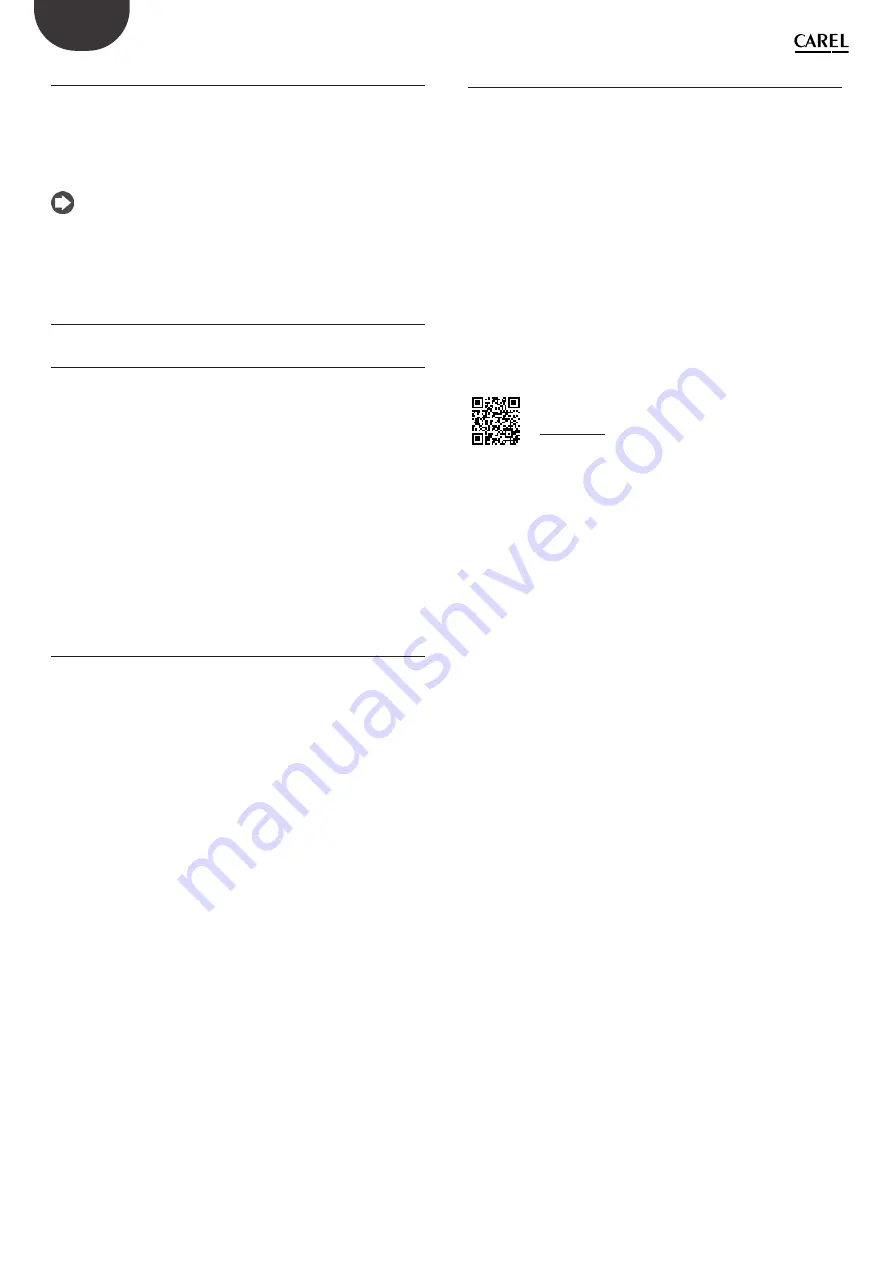
24
ENG
Heos BOX R704
+0300140EN - rel. 1.0 - 25.05.2022
4.9.2 Conformity to EMC directive
Heos Box is designed in compliance with the harmonised standards
of the EMC directive 2014/30/EU. Heos Box is a partly-completed
machine and as such must be appropriately incorporated into an
evaporator system; compliance with the EMC directive must therefore
be verified in the application, after final assembly. Contact Carel for
suggestions and guidelines.
Notice:
the length of the earth wire for the electronic controller
main power supply and digital output connections should be minimised,
using the earthing points provided inside the electrical panel (positions 41
and 42 in Figure 2.j) .
4.6 Kit installation
4.6.3 Anti-sweat heater kit
• Before opening the electrical panel, move disconnect switch QS1 to
OFF;
• Installation involves the DIN rail on the vertical panel in the electrical
panel (no. 65) and the electronic controller, and will require the use of a
flat-head screwdriver to press the spring terminals.
• Install the fuse carrier (marked FU4) and the SSR relay (marked KR1) and
the two pre-wired terminals on the DIN rail (no. 65), as shown in the
wiring diagram on page +QE&ETL/6;
• Wire the cables marked 01 and 04 to terminals 1 and 2 (as per the wiring
diagram);
• Wire the cables marked 201 and 200 to electronic controller terminal J10
(as shown in the wiring diagram);
• Complete the wiring by connecting the anti-sweat heater power cables
to terminals 3 and 4
• Close the electrical compartment and move the disconnect switch to
ON to restart the unit.
4.6.4 WiFi gateway kit
• Before opening the electrical panel, move disconnect switch QS1 to
OFF;
• The parts of the box to be worked on are the electronic controller and
the external interface (where all the electrical panel I/Os are located);
• Now connect the wires downstream of the kit, marked 08 and 09,
to terminal J25, as shown on page +QE&EFS/7 of the panel’s wiring
diagram, using a flat-head screwdriver to help lever the spring;
• When connecting the wires, make sure that the tip of the wire is fully
inserted in the opening provided on the terminal;
• Then install the WiFi gateway marked A2 on the holes provided on the
external panel interface (where all the electrical panel I/Os are located),
using the two screws provided together with the kit, in the space
designated as “WIFI optional” in Figure 2.j, position 61;
• Now run the two cables connected to gateway A2 through the cable
gland marked “Supervision” in Figure 2.j, position 51, then firmly tighten
the cable gland. All of the work to be done outside of the panel is now
complete;
• Proceed by wiring these two cables inside the panel. Connect the 3
wires marked 37-38-15 to terminal J14 on the controller, and the wires
marked 08 and 09 to terminal J25, as shown on page +QE&EFS/7 of the
panel’s wiring diagram, using a flat-head screwdriver to help lever the
spring;
• Close the electrical compartment and move the disconnect switch to
ON to restart the unit.
4.7 Refrigerant charging procedure
The HEOS BOX unit is designed to work only with R744 (CO2): only use
R744 certified refrigerant to charge the HEOS BOX unit.
The following points should be considered general indications for correctly
charging refrigerant into the unit, and are not technical specifications.
The expansion valves on the units must be correctly sized in order to
complete the charging operation successfully.
CAREL Industries S.p.A. may in this case, based on specific agreements, act
as a consultant for the design/installation/commissioning/use of the unit,
however in no case does it accept liability for incorrect operation of the
unit and the overall system if the warnings or suggestions provided in this
manual or in other product technical documents are not heeded.
In order to charge the unit (as described in the steps listed below), use
an interface (smartphone app or PC software) so as to monitor some
operating variables that are useful in the refrigerant charge process (such
as superheat).
For details on using the Carel Heos Box unit, see the manual
(+0300145EN).
The recommended sequence is as follows:
1. Electrically disconnect HEOS BOX using the on/off switch on the unit
and the disconnect device upstream of the unit’s power supply line.
Then remove the refrigerant circuit cover panel.
2. Check that the refrigerant inlet and outlet shut-off valves (18 and 21
in Fig. 2.i) are open
3. Using a vacuum pump, bring the system to a pressure of less than 0.25
mbars (187 μmHg), medium vacuum. The time the circuit is kept in a
vacuum must be evaluated on site, according to the volume of the
circuit and in any case must not be less than 60 minutes.
4. Prepare a system to weight the amount of refrigerant charged into the
unit, and write the value on the rating label affixed in this document
and to the HEOS BOX structure.
5. Charge the unit with a refrigerant pre-charge (e.g. 2 kg - 4.4 lbs) in
order to activate the control system and switch on the compressor.
6. Check that the electronic valve stators are installed correctly
7. Power on HEOS BOX using the on/off switch on the unit and the
disconnect device upstream of the unit’s power supply line.
8. Set the Heosbox unit to OFF
9. Set parameter CSM (max custom speed) to a value of 80 rps
10. Set the water-glycol inlet temperature to 15°C (with nominal flow-rate)
11. Set the HEOS BOX unit to ON and make sure that the compressor is
close to the maximum speed allowed (80 rps), while making sure that
the unit operates within the range stated in paragraph 2.6.2.
12. Make sure that the compressor remains running at the maximum
allowed speed (80 rps) for a few minutes (air control temperature close
to the set point; for a multi evaporator configuration, the air control
temperature must be close to the set point on each unit)
13. If the superheat is greater than the set point (SH > SHset) and the
expansion valve/valves are fully open (EEV%=100%), add refrigerant
(e.g. 100/200 g) (for a multi evaporator configuration, the superheat
on each evaporator must be monitored as described here). To check
the superheat set point, see the Carel Heos manual, as described
previously.
14. Wait a few minutes to let the system stabilise.
15. Repeat the previous two steps until SH=SHset and EEV%<70% (for
multi evaporator configurations this must be checked for each valve).
16. Check the refrigerant temperature in the section of piping leaving
the condenser and make sure that subcooling is between 0 and 4K
(optimum value 3K) (0<SBC<4K)
17. After having correctly charged the refrigerant, carefully check for leaks
using suitable instruments.
18. Reset parameter CSM (max custom speed) to the default value of 100 rps
Содержание HB200C0300CE0
Страница 2: ......
Страница 4: ......
Страница 30: ...30 ENG Heos BOX R704 0300140EN rel 1 0 25 05 2022 Notes...
Страница 31: ......