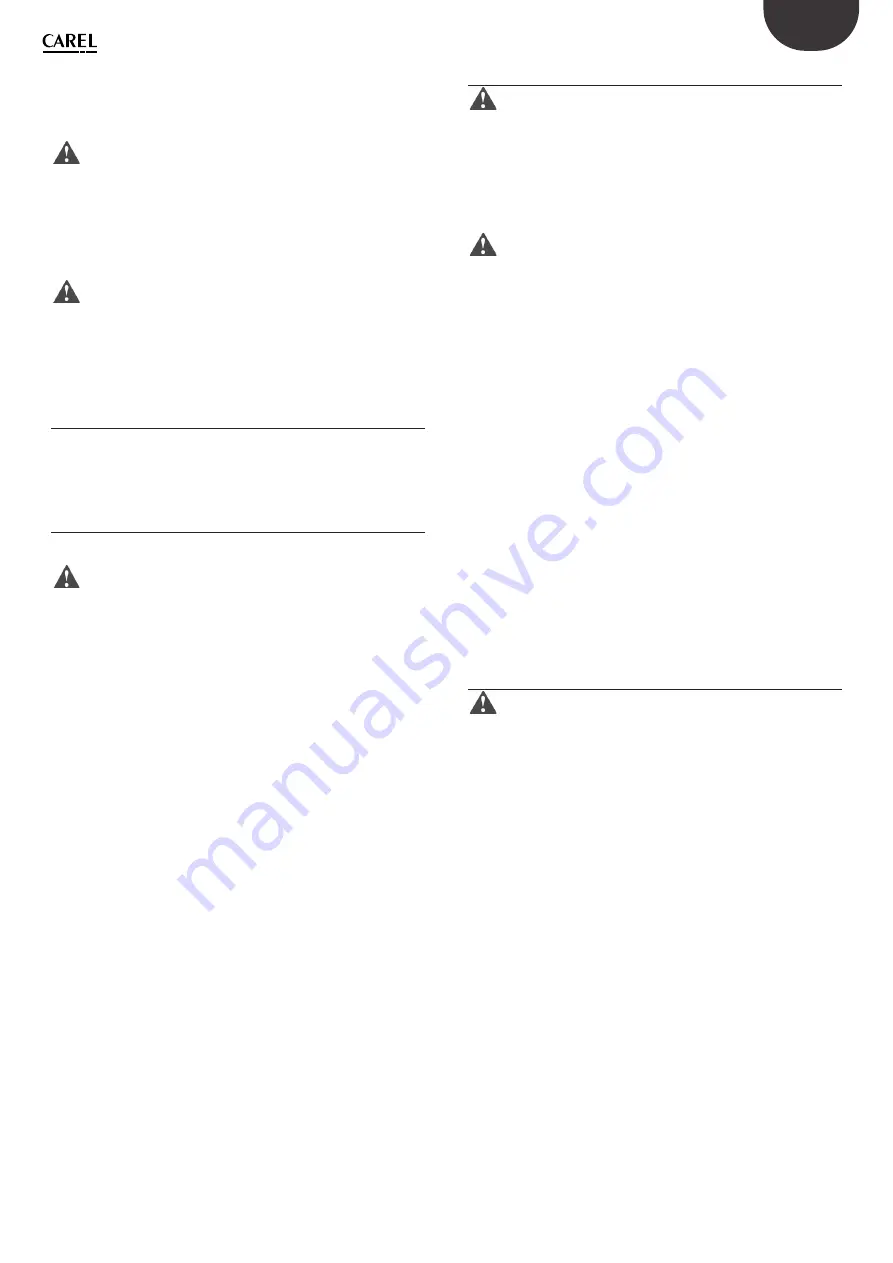
25
ENG
Heos BOX R704
+0300140EN - rel. 1.0 - 25.05.2022
If the system is functioning correctly, no bubbles are evident in the flow
indicator (Fifure 2.i, position 16) on the unit. Always make sure that the
colour of the sensitive loop inside the moisture indicator
is actually green
(no moisture present).
Caution
: the refrigerant charge must always be completed by
qualified personnel who have the qualifications and authorisations
required by local regulations, who are aware of the necessary precautions,
using appropriate personal protective equipment (PPE), and who are able
to correctly and safely complete all required operations.
Residual risk of pressurised parts yielding if the installer does not follow
the refrigerant gas charge instructions.
Caution
:
In the event where the box is out of service without power
connected for an extended period, it is recommended to manually open
the expansion valve so as to ensure continuity of the volume insider the
refrigerant circuit.
4.8 Oil top-up requirements
The Heos Box compressor is supplied filled with IDEMITSU DAPHNE PZ100S
(PAG VG100) oil. The oil level must only be topped up using the original oil,
or the following alternative:
FUCHS RENISO PAG 100
4.8.1 Single evaporator (SE)
The following instructions apply to both low temperature and medium
temperature applications.
Caution
: in SE mode, 5% of the total refrigerant oil charge must be
added to the circuit if:
• the R744 charge exceeds 2 kg;
• the suction line is more than 10 m long.
Example:
R744 charge = 2.5 kg Additional oil charge = 125 mg.
Proceed as follows to add oil:
1. Complete the charging procedure described in paragraph 4.6
2. Switch Heos Box off from APPLICA
3. Electrically disconnect HEOS BOX using the on/off switch on the unit
and the disconnect device upstream of the unit’s power supply line.
Then remove the refrigerant circuit cover panel.
4. Close the refrigerant inlet and outlet shut-off valves (Fig. 2.i, 18 and 21)
5. Carefully empty the system through the discharge pressure port (Fig.
2.i, 3)
6. Connect and switch on the vacuum pump at the discharge pressure
port (Fig. 2.i, 3)
7. Remove the plug from the suction line pressure port (Fig. 2.i, 22) and
add the amount of oil needed for the system, based on the CO2 charge
8. Reposition the plug and close the suction line pressure port (Fig. 2.i,
22)
9. Keep the vacuum pump on for no less than 30 minutes
10. Disconnect the pump and close the discharge pressure port (Fig. 2.i, 3)
11. Carefully open the refrigerant inlet and outlet shut-off valves (Fig. 2.i,
18 and 21)
4.8.2 Multi-evaporator (ME)
Caution
: in ME mode, oil needs to be added to the system.
For low temperature (LT) applications:
• Add an amount of oil equivalent to 10% of the mass of R744 in the
system
Example:
add 1 kg of oil for every 10 kg of CO2 charged in the circuit
• Also add extra oil equivalent to the volume of the traps in the system
(P-traps)
Caution
: for medium temperature (MT) applications:
• Add an amount of oil equivalent to 5% of the mass of R744 in the system
Example:
add 0.5kg of oil for every 10 kg of CO2 charged in the circuit
• Also add extra oil equivalent to the volume of the traps in the system
(P-traps)
Proceed as follows to add oil:
1. Complete the charging procedure described in paragraph 4.6
2. Switch Heos Box off from APPLICA
3. Electrically disconnect HEOS BOX using the on/off switch on the unit
and the disconnect device upstream of the unit’s power supply line.
Then remove the refrigerant circuit cover panel.
4. Close the refrigerant inlet and outlet shut-off valves (Fig. 2.i, 18 and 21)
5. Carefully empty the system through the discharge pressure port (Fig.
2.i, 3)
6. Connect and switch on the vacuum pump at the discharge pressure
port (Fig. 2.i, 3)
7. Remove the plug from the suction line pressure port (Fig. 2.i, 22) and
add the amount of oil needed for the system, based on the CO2 charge
8. Reposition the plug and close the suction line pressure port (Fig. 2.i,
22)
9. Keep the vacuum pump on for no less than 30 minutes
10. Disconnect the pump and close the discharge pressure port (3)
11. Carefully open the refrigerant inlet and outlet shut-off valves (Fig. 2.i,
18 and 21)
4.9.3 Superheat management requirements
Caution
: the superheat set point (SH) must be:
• <10K with 2-circuit evaporator
• <15K with 1-circuit evaporator
The superheat set point (SH) is the sum of the following SW parameters:
• SH set point;
• modulating SH set point.
The sum of these two parameters must be lower than the limit indicated
for one- and two-circuit evaporators.
(example, evaporator with 1 circuit: SHsetpoint = 7K , Modulating
SHsetpoint = 5K , ModulSHsetp. < 15K)
These values apply if a pressure transducer is installed on each evaporator
(better control of superheat)
A value of around 2K needs to be added to the above values if there is only
one pressure transducer installed inside the Heos Box
CAREL Industries S.p.A. recommends using the default superheat set
points configured in the system.
Содержание HB200C0300CE0
Страница 2: ......
Страница 4: ......
Страница 30: ...30 ENG Heos BOX R704 0300140EN rel 1 0 25 05 2022 Notes...
Страница 31: ......