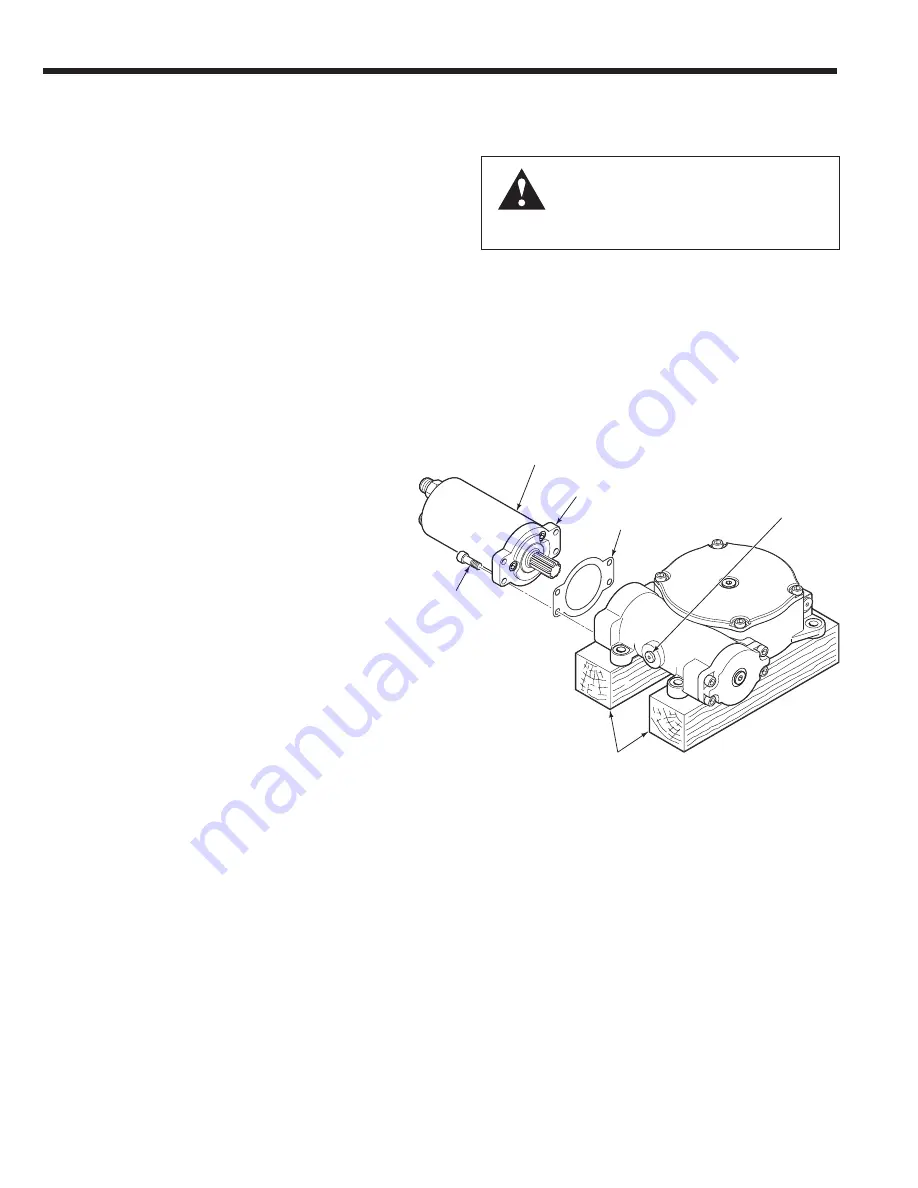
6921413
SERVICE
27
RR0577.eps
WARNING:
Before removing hydraulic
lines, relieve pressure in the hydraulic
system. Turn the truck off and open the
truck auxiliary control valves several times
in both directions.
5
4
3
Drive Motor
Motor Flange
Fill Plug
Flange Gasket
4.5-1
Drive Motor Removal and
Installation
1
Remove the attachment from the truck as described
in Section 4.1.
2
Remove the drive group from the attachment as
described in Section 4.3-1.
3
Remove the fill plug and drain the lubricant from the
drive group.
4
Lay the drive group, pinion down, on two 4 x 4 in.
(10 x 10 cm) wood blocks placed on both sides of the
pinion gear.
5
Remove the four capscrews fastening the motor flange
to the gearcase housing. Tap on the drive motor with
a rubber mallet to separate the drive motor assembly
from the gearcase.
6
For reassembly, reverse the above procedures except
as follows:
• Apply Loctite 242 (blue) to the threads of the four
flange capscrews. Install the drive motor/flange
assembly to the gearcase housing. Tighten the
capscrews to 9.5 ft.-lbs. (13 Nm).
• Fill gearcase until oil begins to run from end cover
port. Use Cascade Gear Lube Part No. 656300, or
SAE 90 wt. gear lube (AGMA 'mild' 6 EP Gear Lube).
4.5
Drive Motor
(1.2 ci motor)
Содержание 14J Series
Страница 2: ...BLANK...