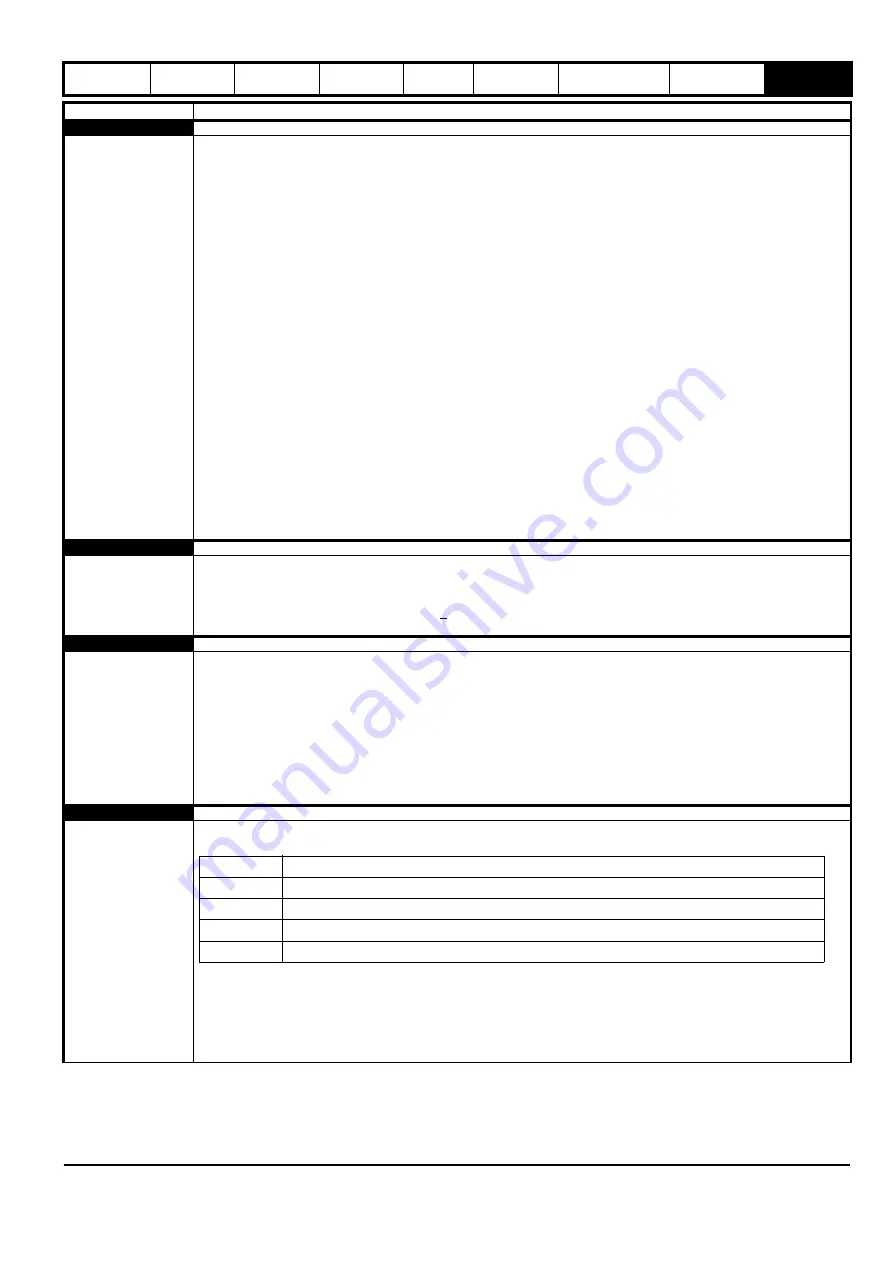
E300 Installation Guide
195
Issue Number: 1
Distance err
Excessive distance error
63
RFC-A
and
RFC-S
This trip indicates distance error is greater than the level defined in
Maximum Distance Error Threshold
(
H16
) resulting in
reduced control. The distance error detection is the integral of the difference between
Profile Speed
(
J39
) and
Actual
Speed
(
J40
) and active for closed loop operation only. The calculated distance error is compared to the user defined
distance error threshold in
Maximum Distance Error Threshold
(
H16
) and where this is exceeded a trip is generated.
The distance error during a travel is displayed in
Maximum Distance Error
(
J56
) independent of the activation of the
distance error detection. The distance error in
Maximum Distance Error
(
J56
) is reset to zero at the start of each travel.
Recommended actions:
•
Possible causes for the distance error trip can be due to the following
Motor
Check motor power connections
Check motor phase rotation
Check motor brake control
Check Elevator safety gear
Position feedback
Check position feedback mechanical mounting
Check position feedback phase rotation
Check position feedback wiring arrangement, risk of induced noise
Position feedback device failure, replace feedback device
Drive set-up
Check motor details and parameter set-up, including current limit
Check position feedback device parameter set-up
Check position feedback device phase offset, static autotune has been completed
Check speed control loop gain settings where motor instability exists
•
Increase the maximum distance error threshold in
Maximum Distance Error Threshold
(
H16
)
•
The distance error detection can be disabled by setting
Maximum Distance Error Threshold
(
H16
) = 0
Drive rating
Motor rated current exceeds allowable HD rating
61
The motor rated current set-up in
Motor Rated Current
(
B02
)
exceeds the limit for heavy duty operation resulting in reduced
/ limited overload capability when operating in the normal duty region.
Recommended actions:
•
Motor rated current should be reduced to < heavy duty rating
•
A larger drive should be used
Encoder 1
Drive position feedback interface power supply overload
189
The Encoder 1 trip indicates that the drive encoder power supply has been overloaded. Terminals 13, 14 of the 15 way D
type connector can supply a maximum current of 200 mA @ 15 V and 300 mA @ 8 V and 5 V.
Recommended actions:
•
Check encoder power supply connections to the drive
•
Check encoder specification, confirm it is compatible with the encoder power supply on the drive
•
Disable the termination resistors
Drive Encoder Termination Select
(
C05
) = Off 0)) to reduce current consumption
•
Use an external power supply with higher current capability to supply the encoder
•
For 5 V encoders with long cables, select 8 V (
Drive Encoder Voltage Select
(
C04
)) and install a 5 V voltage regulator
close to the encoder
•
Internal encoder fault, replace encoder
Encoder 2
Drive encoder feedback wire break detection
190
The Encoder 2 trip indicates that the drive has detected a wire break on the 15 way D type connector of the drive. The
exact cause of the trip can be identified from the sub-trip number.
Recommended actions:
•
Check correct encoder connections
•
Check the encoder cable shield connections, terminations, minimise length of any shield pigtails to connectors
•
Check encoder power supply is set-up correctly
Drive Encoder Voltage Select
(
C04
)
•
If wire break detection is not required, set
Drive Encoder Error Detection Level
(
C21
) = 0 to disable the Encoder 2 trip
•
Internal encoder fault, replace encoder
Trip
Diagnosis
Sub-trip
Reason
10
Drive position feedback interface on any input
11
Drive position feedback interface on the A channel
12
Drive position feedback interface on the B channel
13
Drive position feedback interface on the Z channel
Содержание E300 Series
Страница 211: ......
Страница 212: ...0479 0005 01 ...