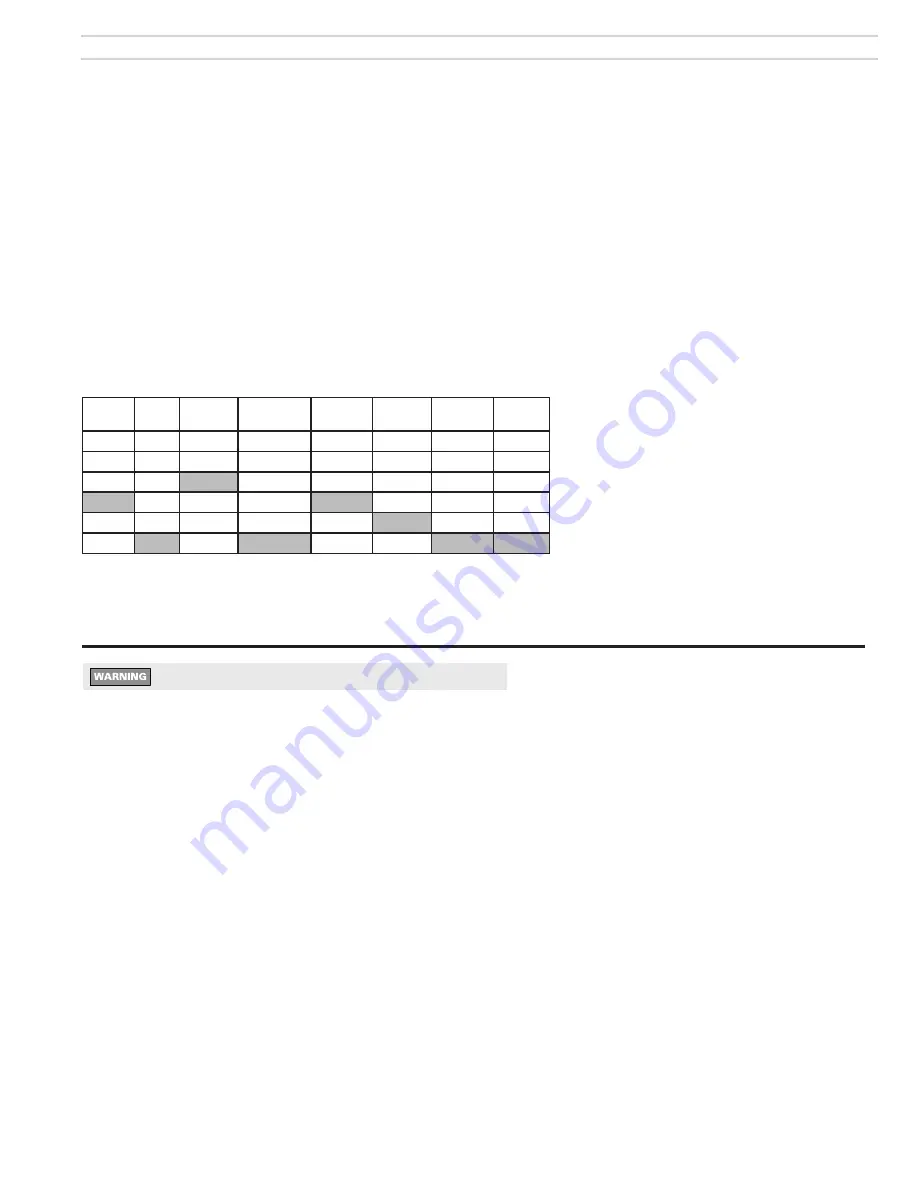
Model 601GAS burner — Instruction manual
MN601GAS 012516
– 17 –
Where appliance instructions differ from this manual, follow the appliance instructions.
4. Check System • Start-up Burner/Appliance
(continued)
Programming and Setup – 60200FR
Definitions:
Call for Heat (C.F.H.): TT on + Limit In on + BV on + CO on
Pre-Purge: Time period the motor is on prior to T.F.I.
Trial for Ignition: (T.F.I.): Burner Flame Establishing period
Post-Purge: Time period the motor is on after a Call for Heat has been satisfied
Post-Purge Interrupt: If selected is Time at which the 120 second Post-purge will be interrupted if a C.F.H. occurs during the Post-purge.
Allowed Recycles: Number of Recycles allowed during a single C.F.H. prior to lockout due to flame loss.
TT Used: Select “NO” when not using TT, select “YES” when using TT
Baseline Reset: Resets the baseline statistics used by the fault history
Factory Default: Resets ALL settings to the “Factory Defaults”
Do not start the burner if the combustion chamber contains gas.
Button Functions – 60200FR
Reset
1. Return to Standby from other operating states. Press for ½ second
2. Reset control from Lockout. Press for 1 second
3. Reset control from Latch-up. Press for 30 second
Display Control
ESC /
Display previous Operating State from Operating screen.
Exit Log or Setup screen to Operating screen with 3 second press.
Scroll through recent fault in Log screen.
Scroll to previous parameter in Setup screen.
Reject parameter change from Setup screen. Displays
Unchanged
on line 2 then after 2 sec, displays parameter with unchanged
value.
DN /
Display Time on line 2 of Operating screen.
Scroll down when in Log or Setup screen.
UP
/
Display Flame Rod – µAmps on line 2 of Operating screen.
Scroll up when in Log or Setup screen.
ENTR
/
Display status/fault messages on line 2 from Operating screen.
Move to less recent fault in Log screen.
Move to next parameter in Setup screen.
Accept parameter change from Setup screen. Displays
Entered
on
line 2 then after 2 sec, displays parameter with changed value.
UP
/
& ENTR
/
for 3 seconds
Enter Setup screen.
DN
/
& ENTR
/
for 3 seconds
Enter Fault History screen.
DN
/
&
UP
/
for 3 seconds
Enter Diagnostic screen to display Load Current sensed and Line
voltage.
Shaded box = default settings
*In seconds
†
MA code (“N” models) are non-recycling and will lock out on flame failure
Pre-
Purge*
T.F.I.*
Post-
Purge*
Post-Purge
Interrupt*
Allowed
Recycles
TT Used
Reset
Baseline
Factory
Default
120
60
90
30
30
15
3
10
6
10
60
1
Yes
Yes
Yes
0
4
0
Never
None
†
No
No
No