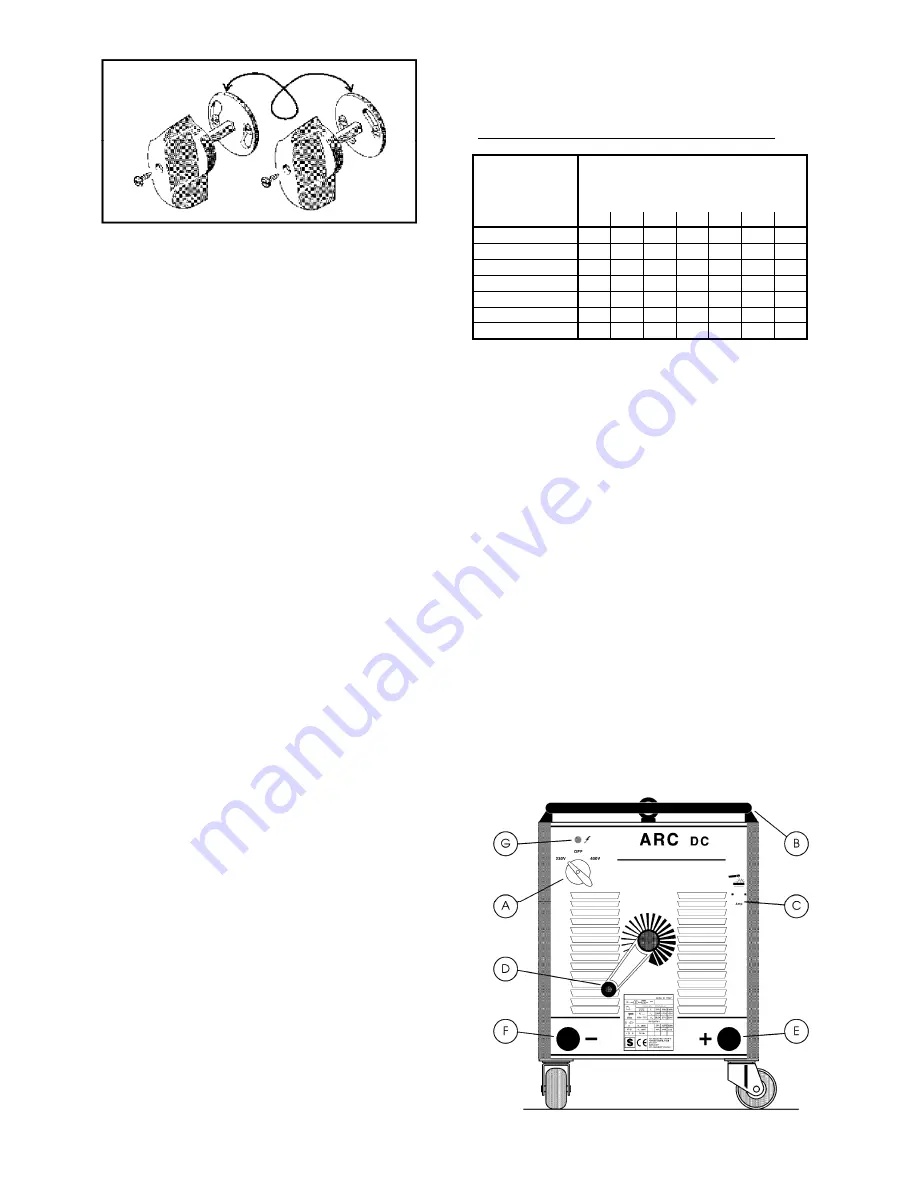
Connect supply cable : the yellow-green wire of cable
must be connected to an efficient earth point of the
system, the remaining wires should be connected to the
feed line through an isolation switch placed, if possible,
close to the working area so as to switch the unit off
quickly if necessary.
6
The magnetothermic switch capacity or of fuses in series
with switch should be equal or above the current
I
1
absorbed is known
by reading the
technical specifications
on the
unit i.e. feed voltage U
1
available.
Any extensions should have adequate sections for current
absorbed
I
1
.
2.3 OUTPUT CONNECTIONS
2.3.1 Connecting the electrode holder
•
The electrode holder must be connected to the machine
in compliance with the polarity indicated on the box of
electrodes that you are going to use.
•
When you connect the electrode holder cable and the
hearth cable, make sure that the power cable terminals
are well tightened.
•
The jaws of the electrode holder must be kept tightened
and the surfaces must be kept in good condition to ensure
good contact with the electrode rod.
•
Defective jaws will allow the electrodes to move which
will make welding difficult.
•
The connection between the electrode holder cable and
the electrode holder must be well tightened.
•
Use well insulated electrode holders.
•
Never touch the electrode holders of two different
welding machines at the same time.
•
Always avoid contact between parts of the body and the
electrode holder and/or the electrode.
2.3.2 Connecting the Earth Clamp
•
Make sure that the earth clamp makes good contact
with the workpiece.
•
Check that the earth cable is tightly fitted to earth clamp;
periodically check to make sure that this connection
remains well tightened.
A poorly tightened connection can cause current drops
during welding and also cause overheating of the earth
clamp and cable which can create the danger of burns.
•
The weld circuit must not be purposefully placed in
direct or indirect contact with the protection lead if not in
the workpiece.
•
If the workpiece is intentionally connected to the system
earth by means of a protection lead, the connection has to
be as direct as possible and done with a lead that has a
cross section at least equal to that of the welding current
return cable.
A second earth clamp, placed in the immediate vicinity,
can also be used.
2.3.3 Choosing the right welding cables
We recommend using the shortest possible welding
cables type H01 N2-D or H01 N2-E, in compliance with
CENELEC HD22.6 S1.
Too much resistance in the welding cables can reduce the
output available for the welding.
The performance of any arc welding machine depends,
generally, on the condition of the cables and the cable
connections.
CROSS SECTIONS OF WELDING CABLES IN mm
2
WELDING
CURRENT IN
AMPERE
DISTANCE IN METRES FROM THE
MACHINE
15
20 30 40 45
50
60
100
35
35 35 50 50
50
50
150
35
35 50 50 70
70
90
200
35
50 50 70 70
95
100
250
35
50 70 70 95
100 150
300
50
70 70 95 100 150 150
350
50
70 95 100
150 150 200
400
50
95 95 150
150 200 210
NOTE: The cross sections listed in the table are those for
each single conductor (electrode holder or ground clamp).
The cross sections listed in the table are those for each
single conductor (electrode holder or group clamp).
The cross sections of the cables can be obtained by
connecting in parallel 2 or 3 conductors having the same
cross section. For example :
150mm
2
=three 50mm
2
cables linked together in parallel.
200mm
2
=2x95 mm
2
cables or 3x70 mm
2
cables linked
together in parallel.
2.3.4 Connecting two welding machines in parallel
Two welding machines can be connected in parallel so that
one obtains on output current greater than the output
current of each single machine.
It is important that the positive pole of one machine is
connected to the positive pole of the other machine and
likewise that the negative pole of one machine is connected
to the negative pole of the other machine.
When making this connections it is important to abide by the
cross sections shown in the table.
After having connected two machines in parallel, set the
output current of each machine to the halfway point so that
each machine will produce half of its maximum output
current.
This is recommended in order to balance the heath
produced by each machine, thus allowing the operator to
make the best use of duty cycles of both machines.
3 PANELS DESCRIPTION
Содержание MMA 793
Страница 21: ...Artt Items 793 794 795 798 799 21...
Страница 23: ...Art 796 797 23...
Страница 25: ......
Страница 26: ...Cod 381656 10 2009...