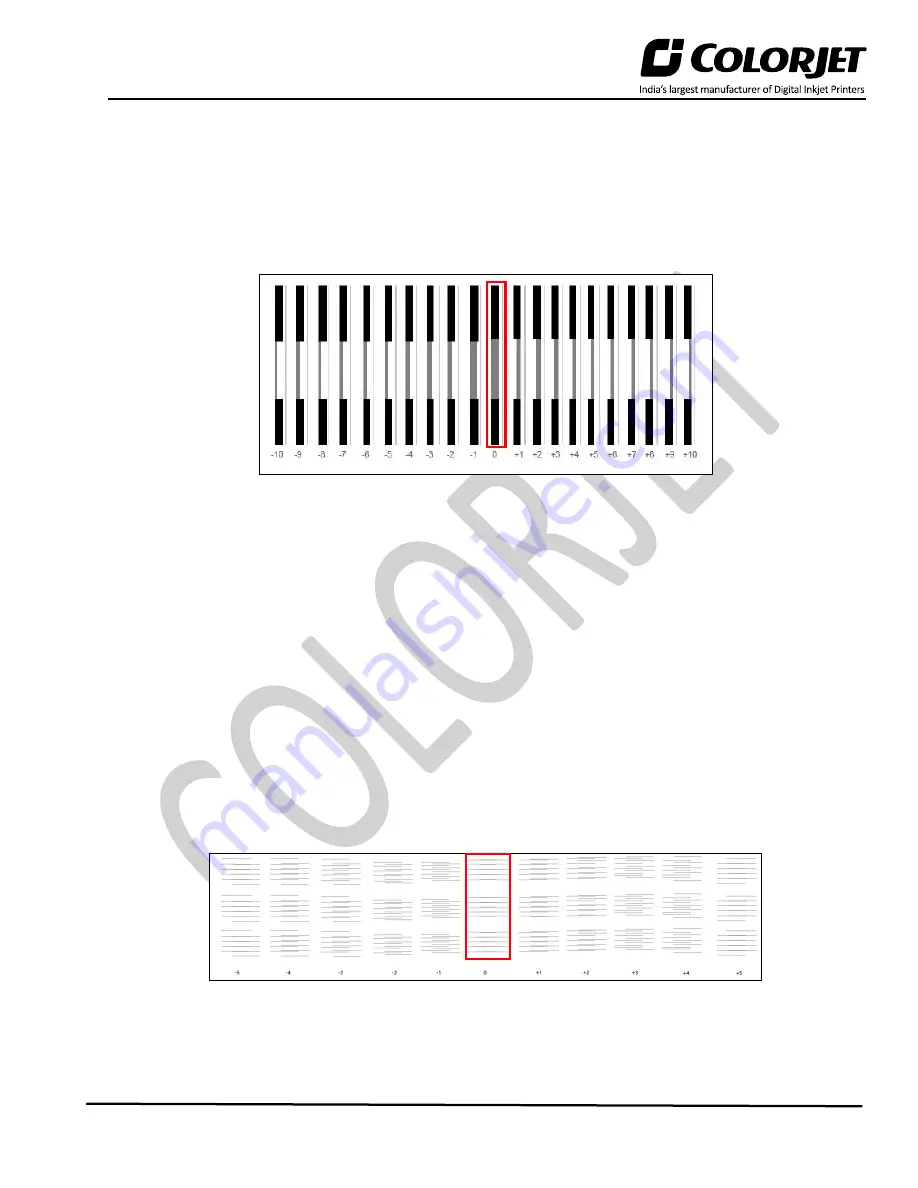
Page | 41
AuraJet Series II
Head Space Alignment
The Head Space alignment test checks the spacing between two heads of the machine. If two heads are not placed
horizontally correct, then they can hamper the printing quality. After getting the head space alignment result,
observe the printed patterns and select the best pattern from all the available. Enter the correction value in the
given field in the LCD control panel screen to align the head.
The Head Space Alignment test result is shown in the image below:
Fig 46: The Head Space Alignment Test Result
In the above figure, observe the head space test result carefully and try to find out at which position or value, the
pattern is aligned properly. This value is known as the correction value and feed it in the printer using the given
option from the LCD control panel. Now, the spacing gets corrected and heads are aligned properly.
Feed Adjustment
The Feed Adjust test is used for the printer step calibration that is performed to verify and correct the media
feeding. The printer prints a complete image in several passes. A pass is the horizontal carriage sweep
perpendicular to the media movement. After each pass, the printer moves the media forward for the next pass
and it (the next pass) should be in continuation with the previously printed pass. If there is any gapping or
overlapping situation then it will cause horizontal white or dark bands to appear in the print output. Thus, in this
situation, step size needs to be adjusted. The step size is affected by multiple factors like thickness and type of the
printing media etc. Feed Adjust should be used to fine adjust the step size.
The Feed Adjust test result is shown in the image below:
Fig 47: The Feed Adjust Test Result
To perform the Feed Adjust test, you should first select the media type for which the calibration has to be done.
Содержание AURAJET II Series
Страница 1: ......
Страница 18: ...Page 17 AuraJet Series II Step 17 Install the sublimation kit If applicable as shown below...
Страница 79: ......