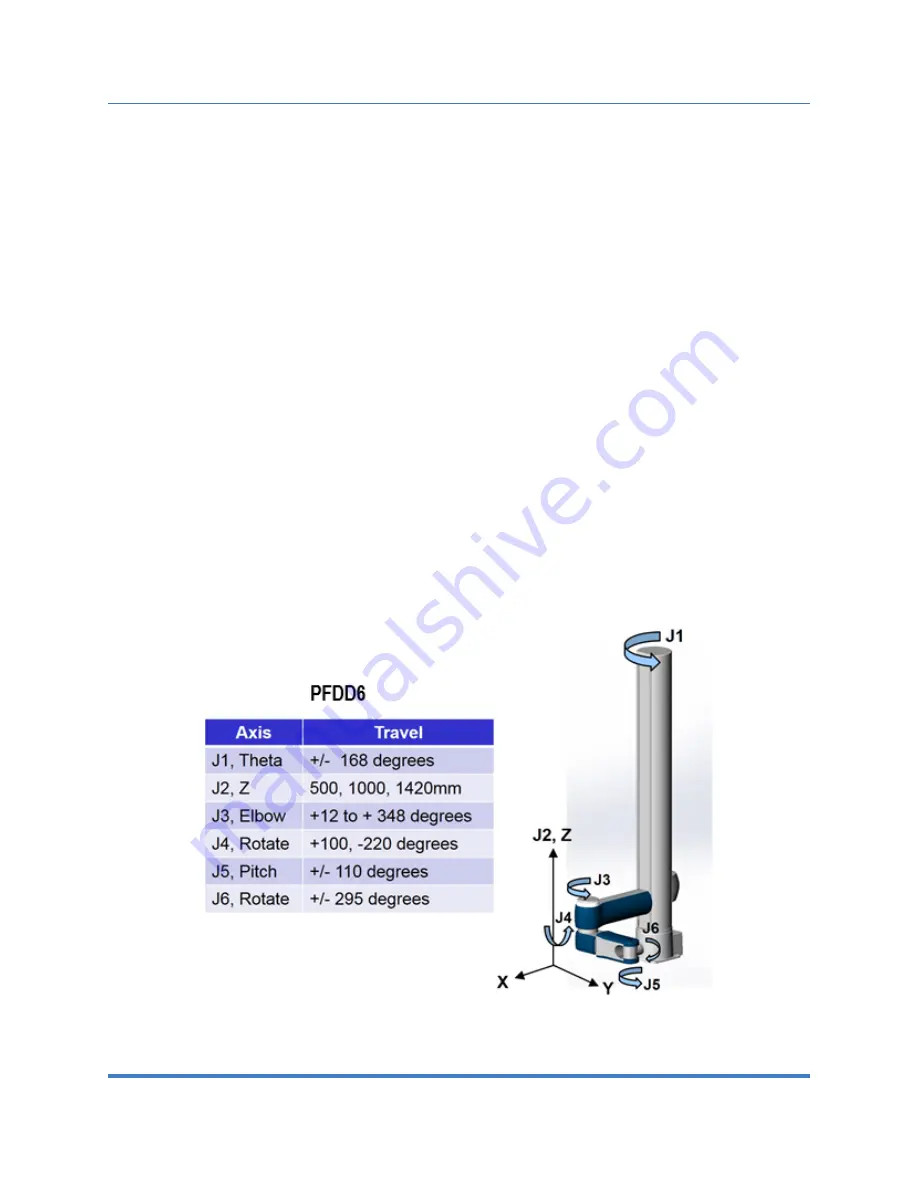
Introduction to the Hardware
PreciseFlex™ DDR Collaborative Robots
P/N: PFD0-DI-00010, Rev 5.0.0, April 9, 2022
12
Copyright © 2022, Brooks Automation, Inc.
8 for the PFDD6 and value 6 for the PFDD4. The tool mass, in kg, must be set in parameter 16067 value
8 for the PFDD6 and value 6 for the PFDD4, in order for the Dynamic Feed Forward to work properly.
Note that when setting the payload and gripper payload offset parameters in the database, these values
must be entered, saved to flash, and the controller must be re-booted for them to take effect.
See the software documentation about Parameters 16051, 16071, 16067, 16068, and the “
Robot.Tool”
and “
Robot.Payload”
properties for more a more detailed explanation.
These robots have 12 inputs and 8 outputs available at the base connector panel in a 25 pin D-
subminiature connector and have 2 digital outputs and up to 3 digital inputs available in the outer link
when the pneumatic version is ordered. A belt encoder input is available on the connector panel.
These robots are nominally quoted and shipped with a standard ISO flange, and a single solenoid valve
mounted in the outer link for users to add pneumatic or vacuum grippers of their design. Optionally, an
additional solenoid can be ordered, or a 23N squeeze, 60mm travel electric gripper can be ordered. See
the “system dimensions” section for reference dimensions on these options.
System Diagram and Coordinate Systems
The major elements of the PFDD Direct Drive robots and the orientation and origin of their World
Cartesian coordinate systems are shown in the diagrams below.