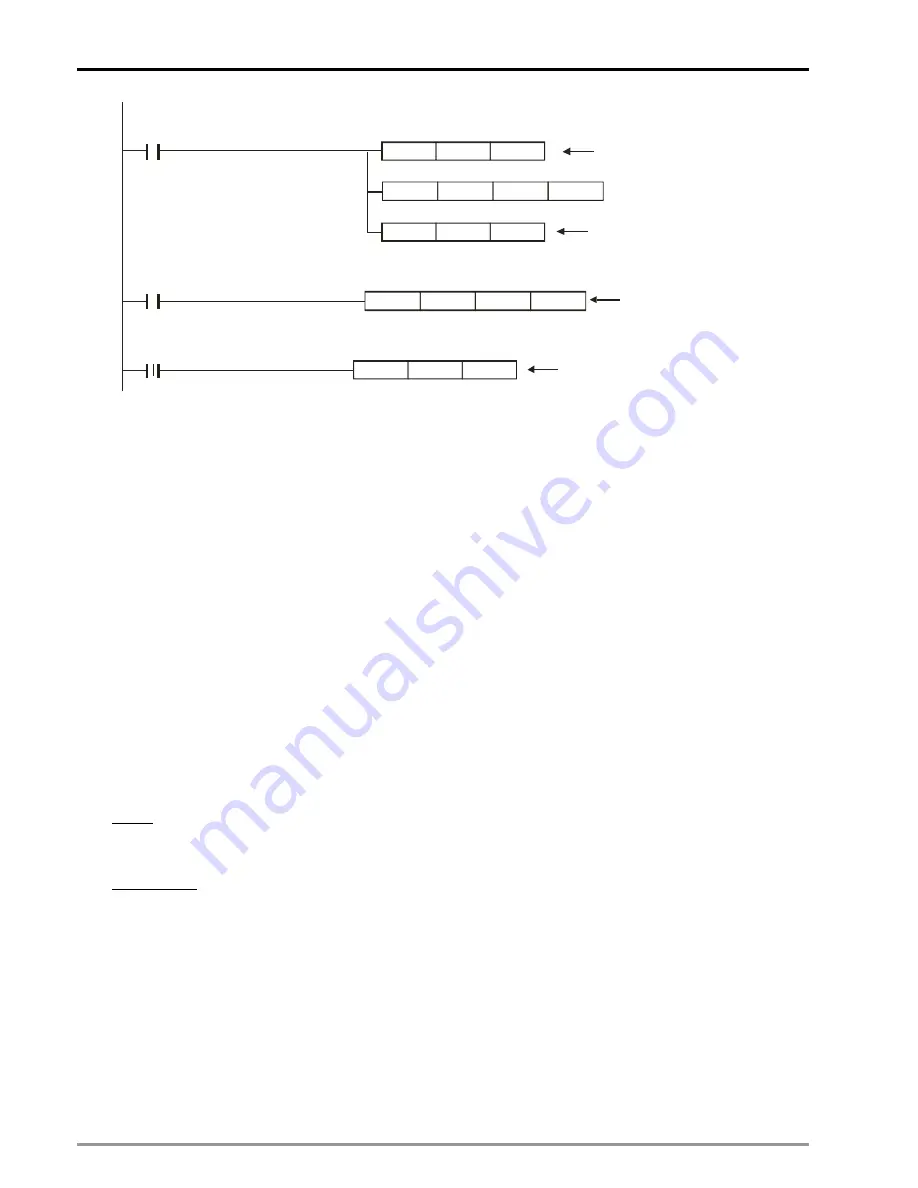
9
Electrical CAM
DVP-PM Application Manual
9-52
M4
DFLT
D138
D140
M4
M4
..
..
..
DEDIV
F2.0
D142
D140
DINT
D142
D144
DSUB
D126
D302
D144
DMOV
D126
D302
Convert the o ffset valu e int o
float ing poi nt value
D1 42=1 /2 D1 38
Users can decide an
off set ra tio
Backup t he actual
off set val ue
Ca lculate th e modifie d S lave
le ng th according t o t he a ctu al
off set val ue
W hen calcu la tion is fi nished,
move the le ngth of Sla ve
in to
D3 02
b ack
Po ints to no te:
1. Users can modi fy the o ffset ratio (0.5*D13 8
) a ccording to actu al need s
2. D1 32 h as to be applied i n D TO in st ructio n for cre at ing ro tary cu t E- CAM Data with o ffse t compen satio n
in th is e xample
Set up M4 t o ca lculate the actual offset value and the mo dif ied Sl ave le ngth
9.4.2.6 Flying
Saw
Application
–
Check cutter position
In flying saw application, it is important to check if the cutter is back in designated position when moving
back. If the cutter is not at designated position, it should remain current speed until limit switch is met,
otherwise the mechanical system might be damaged during the moving back process of cutter. M1757 can
be applied to remain current speed of Slave and continue operation until the limit. Users can compare the
designated position with Master position in current cycle to decide if M1757 needs to be enabled. Master
position in current cycle can be obtained by subtracting “Master position captured at the end of cycle” from
accumulated Master position (DD1862). Master position captured at end of cycle can be read out by using
DFROM instruction (D0 = K10005, Capture mode).
Application
Example
Set up:
Check if the cutter position is correct and automatically determine the execution of M1757.
Control Steps:
Step 1: Run the program and read the E-CAM status in capture mode by DFROM instruction. Read the data
in CR#10005 (Capture mode) of special module K100 to D300~D308 at the end of cycle.
Step 2: Substract the captured Master position (D306) from the
number of accumulated MPG input pulses
(D1862), and we can obtain the actual Master position in current cycle (D350).
Step 3: Compare the actual Master position (D350) with the target position (D1842). If the actual Master
position is bigger than the target position and the limit switch has not been triggered, execute M1757 then
stop the CAM operation.
Содержание DVP-10PM
Страница 1: ......
Страница 45: ...2 Hardware Specifications and Wiring DVP PM Application Manual 2 30 MEMO...
Страница 125: ...3 Functions of Devices in DVP PM DVP PM Application Manual 3 80 MEMO...
Страница 341: ...8 Application Examples DVP PM Application Manual 8 2 Trajectory 3 Trajectory 4...
Страница 427: ...9 Electrical CAM DVP PM Application Manual 9 74...
Страница 437: ...10 Encrypting User Program DVP PM Application Manual 10 10 MEMO...
Страница 458: ...11 G code Application DVP PM Application Manual 11 21 B O100 main program...
Страница 561: ...14 Appendix DVP PM Application Manual 14 4 MEMO...