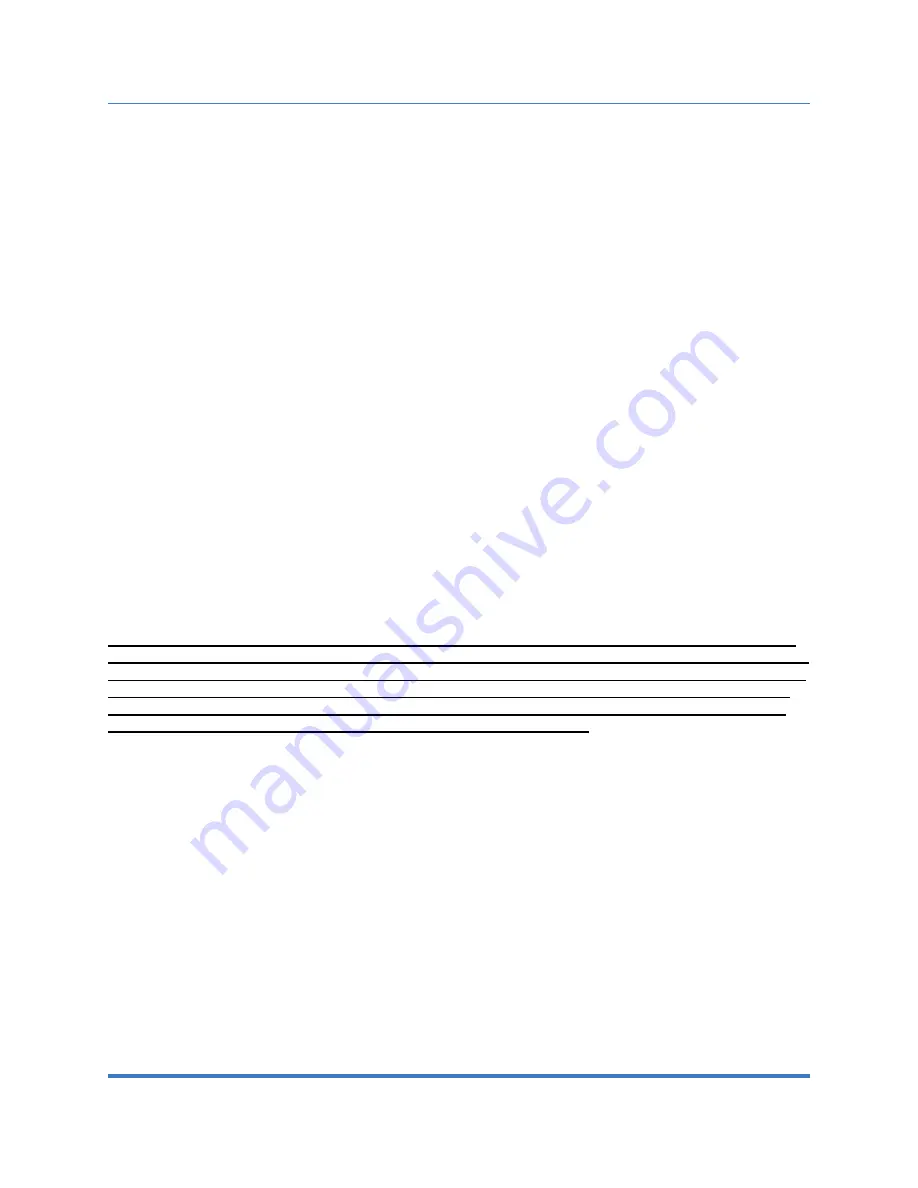
Brooks Automation
P/N: PFD0-DI-00010, Rev 5.0.0, April 9, 2022
Introduction to the Hardware
Copyright © 2022, Brooks Automation, Inc.
10
Introduction to the Hardware
System Overview
System Description
The PFDD Direct Drive Robots are available in either a four-axis or six-axis configuration. Both robots
include embedded motion controllers, a 48VDC motor power supply, and a 24VDC logic power supply
located inside the robot. In addition, they may optionally include an electric gripper and electric gripper
controller, or solenoid valves to support pneumatic grippers.
The Z axis of these robots is available with a standard travel of 500 mm, and optional travels of 1000mm
and 1420mm. The 6-axis robot can carry a payload of up to 5kg and the 4-axis robot can carry a payload
up to 7.0kg. These robots are extremely quiet and smooth, very reliable, and have excellent positioning
repeatability. To achieve these results, the axes are powered by brushless DC motors with absolute
encoders. With these characteristics, these robots are ideal for automating applications in the Life
Sciences, Medical Products, Semiconductor, Automotive, and Electronics industries.
In general, assuming a collaborative gripper with no sharp edges or other dangerous features, is
attached to the robot, these robots can make horizontal motions at tip speeds up to 1.5 -2.0 m/sec,
and bump into a person without causing a severe injury. For vertical motions, the Z speed should
be limited to 150mm/sec when the robot comes within 100mm of a rigid surface, as the effective
moving mass in Z is much greater than the effective moving mass in the horizontal plane. More
detail is provided in the Collaborative Robot section of this manual.
A number of communications and hardware interfaces are provided with the basic robot. These include
an RS-232 serial interface, an RS485 serial interface, an Ethernet interface, and a number of digital input
and output lines. In addition, the robot can be purchased with several types of optional Precise
peripherals. These include digital cameras, remote I/O, and a hardware manual control pendant.
The controller is programmed by means of a PC connected through Ethernet. There are four
programming modes: a Digital IO (PLC) mode, a Graphical User Programming Mode (Guidance Motion),
an Embedded Language mode (GPL), and a PC Control mode (TCS). When programmed in the PLC,
Graphical User Mode or Embedded Language mode, the PC can be removed after programming is
completed and the controller will operate standalone. The PC is required for operation in the PC Control
mode, which is implemented through a command-server interface.
In all modes of operation, the controller includes a web-based operator interface. This interface is used
for configuring the system, starting and stopping execution, and monitoring its operation. The web
interface can be accessed locally using a browser or remotely via the Internet. This remote interface is of
great benefit in system maintenance and debugging.