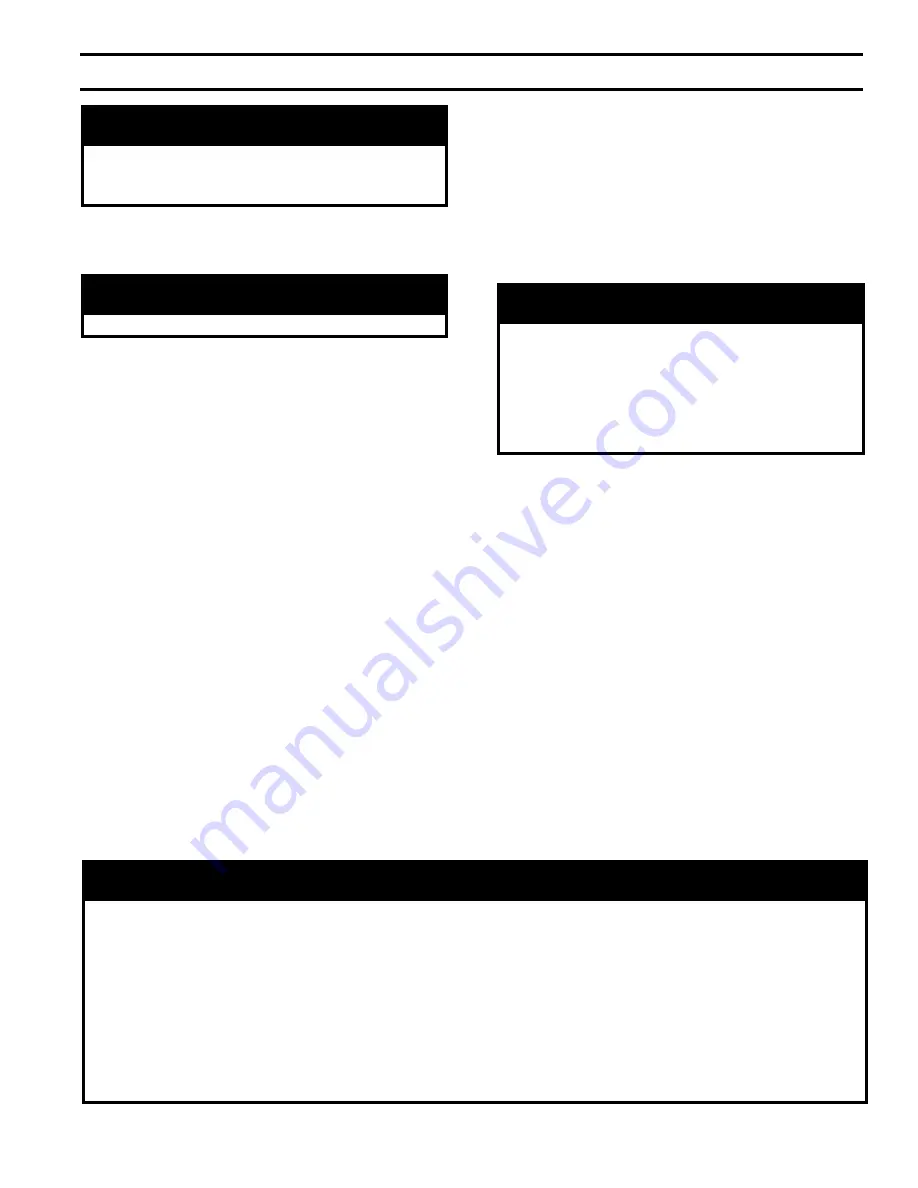
71
SECTION V – SERVICE (continued)
WARNiNG
Before returning boiler to service:
Follow this low water cut-off check out
procedure:
- Set thermostat to the highest setting.
- While boiler is operating, open drain valve
and
slowly
drain down boiler water.
cAUTiON
Do not drain water below gauge glass.
- Main burners should turn off when water
level drops below low water cut-off. At this
point the water level in gauge glass will just
be visible.
- Be sure that it is the low water cut-off
control and not the room thermostat,
pressure cut-out or other control that has
shut off the burners.
- Refill the boiler to the normal water level.
- Main burners should reignite.
- Clean out the boiler according to the
instructions for steam boilers on page 41.
- Reset controls for normal operation.
8.
FREQUENT WATER ADDITION
A leaky system will increase the volume of make-up
water supplied to the boiler which can significantly
shorten the life of the boiler. Entrained in make-up
water are dissolved minerals and oxygen. When the
fresh, cool make-up water is heated in the boiler the
minerals fall out as sediment and the oxygen escapes
as a gas. Both can result in reduced boiler life. The
accumulation of sediment can eventually isolate
the water from contacting the cast iron. When this
happens the cast iron in that area gets extremely hot
and eventually cracks. The presence of free oxygen
in the boiler creates a corrosive atmosphere which, if
iMPORTANT
If, during normal operation, it is necessary to add water to this boiler more frequently than once a month,
consult a qualified service technician to check your system for leaks. A leaky system will increase the volume
of make-up water supplied to the boiler which can significantly shorten a life of the boiler. entrained in make-
up water are dissolved minerals and oxygen. When the fresh, cool make-up water is heated in the boiler the
minerals fall out as sediment and the oxygen escapes as a gas. Both can result in reduced boiler life. The
accumulation of sediment can eventually isolate the water from contacting the cast iron. When this happens
the cast iron in that area gets extremely hot and eventually cracks. The presence of free oxygen in the boiler
creates a corrosive atmosphere which, if the concentration becomes high enough, can corrode the cast iron
through from the inside. Since neither of these failure types are the result of a casting defect the warranty
does not apply. Clearly it is in everyone’s best interest to prevent this type of failure. The maintenance of
system integrity is the best method to achieve this.
the concentration becomes high enough, can corrode
the cast iron through from the inside. Since neither of
these failure types are the result of a casting defect the
warranty does not apply. Clearly it is in everyone’s best
interest to prevent this type of failure. The maintenance
of system integrity is the best method to achieve this.
Refer to Minimum Water Quality Requirements chart
on Page 41.
9.
OXYGEN CORROSION:
WARNiNG
Oxygen contamination of the boiler water will cause
corrosion of iron and steel boiler components, and
can lead to boiler failure. Burnham Commercial's
standard warranty does not cover problems caused
by oxygen contamination of boiler water or scale
(lime) build-up caused by frequent addition of
water.
There are many possible causes of oxygen
contamination such as:
a. Addition of excessive make-up water as a result
of system leaks.
b. Absorption through open tanks and fittings.
c. Oxygen permeable materials in the distribution
system.
In order to ensure long product life, oxygen
sources should be eliminated. This can be
accomplished by taking the following measures:
a. Repairing system leaks to eliminate the need for
addition of make-up water.
b. Eliminating open tanks from the system.
c. Eliminating and/or repairing fittings which allow
oxygen absorption.
d. Use of non-permeable materials in the
distribution system.
e. Isolating the boiler from the system water by
installing a heat exchanger.
Содержание 5006B
Страница 10: ...10 Fig 6 ARRANGEMENT OF SECTIONS AND CANOPY S SECTION III INSTALLATION INSTRUCTIONS continued...
Страница 22: ...22 Fig 22 SECURING OF CANOPY DRAFTHOOD SECTION III INSTALLATION INSTRUCTIONS continued...
Страница 23: ...23 Fig 23 CANOPY DRAFTHOOD MOUNTING DIAGRAM SECTION III INSTALLATION INSTRUCTIONS continued...
Страница 29: ...29 Fig 28 MOUNTING ELEVATIONS OF M M 150 AND A 67M FLOAT LWCO SECTION III INSTALLATION INSTRUCTIONS continued...
Страница 51: ...51 Fig 46 wiring diagram 5006B THRU 5014B SECTION BOILERS OP CONTROL SYSTEM SECTION IV OPERATION continued...
Страница 53: ...53 Fig 47 wiring diagram 5015B THRU 5026B SECION BOILERS OP CONTROL SYSTEM SECTION IV OPERATION continued...
Страница 55: ...55 Fig 48 wiring diagram 5006B THRU 5014B SECTion BOILERS EP CONTROL SYSTEM SECTION IV OPERATION continued...
Страница 56: ...56 Fig 49 wiring diagram 5015B THRU 5026B SECTION BOILERS EP CONTROL SYSTEM SECTION IV OPERATION continued...
Страница 68: ...68 Fig 58 PILOT LOCATIONS SECTION V SERVICE continued...
Страница 72: ...72 SERVICE RECORD DATE SERVICE PERFORMED...
Страница 74: ...74 Fig 64 BASE PARTS 5006B Thru 5014B SECTION VI REPAIR PARTS continued...
Страница 76: ...76 Fig 65 BASE PARTS 5015B thru 5026B SECTION VI REPAIR PARTS continued...
Страница 78: ...78 Fig 66 INTEGRAL CANOPY DRAFTHOODS SECTIONS SECTION VI REPAIR PARTS continued...
Страница 82: ...82 Fig 67 JACKETS SECTION VI REPAIR PARTS continued...
Страница 102: ...102 Control assembly and mounting bracket OP EP CONTROL SYSTEMS SECTION VI REPAIR PARTS continued...
Страница 111: ...111 SERVICE RECORD DATE SERVICE PERFORMED...
Страница 112: ...112...