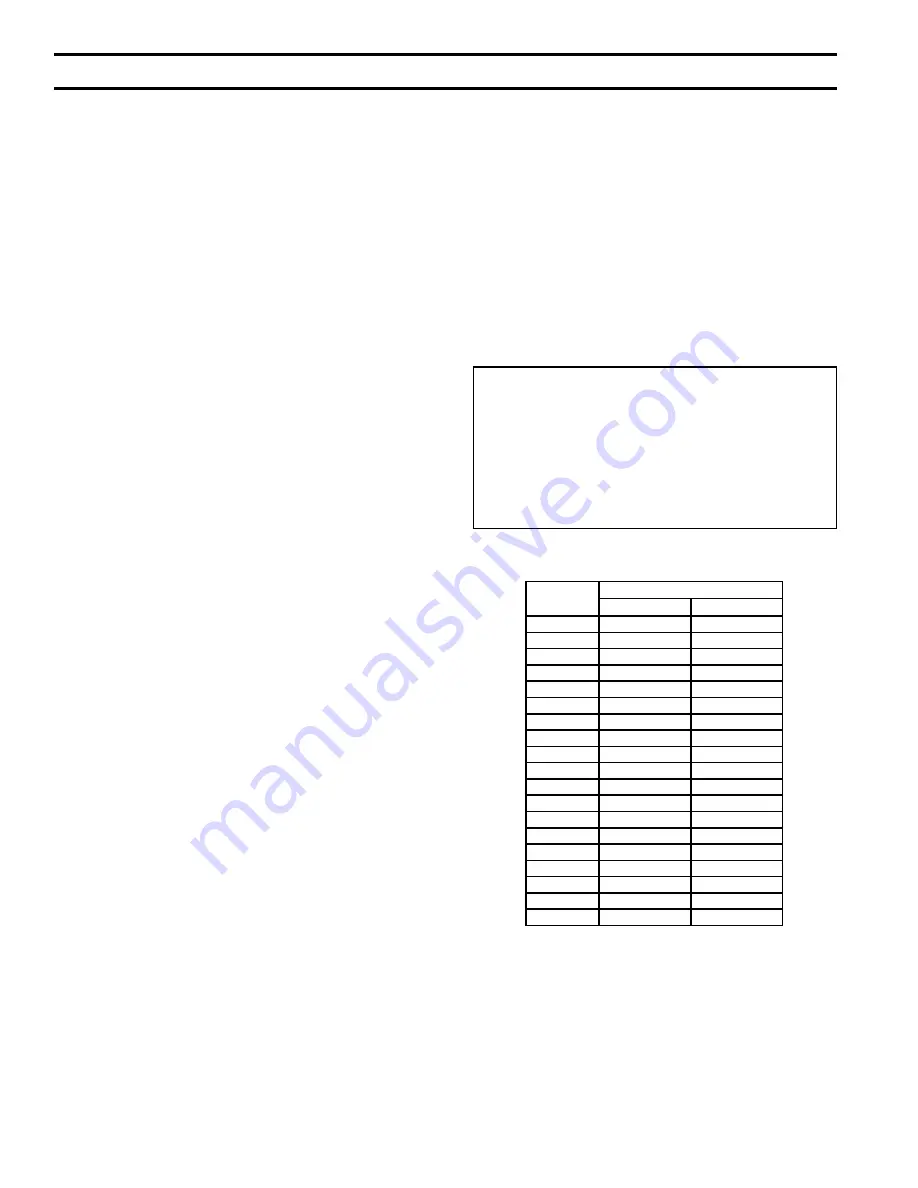
42
b. Draw about 5 gallons of hot water from
boiler into a container and dissolve into it the
appropriate amount of a recommended boilout
compound. Remove safety valve from boiler
and pour this solution into boiler, then reinstall
safety valve.
c. Turn on burner and keep operating while feeding
water to boiler slowly. This will raise water
level in boiler slowly into supply main and back
through return main, flowing from drain hose
at about 180ºF. Continue until water runs clear
from drain hose for at least 30 minutes.
d. Stop feeding water to boiler but continue
operating burner until excess water in boiler
flows out through supply main and water lowers
(by steaming) until it reaches normal level in
boiler.
Turn off burner. Drain boiler. Open all radiator
valves. Reinstall all supply main air valves.
Open gate valve in Hartford Loop.
e. When boiler has cooled down sufficiently
(crown-sheet of sections are not too hot to
touch), close the drain valves at boiler and in
return main and feed water slowly up to normal
level in boiler. Turn on burner and allow boiler
to steam for 10 minutes, then turn off burner.
Draw off one quart of water from bottom gauge
glass fitting and discard. Draw off another quart
sample and if this sample is not clear, repeat the
cycle of draining the boiler and return main and
refilling the boiler until sample is clear.
f. If the boiler water becomes dirty again at a later
date due to additional sediment loosened up in
the piping, close gate valve in Hartford Loop,
open drain valve in return main, turn on burner
and allow condensate to flow to drain until it has
run clear for at least 30 minutes while feeding
water to boiler so as to maintain normal water
level. Turn off burner, drain boiler, open gate
valve in Hartford Loop, then repeat step 1 above.
3. Make pH or Alkalinity Test
After boiler and system have been cleaned and
refilled as previously described, test the pH of
the water in the system. This can easily be done
by drawing a small sample of boiler water and
testing with Hydrion paper which is used in the
Boiler Size
Water Content (Gallons)
Water Boiler
Steam Boiler
5006B
37.6
25.6
5007B
43.4
29.3
5008B
49.1
33.0
5009B
54.9
36.8
5010B
60.6
40.5
5011B
66.4
44.2
5012B
72.1
47.9
5013B
77.9
51.6
5014B
83.7
55.4
5015B
89.4
59.1
5016B
95.2
62.8
5017B
100.9
66.5
5018B
106.7
70.2
5019B
112.5
73.9
5020B
118.2
77.7
5021B
124.0
81.4
5022B
129.7
85.1
5024B
141.2
92.5
5026B
152.8
100.0
TABle IV: WATer CONTeNT
SecTiON iV - OPeRATiON (continued)
Minimum Water Quality Requirements
pH - 8.3 - 10.5
TDS - 3500 ppm
Total alkalinity ppm as CaCO
3
- 1200
Total copper ppm - .05
Oily matter ppm -1
Total harness ppm -3
same manner as litmus paper, except that it gives
specific readings. A color chart on the side of
the small hydrion dispenser gives the reading in
pH. Hydrion paper is inexpensive and obtainable
from any chemical supply house or through your
local druggist. The pH should be in accordance
to “Minimum Water Quality Requirements” chart
below. Add some washout chemicals (caustic soda),
if necessary, to bring the pH within the specified
range. With this lower level of protection, care must
be exercised to eliminate all of the free oxygen in
the system.
4.
Boiler is now ready to be put into service.
Содержание 5006B
Страница 10: ...10 Fig 6 ARRANGEMENT OF SECTIONS AND CANOPY S SECTION III INSTALLATION INSTRUCTIONS continued...
Страница 22: ...22 Fig 22 SECURING OF CANOPY DRAFTHOOD SECTION III INSTALLATION INSTRUCTIONS continued...
Страница 23: ...23 Fig 23 CANOPY DRAFTHOOD MOUNTING DIAGRAM SECTION III INSTALLATION INSTRUCTIONS continued...
Страница 29: ...29 Fig 28 MOUNTING ELEVATIONS OF M M 150 AND A 67M FLOAT LWCO SECTION III INSTALLATION INSTRUCTIONS continued...
Страница 51: ...51 Fig 46 wiring diagram 5006B THRU 5014B SECTION BOILERS OP CONTROL SYSTEM SECTION IV OPERATION continued...
Страница 53: ...53 Fig 47 wiring diagram 5015B THRU 5026B SECION BOILERS OP CONTROL SYSTEM SECTION IV OPERATION continued...
Страница 55: ...55 Fig 48 wiring diagram 5006B THRU 5014B SECTion BOILERS EP CONTROL SYSTEM SECTION IV OPERATION continued...
Страница 56: ...56 Fig 49 wiring diagram 5015B THRU 5026B SECTION BOILERS EP CONTROL SYSTEM SECTION IV OPERATION continued...
Страница 68: ...68 Fig 58 PILOT LOCATIONS SECTION V SERVICE continued...
Страница 72: ...72 SERVICE RECORD DATE SERVICE PERFORMED...
Страница 74: ...74 Fig 64 BASE PARTS 5006B Thru 5014B SECTION VI REPAIR PARTS continued...
Страница 76: ...76 Fig 65 BASE PARTS 5015B thru 5026B SECTION VI REPAIR PARTS continued...
Страница 78: ...78 Fig 66 INTEGRAL CANOPY DRAFTHOODS SECTIONS SECTION VI REPAIR PARTS continued...
Страница 82: ...82 Fig 67 JACKETS SECTION VI REPAIR PARTS continued...
Страница 102: ...102 Control assembly and mounting bracket OP EP CONTROL SYSTEMS SECTION VI REPAIR PARTS continued...
Страница 111: ...111 SERVICE RECORD DATE SERVICE PERFORMED...
Страница 112: ...112...