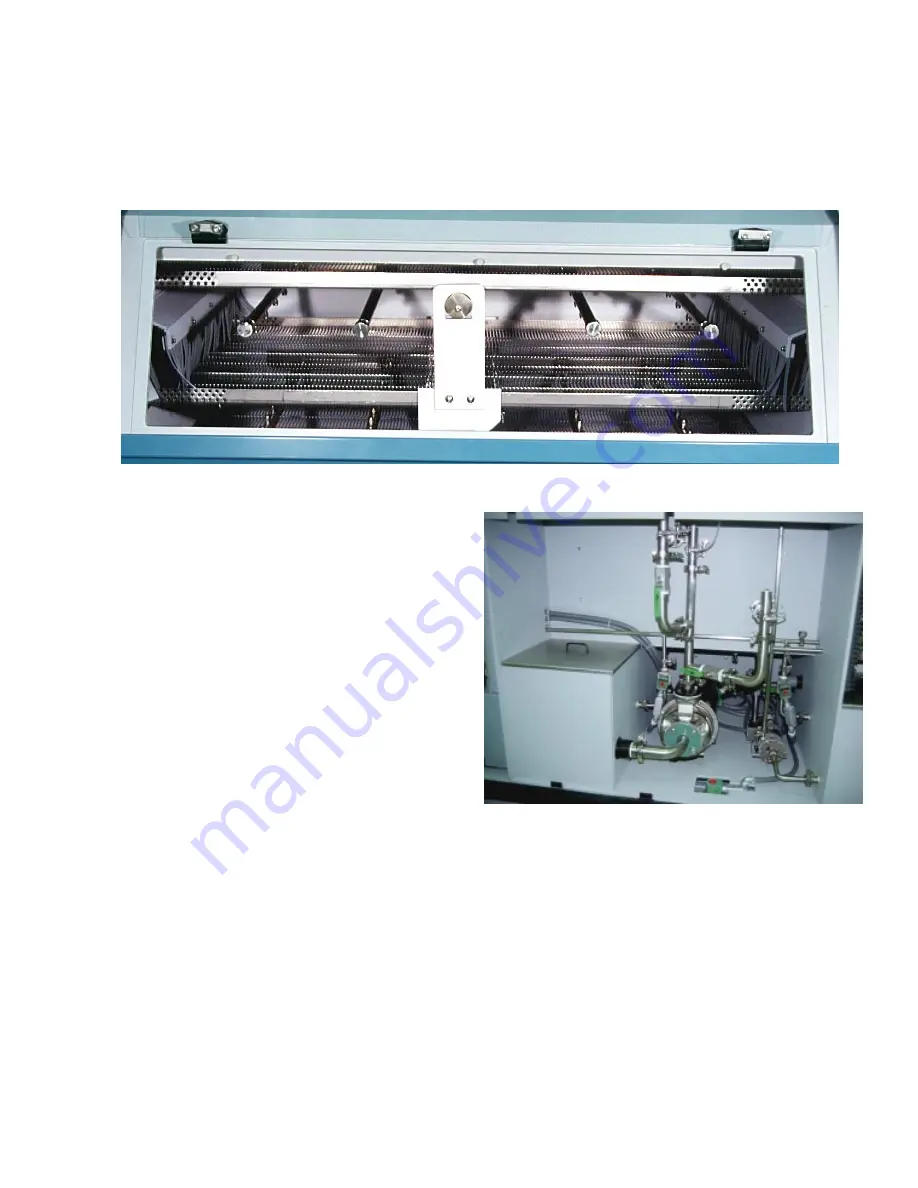
Aquastorm 200
Overview 1-9
Heated Recirculating Rinse/ Hurricane Section
The Recirculating Rinse section is 122 cm (48 inches) long consisting of four (4) upper spray manifolds and
four (4) lower spray manifolds, powered by a 5 HP pump (standard configuration). A 189 liter (50 gal.)
tank is standard with two (2) 16 kw immersion heaters.Temperatures are displayed via the LCD. The
computer continually monitors and corrects the temperature in the rinse tank by means of a thermocouple
device. If the temperature exceeds 82
o
C (180
o
F), the tank high temperature alarm indicator illuminates,
the audible alarm sounds and the tank heater shuts off.
An optional Hurricane Jet
TM
performance kit may
be configured to include a 10 HP pump in lieu
of the standard 5 HP pump. The Hurricane Jet
TM
manifold is configured between the standard four
(4) upper spray manifolds.
The water level in the rinse tank is monitored by
means of liquid level float switches. If the tank
fluid level falls below the low level float switch,
the tank heaters shut off and trip the tank level
alarm indicator on the front control panel along
with an audible alarm.
Tank filling is automatic via the fill solenoid,
activated by the low and/or operating liquid level
float switch(es) in the rinse tank. When the
system is initially activated and the tank is empty,
the fill solenoid activates to fill the system tanks.
During normal operation, if the water level falls
below normal operating level, the fill solenoid
activates to fill the tank.
The recirculating rinse tank is configured with a
cascade pipe to the recirculating wash tank. Flow
through the cascade pipe, from rinse to wash, is
controlled via a ball valve. O/A (Organic Acid)
or water soluble applications should be run with
the valve in the open position. Rosin or saponifier
applications should be run with the valve in the
closed position, not permitting cascading to occur.
If the system is configured with an on-board tank
for Enhanced Chemical Isolation (Level 3), a
cascade pipe from the recirculating rinse tank to
the Chemical Isolation tank is supplied as well.
The valve supplied on this cascade pipe should
remain closed for O/A applications. When
running saponifier processes, the ball valve on
the cascade pipe to the Chemical Isolation tank
should be open slightly. This is to prevent the
chemical isolation tank from loading up with
excess saponifier. The amount this valve is open
or closed is dependent upon the type of saponifer
as well as the product mix or product
configuration.
Содержание Aquastrom 200
Страница 26: ...Aquastorm 200 Overview 1 21 Optional Sump Pump 61 6 cm 24 in L x 42 5 cm 16 6 in W x 61 8 cm 24 in H ...
Страница 48: ......
Страница 142: ...Aquastorm 200 Maintenance 4 49 ...