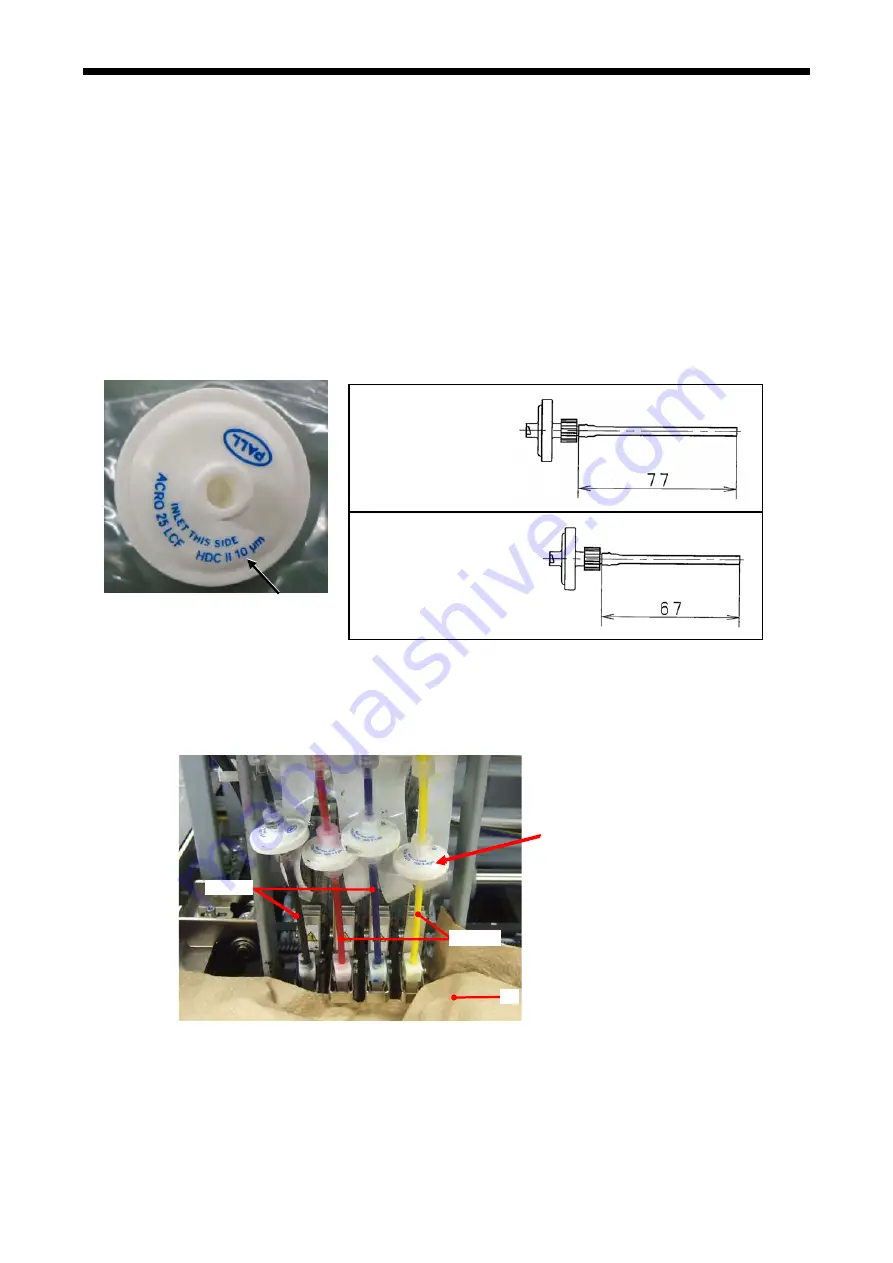
6. Replacing Parts
6-1-33. Replacing the Filter on the Print Head
Replace the Filter before replacing the Print Head when you find a large number of missing nozzles in
printing; the print is getting lost in printing Solid test pattern and there may be clogged ink covering the F/E
Filter inside the Print Head (see “4-1-2. Heavy misfiring in printing (Checking the Cracks in the Tube”).
6-1-33-1. Replacing the Filter for CMYK
Confirm that the firmware should be ver. 2.10 or higher.
<Note>
Be sure to wear the gloves in operation to keep pretreatment from the skin, as well as to prevent the ink
contamination with dust and oil in the Tubes.
<Requirements>
Some soft and clean cloths (several sheets)
220
GT-3 Series
<black /cyan>
<magenta/yellow>
1.
Turn OFF the printer, and open the Front Cover with both hands until it is locked with the stopper.
2.
Put on the gloves. Cover the Print Heads and the Carriage with a soft and clean cloth (1) so that the ink
may not make them dirty as well as some parts may not drop inside the printer.
The printed surface on the top
67 mm
77 mm
(1)
10
μ
m
Содержание GT-3 Series
Страница 38: ...2 Setting up GT 3 Series 3 Select LocalArea Connection 4 Click the Properties Button GT 3 Series 29 ...
Страница 130: ...6 Replacing Parts Bottom Parts of the Covers 0182Y 0183Y GT 3 Series 121 ...
Страница 375: ...SERVICE MANUAL 2013 Brother Industries Ltd All Rights Reserved GT 3 Series I3010990Z 2013 03 0 ...