
W7006323
PCB Secondary Rectifier
6
W7006433
PCB Control
7
W7006434
PCB Primary Inverter
8
W7006307
PCB, Display
9
W7006427
REL02
10
W7006326
Transformer, Inverter
11
W7006439
Switch, On/Off
12
W7006426
Rectifier, Bridge, Mains Supply
13
W7006314
Cable Assy, 8 Pin Remote
14
W7006431
Cable Assy, 4 Pin CAN
13
667.8377.0
Cable Assy, 14 Pin Remote
16
W7006315
Solenoid 24VDC
17
W7006316
Fan 12VDC
18
W7006317
Inductor HF
20
W7006319
IGBT
21
W7006740
Diode, Output
22
W7006425
HF Filter
23
W7006430
Panel Mount Dinse Socket 50mm
2
24
W6000000
Thermal Sensor
25
W7006441
Panel, Control (User Interface)
26
W7006429.
Panel, Front
27
W7006440
Panel, Rear
28
W7006428
Transformer, Control
Table 6-1: Spare Parts
Содержание ET 220i AC/DC
Страница 46: ...ET 220I AC DC INSTALLATION OPERATION AND SETUP Manual 0 5346 3 34 This Page Intentionally Blank...
Страница 68: ...ET 201I AC DC KEY SPARE PARTS 0 5346 6 2 6 01 Key Spare Parts A 12885_AB Figure 6 1 Spare Parts...
Страница 70: ...ET 201I AC DC KEY SPARE PARTS 0 5346 6 4 This Page Intentionally Blank...
Страница 73: ......