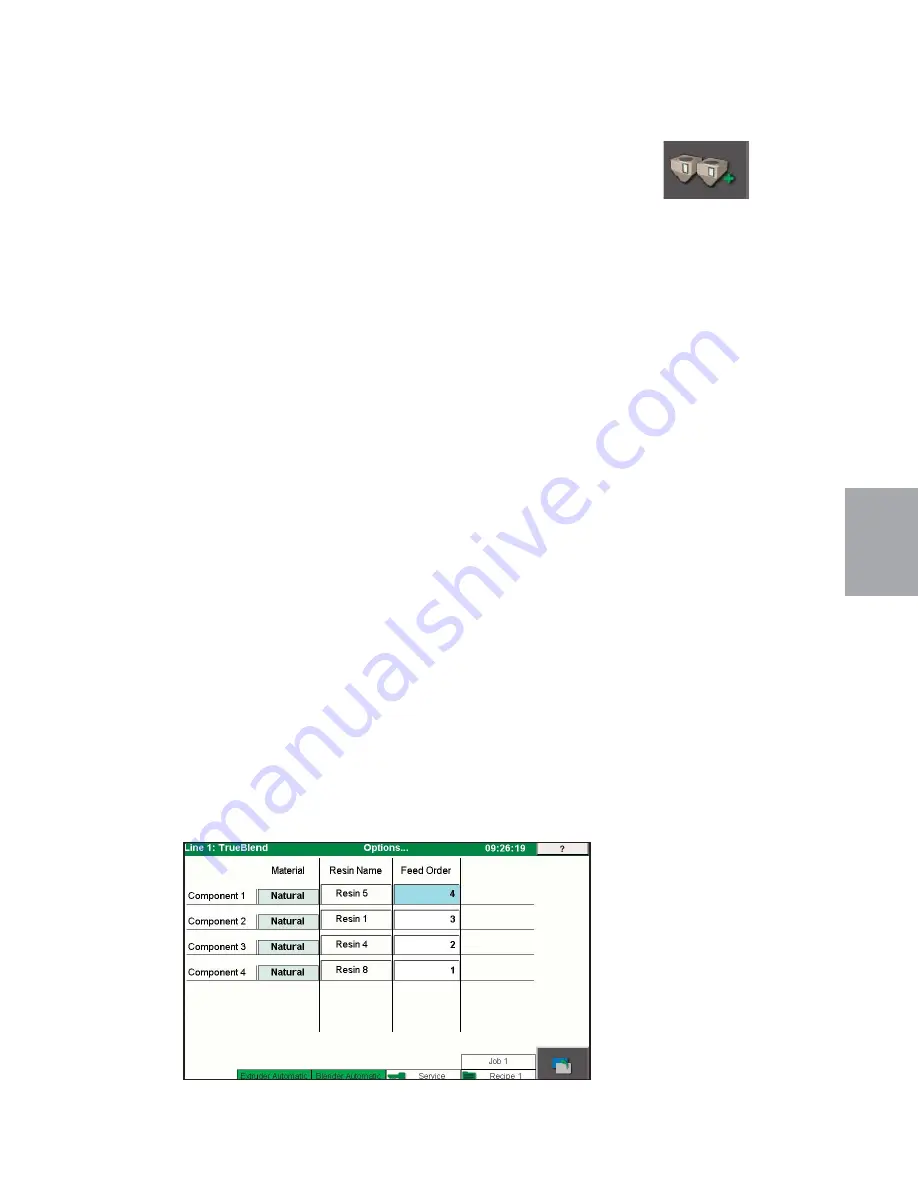
O p e r a t i o n l
4 - 3 5
4
Opera
tion
O p e r a t i n g S c r e e n s
( c o n t i n u e d )
For additional component hoppers, a [Previous/Next] button is available to view the addi-
tional components hoppers.
For each component hopper, there is a row of possible data entry values for the hopper.
Based on the configuration of the system, not all data entry fields may be present. Use the
[Previous/Next] button to show additional component hoppers.
•
Material Density:
If (Material Density in Recipe) is enabled, and (Resin Codes) are
disabled, this data entry field will be presented. For each component hopper, the oper-
ator can enter the material’s solid density value (g/cc).
•
Resin Codes:
If (Use Resin Names) is enabled, this data field will be presented. When
touched, a popup is presented where the operator can select the Resin that will be
available in the hopper. The system maintains a list of 255 resins which can be indi-
vidually defined. When a resin is selected from the list, the popup will be closed, and
the resin name will be displayed on the <Options> screen. The selected resin will now
also be shown on the main blender monitor screen in place of the material type field.
Note: When using Resin Codes, the resins solid density is defined and will be used if
needed.
•
Feed Order:
If (Feed Order in Recipe) is enabled, this data entry field is present. The
operator can enter the desired feed sequence. If the sequence is entered incorrectly, a
popup will notify the operator. The feed sequence must be correct before leaving this
screen. If the [Feed Order in Recipe] is set to (NO), the [Natural] feed sequence will
be automatically selected from the smallest to largest percentage; [Regrind] is always
fed first. If the [Feed Order in Recipe] is set to (YES), the feed sequence will be
selected according to the operator’s selection. The [Regrind] component will be forced
to feed first and the operator will select a unique feed sequence for the remaining
[Natural] components.
•
Dosing Rate (g/s):
When the blender is operating purely in volumetric mode of opera-
tion, this value will determine the amount of time the gate remains open in order to
process the recipe. This data is a gram per second value. In volumetric mode, the
batch hopper is not being weighed and there is no verification that the batch process-
ing is accurate. The system is purely relying on the dosing rate value to feed material.
If this value is incorrect, the mix will be wrong. In this mode, variations in bulk densi-
ty and flow rate are not accounted for.
(Continued)
Содержание TrueBlend SB-4
Страница 6: ...iv l Table of Contents...
Страница 38: ...3 10 l Installation...
Страница 134: ...4 96 l Operation...
Страница 160: ...6 10 l Troubleshooting...
Страница 165: ...Appendix l C 2 Hole Locations for Blow Off Kit...
Страница 168: ...D 3 l Appendix...