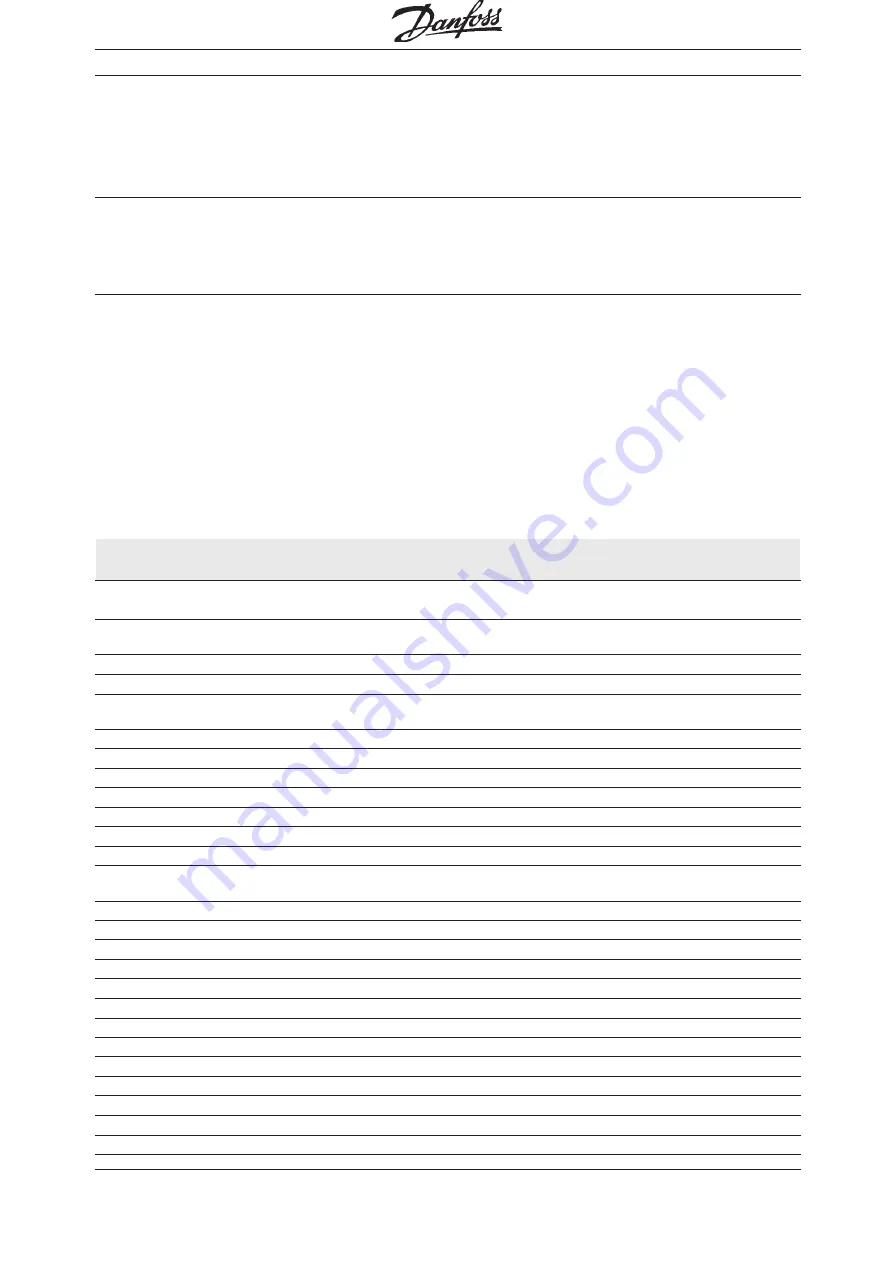
171
MG.10.J8.02 – VLT is a registered Danfoss trade mark
Programmable SyncPos motion controller
Parameter Code
Parameter Name
VLT- SyncPos
Par.
Unit
Factory
No. Par.No.
Group
setting
ACCMAXQC
Maximum acceleration
10
AXV
qc/ms
2
*
1/65536
BANDWIDTH
Bandwidth within which the
PID filter is active
706
35
AXR
%
1000
DFLTACC
Default acceleration
34
AXV
%
50
DFLTVEL
Default velocity
33
AXV
%
50
ENCODER
Encoder counts per revolution
2
AXE
counts/
500
revolution
ENCODERTYPE
Encoder type for encoder 0 (Slave)
27
AXE
–
0
ENDSWMOD
Behavior at limit switch
44
AXI
–
0
ERRCOND
Behavior after error
43
AXI
–
0
ESCCOND
Behavior after error
70
AXI
–
0
FFACC
Acceleration feed-forward
708
37
AXR
%
0
FFVEL
Velocity feed-forward
707
36
AXR
%
0
HOME_FORCE
Force HOME?
3
AXH
–
0
HOME_OFFSET
Zero point offset in relation to
machine zero point or index
42
AXH
qc
0
HOME_RAMP
Ramp for home motion
41
AXH
%
10
HOME_VEL
Velocity of home motion
7
AXH
%
10
HOMETYPE
Behavior during home motion
40
AXH
–
0
I_BREAK
Input for abort
105
GLI
–
0
I_CONTINUE
Continue program
106
GLI
–
0
I_ERRCLR
Clear error
107
GLI
–
0
I_NEGLIM ITSW
Negative limit switch
47
AXI
–
0
I_POSLIMITSW
Positive limit switch
46
AXI
–
0
I_PRGCHOICE
Input for beginning program choice
104
GLI
–
0
I_PRGSTART
Input for program start
103
GLI
–
0
I_REFSWITCH
Input for reference switch
45
AXI
–
0
KDER
Derivative value for PID control
703
12
AXR
–
1
KILIM
Limit value for integral sum for PID control
705
21
AXR
–
0
8
■
■
■
■
■
All SyncPos parameters in Alphabetical Order
For a better overview the parameters for the SyncPos program are divided into groups:
Global Parameters G L
The program language is prepared for multi axis applications. Therefore all parameters independent of an
axis such as the
Activated Program Number
Activated Program Number
Activated Program Number
Activated Program Number
Activated Program Number
PRGPAR (102) and the I/O parameters such as
clear error
clear error
clear error
clear error
clear error
I_ERRCLR (107) are combined in the group global parameters (GL).
Axis parameters AX...
This group contains all axis-specific parameters which can be processed with the GET and SET commands
and need axis information in the command:
AXE
Axis parameter encoder
AXV Axis parameter velocity (velocity and acceleration values)
AXI
Axis parameter I/O (I/O configuration)
AXH Axis parameter home (parameters affecting home motion)
AXR Axis parameter control (everything concerning control behavior) and
AXS Axis parameter synchronization
The column parameter group (AXV, AXR etc.) references to the dialog fields "CONTROLLER"
→
"PARAMETERS"
→
"AXIS", resp.
→
"GLOBAL", where you can define and change the parameters.
Parameter Reference