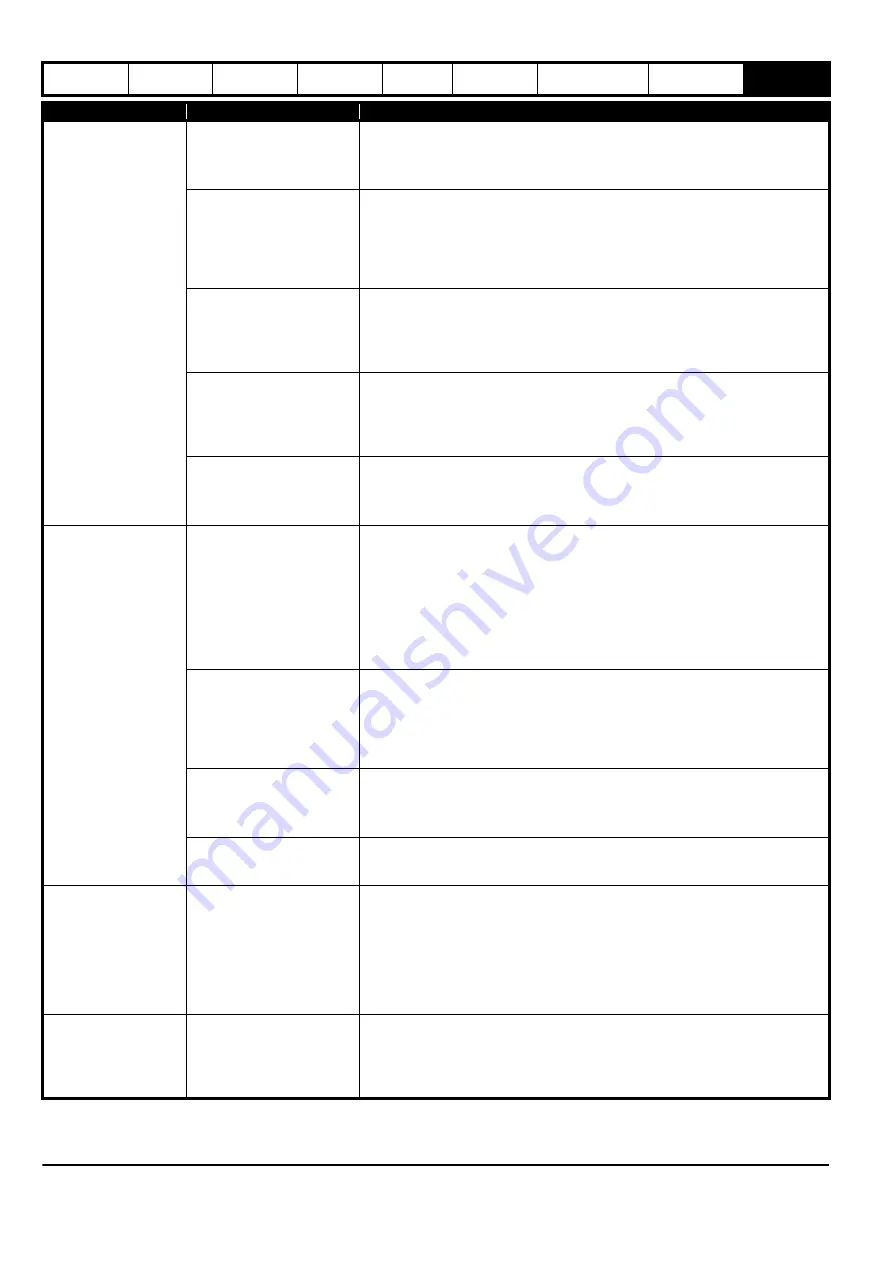
186
E300 Installation Guide
Issue Number: 1
Reported fault
Root cause
Recommended actions
Elevator incorrect
operating speed or
direction
Elevator mechanical data not
entered correctly
In order for correct operation at the systems rated speed, the mechanical data for the
Elevator system must be entered correctly, this includes the Nominal speed (m/s)
Sheave diameter, Roping, Gear ratio and Maximum speed.
•
Refer to
Menu E Mechanical
to enter the mechanical data
Elevator operating speeds not
set-up
The
E300 Advanced Elevator
drive in default set-up has 4 speed selections V1 through
to V4 which can be adjusted in parameters
G01
through to
G04.
Also ensure that the
correct control connections are made to the drives control terminals to select the
required speed.
•
Refer to
Menu G Profile
to set-up the operating speeds and
Menu F Hardware IO
for the control input configuration and monitoring
Incorrect direction input
configuration, selection
Where operation in an incorrect direction is identified, check that the correct direction
input control single or dual directions) has been set-up in
Control Input Mode
(
H11
) and
is being selected. Also check that the motor power and encoder connections are of the
correct rotation
•
Refer to
Menu F Hardware IO
for input direction control
Autotune has not been
completed for RFC-S mode
with a PM motor in a gearless
Elevator system
For PM motors and operation in RFC-S an encoder phase angle test must be
completed before operation. Failure to do an autotune will result in a loss of control and
on brake release the motor could move in either direction dependant upon the direction
of the load.
•
Refer to
Motor Autotune
(
B11
)
Motor power, encoder control
connections
Check both the motor power connections and the encoder control connections for the
correct rotation.
•
Refer to
Reverse Motor Phase Sequence
(
B26
) for the motor or
Drive Encoder
Feedback Reverse
(
C12
).
Elevator fails to reach
contract speed
Drive operating in current limit
If the motor is unable to reach the demanded speed check if the drive is operating in
current limit in
Current Limit Reached
(
L15
).
•
Check the motor parameters and symmetrical current limit are set-up correctly in
Menu B Motor
•
Check motor load in
Total Output Current
(
J22
)
•
Check for system mechanical issue, brake, safety gear, incorrect balance weights
•
Check drive size correct
•
Reduce acceleration, deceleration rates in
Menu G Profile
if issue is during
acceleration and/or deceleration
Motor rated speed “slip”
incorrect Open loop vector,
RFC-A)
The motor is unable to reach the demanded speed due to a limitation in output torque
as a result of the incorrect rated speed “slip”
•
Manually adjust the rated speed to achieve the maximum torque in
Torque
Producing Current (
J24
)
Open loop)
•
Tune the rated speed to achieve the maximum torque using
Motor Parameter
Adaptive Control
(
B25
) RFC-A)
Output motor voltage limited
If the motor is unable to reach the contract speed due to insufficient voltage available
from the AC power supply, consider any voltage drops due to any additional AC power
supply input choke or drive output choke to the motor.
•
Refer to
Output Voltage
and
Last Travel Maximum Output Voltage
(
J63
)
PM motor operating in RFC-S
reaching flux weakening
region
The motor may be operating at its maximum speed / going into flux weakening.
•
Refer to
Enable High Speed Mode
(
B28
) and ensure
Motor Rated Voltage
(
B03
) is
set to the maximum rated voltage for the motor
Overshoot during
change in speed
Speed control loop
Overshoot can occur during operation where there is a change in speed due to the
speed control loop proportional gain being to low. The speed control loop proportional
gain should be increased for the section, Start, Travel, Stop to minimise overshoot
under both full load and no load conditions
•
Refer to
Menu I Tuning
to adjust the speed loop P gain during the Start, Travel and
Stop.
•
Ensure good EMC practices are followed for the position feedback, induced noise
can limit the level of control loop gain which can be achieved.
Acoustic noise from
motor/ brake
arrangement during
start / stop
Current limit ramp time
During the stop and following brake apply the drive ramps the current limit down
releasing the load slowly onto the mechanical brake before disabling drive. If there is no
ramp or the ramp time is not correct some acoustic noise can be heard with some
motors and mechanical brakes.
•
Refer to
Motor Torque Ramp Time
(
D02
)
Содержание E300 Series
Страница 211: ......
Страница 212: ...0479 0005 01 ...